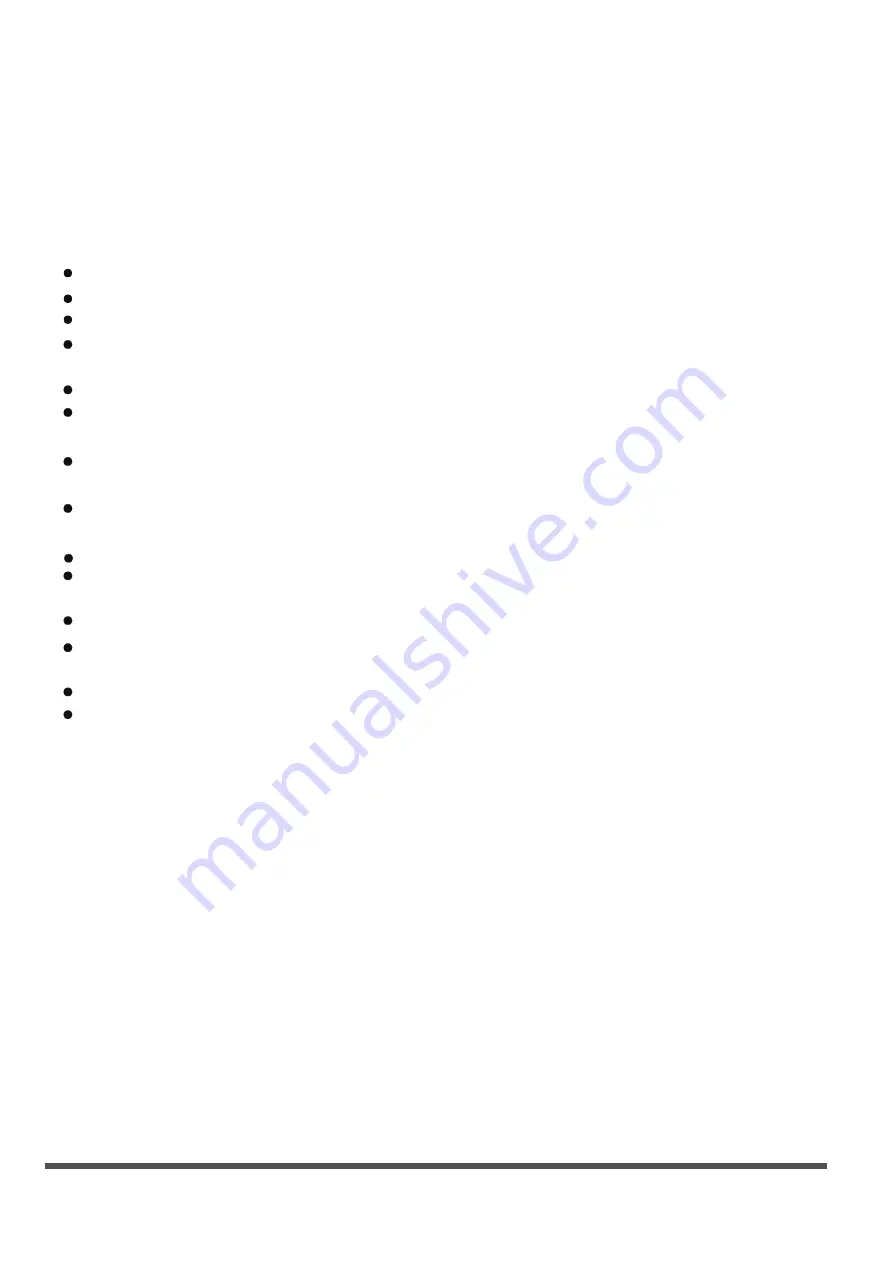
Page 9
20. Venting of HC Refrigerant (R290)
Venting may be carried out as an alternative to recovering the refrigerant. Because HC
refrigerants have no ODP and negligible GWP, under certain circumstances it may be
considered acceptable to vent the refrigerant. However, if this is to be considered, it
should be done in accordance with the relevant national rules or regulations, if they
permit.
In particular, before venting a system, it would be necessary to:
Ensure that legislation relating to waste material has been considered
Ensure that environmental legislation has been considered
Ensure that legislation addressing safety of hazardous substances is satisfied
Venting is only carried out with systems that contain a small quantity of refrigerant,
typically less than 500 g.
Venting to inside a building is not permissible under any circumstances
Venting must not be to a public area, or where people are unaware of the procedure
taking place
The hose must be of sufficient length and diameter such that it will extend to at least 3 m
beyond the outside of the building
The venting should only take place on the certainty that the refrigerant will not get blown
back into any adjacent buildings, and that it will not migrate to a location below ground level
The hose is made of material that is compatible for use with HC refrigerants and oil
A device is used to raise the hose discharge at least 1 m above ground level and so that the
discharge is pointed in an upwards direction (to assist with dilution)
The end of the hose can now discharge and disperse the flammable fumes into the ambient air.
There should not be any restriction or sharp bends within the vent-line which will hinder the
ease of flow.
There must be no sources of ignition near the hose discharge
The hose should be regularly checked to ensure that there are no holes or kinks in it, that
could lead to leakage or blocking of the passage of flow
When carrying out the venting, the flow of refrigerant should be metered using manifold
gauges to a low flow rate, so as to ensure the refrigerant is well diluted. Once the refrigerant
has ceased flowing, if possible, the system should be flushed out with OFN; if not, then the
system should be pressurised with OFN and the venting procedure carried out two or more
times, to ensure that there is minimal HC refrigerant remaining inside the system.
Summary of Contents for Therminator 3.2 Series
Page 3: ...3 8 3 8...
Page 4: ...4...
Page 6: ...6 fresh Fresh defrost Defrost run timer TIMER Clean...
Page 10: ...10 Care and Maintenance 40 C 104 F 1 2 3 4 5 6 7 8 Plasma 10...
Page 12: ...12 ON OFF 3 COOL HEAT FAN HEAT HEAT...
Page 13: ...13 64 5000 ON OFF SILENCE SILENCE SILENCE...
Page 14: ...14 3 3 7 44 5 F 10 E x P x F x EH xx EL xx EC xx PH xx PL xx PC xx...
Page 15: ......
Page 16: ...16...
Page 17: ...17...
Page 18: ...18 Unit Parts 1 2 3 4 5 6 7 8 9 10 11 0 Air break 2 V D...
Page 19: ...19 Indoor Unit Installation 1 2 5 0 2...
Page 20: ...20 3 1 65 2 5 90 3 54 5 7 0 2 0 275 2 A B O 16 5 8 90 3 54...
Page 21: ...21 4 1 2 3 15 6 4 5 6 7 5...
Page 23: ...23 3 15 250VAC T5A 250VAC 1 15 6 U 7 1 3 10 2 3 9 3 4 5 6 7 U 8 9 3 10 L...
Page 24: ...24 8 1 4 2 3 4 5 6 7 1 30 50 1 25 1 95 2 3 4 5 6...
Page 25: ...25 1 1 Outdoor Unit Installation 1 1 1 18 90 Figures below...
Page 26: ...26 2 1 2 3 90 4 1 2 3 M10...
Page 29: ...29 U...
Page 33: ...1 5 9 2 3 4 5 10 5 6 7 3 6 5 9 5 10 33...
Page 34: ...1 2 6 1 34...
Page 36: ...4 36...
Page 37: ...COOL HEAT 30 1 2 ON OFF 3 MODE COOL HEAT 4 5 37...