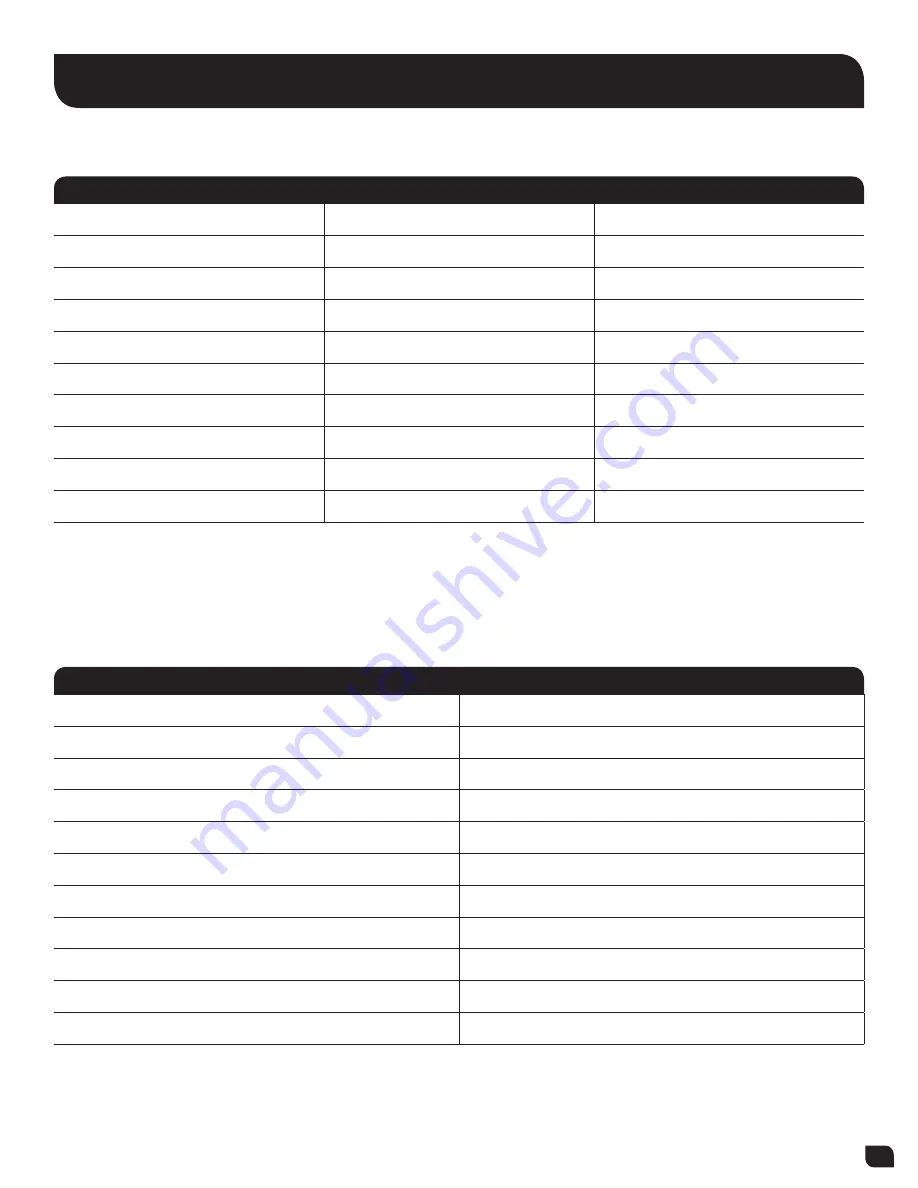
Because the performance of an R.O. Membrane is highly dependent upon pressure, temperature, pH and TDS, the following
should be used for comparison purposes only.
SECTION II. SPECIFICATIONS
Performance
U.S.
Metric
Membrane Production
1
41-53 gpd
155-201 lpd
Membrane TDS Reduction
1
96% Minimum
96% Minimum
System Production²
14 gpd
53 lpd
Recovery Rating²
38%
38%
Efficiency Rating²
22%
22%
TDS Reduction²
90%+ Typical
90%+ Typical
Drain (Reject Water) Flow
3–5 x product Flow
Metric
Empty Storage Tank Precharge
5–7 psig Air
35–48 kPa Air
Performance
1.8 Gallons
6.8 Liters
TABLE A (QUALIFIED PERFORMANCE)
1 Industry standards measure R.O. Membranes performance with no back pressure on the product water, at 65 psig (448kPa) and 77°F (25°C). Further conditions on the above are 250 ppm TDS. Production
rate and TDS reduction figures are for a new Membrane that has been rinsed for 24 hours. The production rate of a new Membrane can decrease by 10% per year or more, depending upon the scaling and
fouling tendencies of the Feed Water.
2 Measured at 50 psig, 77°±2° F, 750±40 mg/l TDS per section 6 of NSF/ANSI Standard 58. Recovery rating means the percentage of the influent water to the membrane portion of the system that is
available to the user as reverse osmosis treated water when the system is operated without a storage tank or when the storage tank is bypassed. Efficiency rating means the percentage of the influent water
to the system that is available to the user as reverse osmosis treated water under operating conditions that approximate typical daily usage. This reverse osmosis system contains a replaceable component
critical to the efficiency of the system. Replacement of the reverse osmosis component should be with one of identical specifications, as defined by the manufacturer, to assure the same efficiency and
contaminant reduction performance.
Specifications
RO-4300RX Membrane
Water Pressure
40–100 psig (280–690 kPa)
TDS
2000 ppm (also mg/l) max.
Temperature
40–100°F (4–38°C)
pH
4–11 (Optimum Rejection At pH 7.0 - 7.5)
Hardness
Less Than 10 gpg (170 mg/l) Or Soften
Iron
Less Than 0.1 ppm (Also mg/l)
Manganese
Less Than 0.05 ppm (Also mg/l)
Hydrogen Sulfide
None
Chlorine
See Note
Bacteria
Must Be Potable**
TABLE B (RECOMMENDED OPERATING LIMITS FOR FEED WATER)
NOTE:
If Chlorine will damage a T.F.C. Membrane. The Sediment/Carbon Pre-Filter has been designed to reduce chlorine from the incoming
water. Change filter every 6 months, more often if the water contains more than 1 ppm chlorine.
** DO NOT USE WITH WATER THAT IS MICROBIOLOGICALLY UNSAFE OR OF UNKNOWN QUALITY, WITHOUT ADEQUATE DISINFECTION BEFORE
OR AFTER THE SYSTEM.
5