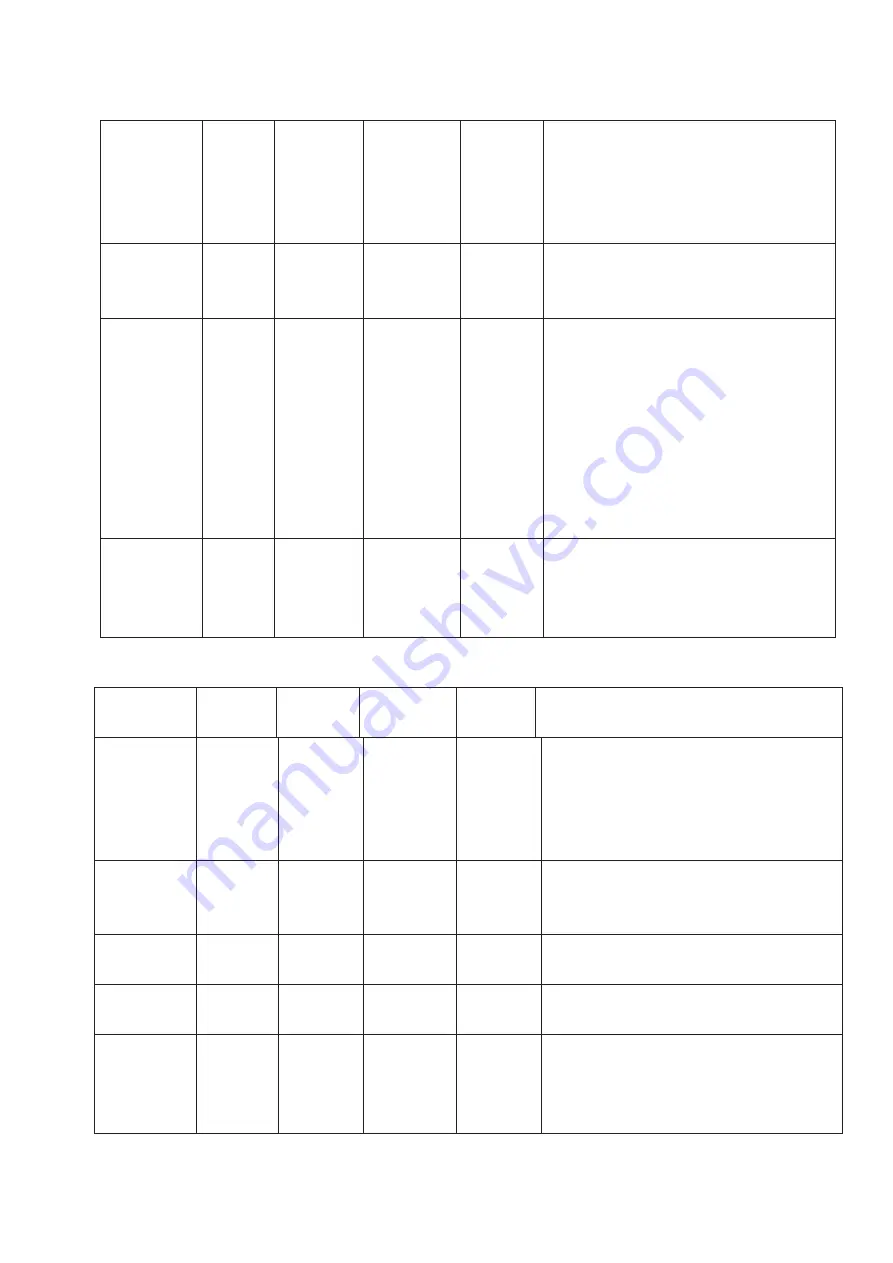
60
rA
-99.0
99
°C/°F(1) -20.0
working
setpoint
during
storage
after
negative
temperature
blast
chilling
(chiller
compartment
temperature)
rb
0
1
---
1
enable negative blast chilling
cycle and storage
1 = yes
rc
0.0
99
°C/°F(1) 5.0
difference
(temperature
detected by the needle probe –
chiller compartment probe” for
the first step when testing the
needle
probe
is
inserted
correctly (refer to paragraph
3.6)
0= test not run (neither the first
nor second step)
rd
1
99
S
60
during the second step of the
test to check that the needle
probe is inserted correctly
(refer to paragraph 3.6)
PARAM MIN.
MAX.
U.M.
DEF.
COMPRESSOR
PROTECTIONS
C0
0
240
min
0
delay in compressor activation
after a cycle has been started;
delay in compressor activation
after the power supply has been
restored.
C1
0
240
Min
5
minimum time between two
consecutive compressor start-
ups.
C2
0
240
Min
3
minimum
duration
of
compressor shut-down
C3
0
240
S
0
minimum
duration
of
compressor start-up
C4
0
240
Min
10
compressor
shut-down
time
during an error alarm chiller
compartment probe when in
storage mode; refer to C5 and