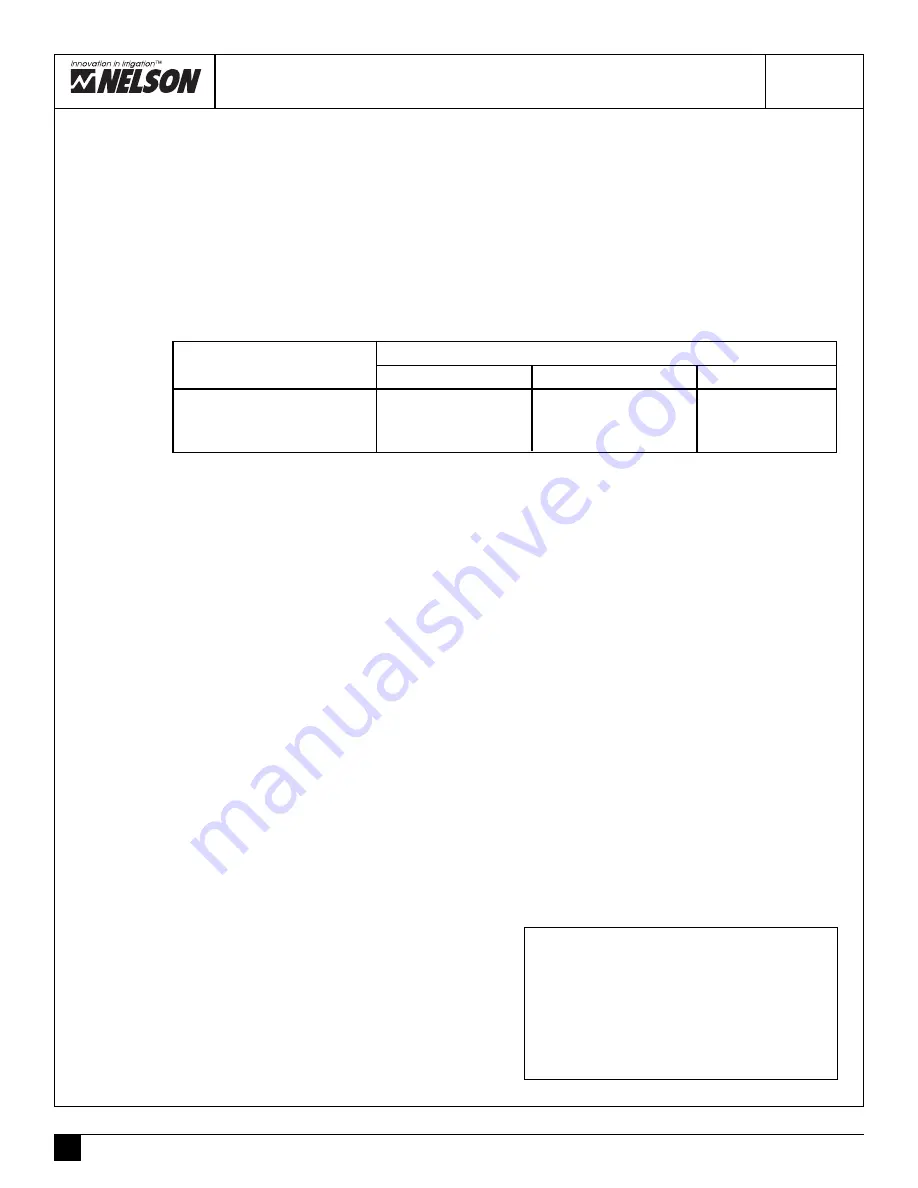
Control Valve
Application
Guide
Nelson Irrigation Corp. 848 Airport Rd. Walla Walla, WA 99362-2271 USA Tel: 509.525.7660 Fax: 509.525.7907 E-mail: [email protected] Web site: www.nelsonirrigation.com
SPECIAL
ON
/
OFF
MODES
Special on/off modes are available on many of the control functions. For a list of the available modes contact the Nelson factory.
Note in Figure 3 the option E80. The hydraulic remote is operated via hydraulic tubing which is run from the controller to the
valve instead of electric wire. The electric solenoid is located near the controller. Wires in the field are minimized. This is used
in areas which have a high potential for lightning damage to the electric system. A special function S10 can also be used to
accomplish the same purpose if infield elevation is minimal (See Appendix D).
2.4.3 PRESSURE CONTROL ACCURACY (SENSITIVITY BUSHING)
The accuracy of the regulating control is a combination of valve friction loss, the slight hysteresis within the regulator and the
sensitivity bushing used in the pressure control. The valve friction loss is dependent upon flow rate. It can be determined from
the loss plot in Graph 1. The overall accuracy of regulation is shown in Table 1 below.
CONTROL
RANGE
ACCURACY
OF
SENSITIVITY
BUSHING
OPTION
SELECTED
SELECTED
RED
BLUE
BLACK
5-50PSI (.3-3.4Bar)
±1PSI (.07Bar)
±1.5PSI (.1Bar)
±2PSI (.13Bar)
10-120PSI (.7-8.3Bar)
±3PSI (.21Bar)
±4.5PSI (.31Bar)
±6PSI (.41Bar)
10-200 PSI (.7-13.8Bar)
±4PSI (.28Bar)
±7PSI (.48Bar)
±9PSI (.62Bar)
For more detail on the sensitivity bushing feature see Section 4.3 and Appendix A.
INSTALLATION HINT: To improve regulator accuracy, avoid installing a pressure tap in a turbulent flow area.
An impeller type flow meter immediately upstream may create turbulence that can cause reduced pressure
control accuracy. For pressure reducing control, a down stream pressure tap at the end of a 24 inch (60 cm)
long straight pipe will help. Also, use of a straight pipe on the upstream end of the valve will help. To be effective
the upstream pipe should be a minimum five pipe diameters long.
3.0 PROPER VALVE SIZING
Proper valve sizing is critical in designing control valve systems. The valves must be sized correctly for the reactive control
functions to work (reducing or sustaining). A high percentage of control valve problems can be directly traced to the initial
selection of the wrong size valve. Be aware of these two common problems:
POTENTIAL PROBLEM #1:
The most common error occurs in over-sizing a pressure control valve. The error occurs by
ignoring the operation and specifying that the size be the same diameter as the pipe. While this simplifies installation,
it may result in the use of a valve that is too large. At lower flow rates this over sizing leads to severe problems such
as cavitation, water hammer and pressure cycling.
POTENTIAL PROBLEM #2:
Almost as common as the above is selecting the control valve from flow graphs. Such graphs
set the limits of minimum and maximum flow rates for each size but the graphs do not account for the pressure drop
across the valve. Since both factors, flow rate and pressure drop, combine to determine the sleeve position both must
be taken into account for the proper sizing of reactive control valves.
Information in the application guide is to aid in avoiding the common problems.
3.1 SIZING SIMPLE ON/OFF VALVES
To size simple on/off valves a designer must look at the valve pressure
rating and then the friction loss. Doing this will assure a valve with
adequate pressure rating is used and also that pressure loss through
the valve will be allowed for in the design.
3.1.1 PRESSURE REQUIRED TO OPEN THE VALVES
The minimum necessary pressure to open the valves is shown in
Table 2, to the right.
Table
1
PROPER VALVE SIZING
Table 2
VALVE RATING
50 PSI
C1 MODEL
begin opening = 2 PSI
fully open = 10 PSI
200 PSI
C2 MODEL
begin opening = 6 PSI
fully open = 28 PSI
80 PSI
C3 MODEL
begin opening = 6 PSI
fully open = 18 PSI
7