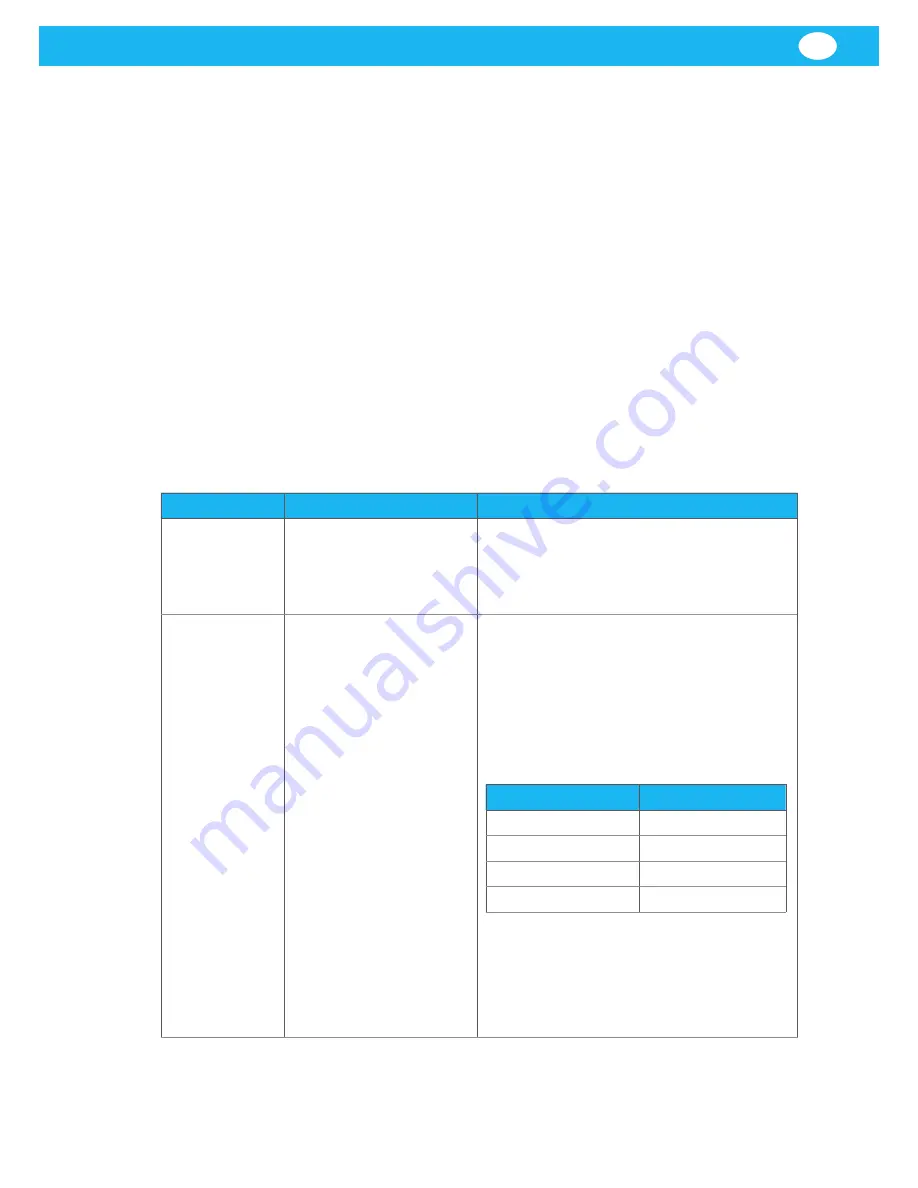
FlexPAK 800/1000
25
EN
7
Troubleshooting
For information on fuses, see Section
‘3.4 Fuses’
and the included electrical diagrams.
There is no over current relay. The frequency converter parameter for maximum current is
adjusted from the factory and is not to be adjusted.
If a fault occurs which cannot be adjusted according to the following descriptions, a
Nederman service technician is to be called.
7.1
Tools
To carry out troubleshooting, it is necessary to have a multimeter with V DC and ohm
measuring capabilities.
7.2
Remove the lid of the start and control unit
Remove the lid as follows:
1.
Unscrew the four plastics screws in the corner of the control cabinet.
2.
Lift of the lid.
3.
Identify the PLC and the terminals in the bottom of the cabinet.
Table 7-1: Trouble shooting guide
Error
Possible cause
Solution
The unit
unexpectedly goes
directly into Running
mode when the
Standby/Running
button is pressed.
•
A valve at a workstation is open
and its micro switch is activated
•
The PS cable is damaged with
its wires short-circuited
If the PS cable is damaged, press the Standby/Running
button to put the unit into Off mode and investigate the
fault. If necessary, loosen the PS cable from the control
unit, see the electrical diagrams, and use an ohmmeter
across the leads in turn to locate the fault.
Defect PT100
temperature sensor.
Check whether the PT100 sensor is defective as follows:
1. Disconnect the PT100 sensor wire from terminal 77 and
measure the resistance between terminal 78 and the
disconnected sensor wire.
2. Measure the resistance in the sensor using an
ohmmeter. The values in the table below are standard
values, so a deviation from the measured value is
normal. If the averaged output (in ohm) deviates more
than ±2% from these values, the sensor will need to be
replaced.
Temperature (°C)
Averaged output (ohm)
0
100
20
110
80
131
135
150
If the sensor has a resistance >150 ohm, there will be a
high temperature alarm. To check whether the sensor
input is working correctly, disconnect the PT100 wire at
terminal 77 and connect a jumper between terminals 77
and 78. Press the OK button on the PLC to reset the alert.
If the alert disappears, the PT100 sensor input is working,
and the PT100 the sensor will need to be replaced.
Summary of Contents for FlexPAK 800
Page 2: ...FlexPAK 800 1000 2...
Page 3: ...FlexPAK 800 1000 3 Figures 4 English 11...
Page 6: ...FlexPAK 800 1000 6 1 2 3 4 5 6 7 14 13 12 11 9 8 10 7 6...
Page 8: ...FlexPAK 800 1000 8 9 10 1643 1mm 65 662 1mm 26 2 1771 4 1mm 70 2 1 4 5 6 8 7 9 3 1...
Page 9: ...FlexPAK 800 1000 9 11 12 14 13...
Page 10: ...FlexPAK 800 1000 10 1 0 m 39 4 A B C 16 17 15 Min 2 1m 83 A A A A C...
Page 32: ...FlexPAK 800 1000 EN 32...
Page 33: ......
Page 34: ...www nederman com...