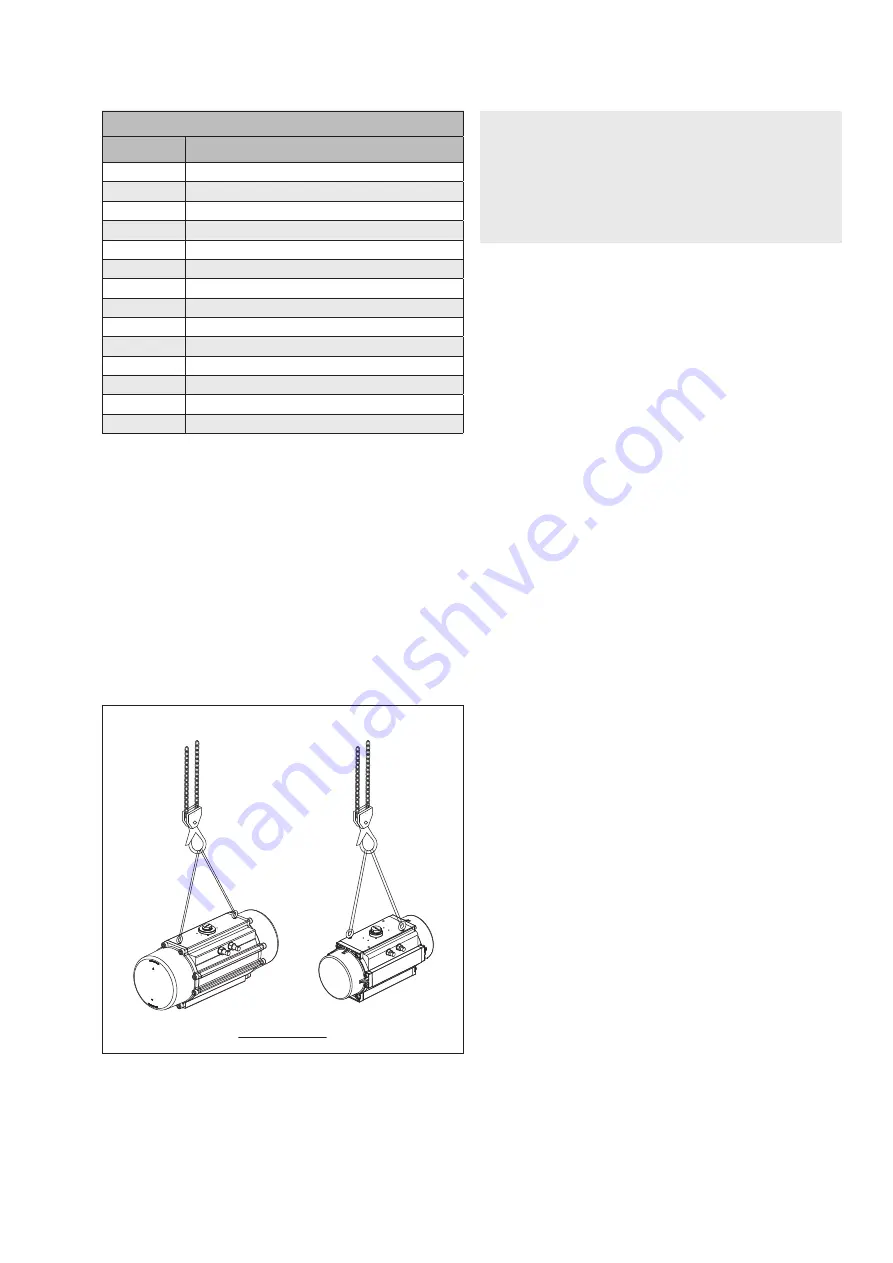
7
IMO-218 EN - Issue 8/2020
Table 4.
Actuator Model Minimum operating time (seconds) for ATEX compliance
RNP 40
0.02
RNP 50
0.02
RNP 63
0.02
RNP 80
0.03
RNP 90
0.03
RNP 100
0.03
RNP 110
0.04
RNP 125
0.04
RNP 150
0.05
RNP 175
0.06
RNP 200
0.06
RNP 250
0.09
RNP 300
0.07
RNP 350
0.09
WARNING:
Valve on which actuator is installed should be earthed properly to
discharge static charge.
2. TRANSPORTATION AND
STORAGE
Make sure that the actuator and associated equipment have not
been damaged during transportation. Store the actuator carefully
before installation, preferably indoors in a dry place. Do not take
it to the installation site or remove the protective caps of ports for
piping until just before installation.
Lift the actuator as shown in Fig. 4: in a horizontal position from the
lifting lugs. Refer to Section 1.4 for weights.
LIFTING ARRANGMENT
RNP 200 / 250
RNP 300 / 350
Figure 4.
Lifting the actuator
Upon receiving the product check the limit actuator and the
accompanying devices for any damage that may have occurred
during transport.
WARNING:
DO NOT USE THE DEVICE IF IT IS DAMAGED DURING
TRANSPORTATION!
IF THE DEVICE HAS SUFFERED DAMAGE DURING
TRANSPORTATION DO NOT INSTALL AND USE IT. IN
CASE OF NOTICING DAMAGE TO THE DEVICE UPON
RECEIVING IT PLEASE CONTACT THE SUPPLIER.
Store the actuator carefully. Storage indoors in a cool, dry place.
Temperature limit for the storing is from 4 °C to 40 °C. The actuator
should be left in its original packing until it is required for the use.
Do not remove protective plugs until installing the actuator.
3. MOUNTING AND
DEMOUNTING
3.1 ACTUATOR GAS SUPPLY
Dry compressed air, nitrogen or natural gas (sweet) can be used
as supply medium, no oil spraying is needed. The air supply
connections are presented in the dimensional drawings in Chapter
9. The maximum supply pressure is depending the selected model.
3.2 INSTALLATION INFORMATION
Before installation please take care of the safety precautions
mentioned in the Section 1.7.
Ensure that the actuator will not be exposed to pressure in excess
to the maximum rating as indicated on the actuator nameplate or
technical documents.
Ensure that throughout the installation that there are no leaks of the
supply media.
The maximum operating temperature for the actuator depends
on individual build of actuator. Refer nameplate for operating
temperature range.
Ensure that the maximum operating temperature as indicated on
the nameplate is not exceeded during operation, transportation or
storage of the actuator.
The environment and surrounding should not affect or limit the
operational safety of the product.
Ensure the product is protected against impact, vibration or any kind
of movement during operation, transportation and storage.
Product should not be installed in hazardous area that is not
compatible with the gas group and temperate class indicated on the
nameplate.
RNP series actuators can be mounted on valve in any desired
position. However it is recommended to align the centerline of the
pneumatic cylinder module along the pipeline.
Ensure proper tightening of fasteners and mounting accessories to
avoid loosening during operation.
All the tubing, fitting and actuation media should be free from
contamination and filtered to the desired level. Quality of media
should be as per ISO 8573-1 [5:3:4]. For additional information
consult Neles.
Ensure proper adjustments of the stopper bolt to desired opening
and closing of the valve.
Summary of Contents for Easyflow RNP Series
Page 27: ...27 IMO 218 EN Issue 8 2020...