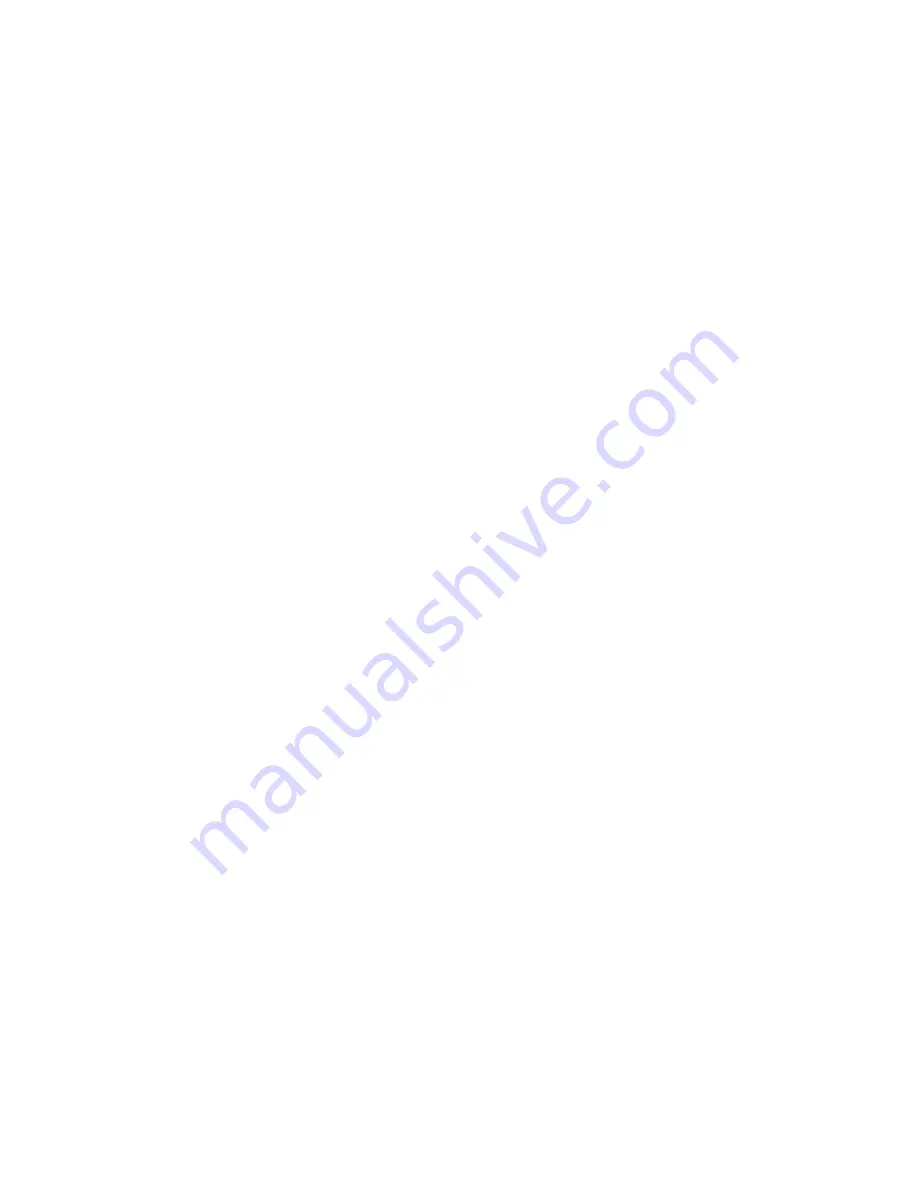
Selecting EV Components
draw. It is not unusual for someone to have a Li powered vehicle that has a 70-90+ mile range, and perform
very well. In part the improved performance is due to the much lower weight of the Li batteries, but also due to
their ability to supply high amperage.
The Controller
In most vehicles being converted a 1,000 Amp or higher controller should be considered. Certainly, 500 Amp
controllers have worked well for many years, and since the older style PbA batteries may have only been
capable of 300 Amps discharge, a 500 Amp controller was sufficient. Indeed, if a vehicle only requires 150
Amps to travel at it's average speed, so the use of a 1,000 Amp controller will not offer any advantages –
EXCEPT at start-up! And, the difference between 500 Amps and 1,000 Amps at start-up can be quite
significant with most motors capable of close to 4 times the torque at 1,000 Amps that they produce at 500
Amps. LiFe batteries exist today that can discharge 4,500 Amps, and the potential of these batteries is
improving rapidly.
If you have a heavy vehicle, you need the higher amperage controllers. Often times, people think it is easier on
a motor to only provide it 500 Amps rather than 1,000 Amps. Though 500 Amps will produce less heat than
1,000 Amps, you must take into consideration whether the amperage will provide the necessary torque the
motor needs to start rotating. If the amperage isn't high enough to start the armature spinning, all of the 500
Amps will be split between just a couple of commutator bars. If the armature doesn't turn it is considered a stall
condition, and the heat build-up can quickly cause a commutator bar to raise. A stall condition is not covered
under warranty, and the condition is quite easily determined by the scorch marks 90 or 180 degrees apart on the
commutator.
The speed that the vehicle will be able to obtain is determined (in part) by the voltage that is delivered to the
motor – not necessarily by the voltage that is delivered to the controller. When a new off-shore manufacturer of
controllers entered the market a few years back, we were swamped by calls from users of this new 120 Volt
1,000 Amp controller who could not get their vehicles over 30 MPH. Users naturally accused the motor of not
being able to power their vehicle, when the actual cause of the problem was that the controller was only able to
deliver 36 Volts to the motor. Volts = RPMs in a nearly linear manner with series wound motors. If the voltage
to the motor doubles, the motor RPMs will double. Since most losses are fixed, the RPMs may increase slightly
more than double.
EV racers found it necessary to build 336 Volt + battery packs due to the fact that 12 Volt PbA batteries would
sag to 5.5 Volts when 1,400 Amps were drawn from them. If the motors are capable of handling 168 Volts, and
the PbA battery pack is 168 Volts nominal, then the motor would only see about 77 Volts when 1,400 was
drawn from the battery pack. In order to deliver the maximum voltage to the motor, it became necessary to
increase the PbA battery pack voltage. As LiFe chemistry battery voltage typically sags far less under heavy
amperage draws (25% vs 50%), the battery pack voltage need not be as high as a comparable PbA battery pack
voltage.
The Motor
Matching all the components of an EV is a critical aspect of any conversion. Choosing batteries that can't
discharge high enough current may mean that the controller won't be able to supply the motor with the
amperage it may need for a particular job. Choosing a controller that can't supply the motor with the current it
needs to perform will likely result in a conversion that doesn't meet expectations. Choosing a battery pack that
is too low a voltage may limit the speed the vehicle is able to attain. Choosing a motor that is too small for a
DRAFT VERSION 1.1
Tue, April 18, 2017 - Copyright© 2015 ,2016,2017 All Rights Reserved,
NetGain Motors, Inc
.
Page 018 of 34 Pages
Summary of Contents for AmP 8
Page 1: ...Owner s Manual for and ...
Page 33: ... ...