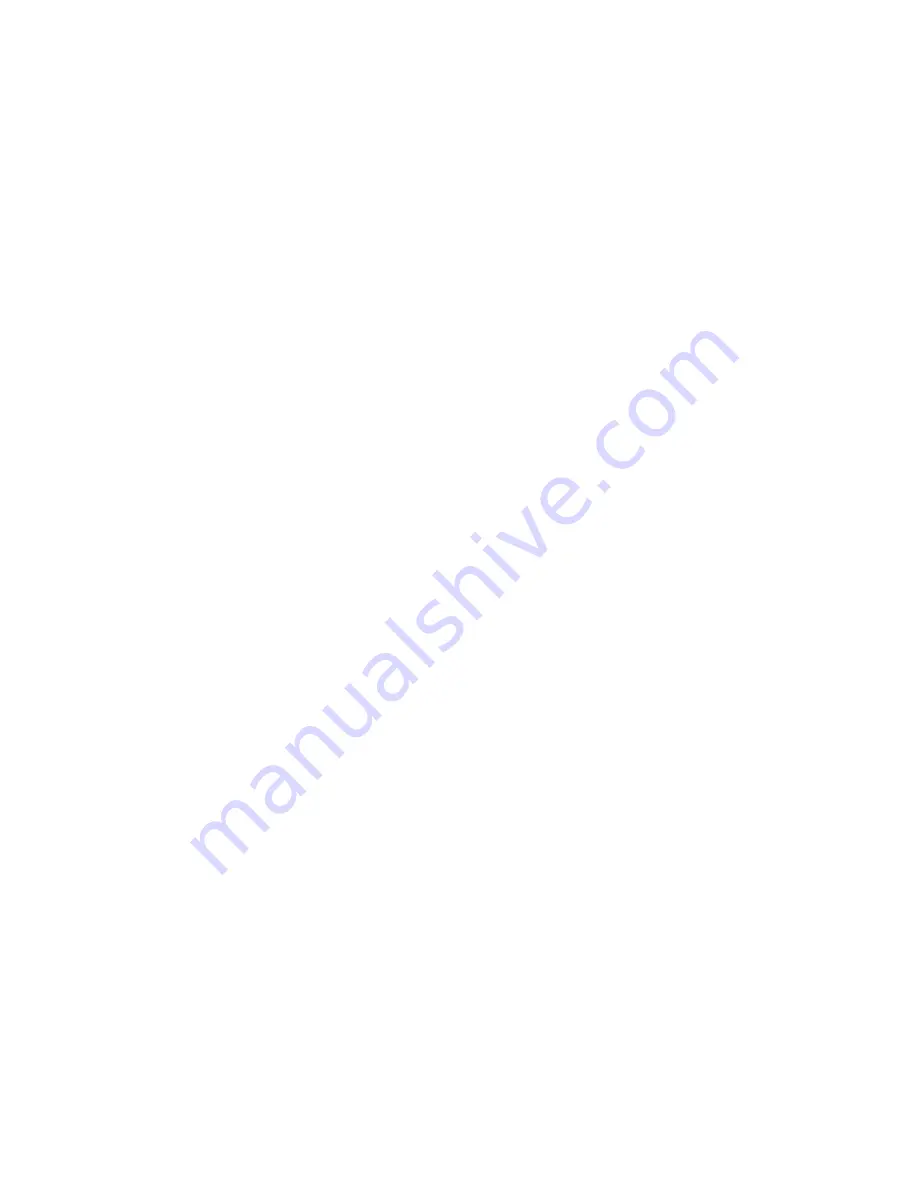
14
14
While the discussion below pertains to applications in metals, there are numerous applications to
a wide variety of engineering materials. For plastics, glasses and other more or less isotropic or
homogeneous materials, the procedures are similar to those for metals. Major differences in testing
nonmetals are in the velocity of sound and different impedance characteristics. Fiber-reinforced
composite materials are characteristically anisotropic, having different acoustical properties in
different directions, and often require specialized transducers and procedures for satisfactory
ultrasonic testing results.
In general, however, many of the transducer selection factors outlined below apply for nonmetals,
but additional experimentation may be required. NDT Systems, Inc. engineers have extensive
experience in ultrasonic testing of many materials and can provide assistance when called upon.
The following suggestions are by no means fully comprehensive or mandatory. Alternative ap-
proaches may produce essentially the same results. The operator should experiment to determine the
best transducer for given applications or contact NDT Systems, Inc. for advice.
Thickness Gaging Applications.
Thickness Ranges
Metals with Thicknesses Ranging from 0.008 inch to Approximately 0.750 inch (0.2 to 20.0
millimeters). In this range, there are overlapping considerations that will dictate which type of
transducer will produce the desired results. Foremost is the limitation of the minimum thickness
that can be resolved by different types of transducers.
Single Element, Delay Line Transducers.
Some highly damped, high frequency transducers of this type are capable of producing fully
resolved multiple back echos equivalent to as little as 0.005 inch (0.13mm) in steel having smooth
surfaces. However, such transducers will be relatively expensive and not readily attainable.
Standard inexpensive delay line transducers, highly damped, in the frequency range of 10 to 20
MHZ, will ordinarily produce good results down to approximately 0.008 inch (0.20mm). Given
smooth surfaces in metals having relatively low attenuation, like wrought steel or aluminum, such
transducers can be used to gage up to 0.75 inch (20mm), more or less, depending upon the
length of the delay line.
To determine the practical minimum thickness resolution of a delay line transducer, it is necessary
to have an array of thin shims ranging in thickness around the desired minimum to be measured.
Inexpensive sets of steel shims, used as feeler gages, can be obtained from well equipped
hardware stores, automotive parts houses or specialty tool suppliers. The nominal thickness is
typically imprinted onto each shim, often in inches and millimeters. Available sets contain as many
as 15 or 20 shims, ranging from 0.005 to 0.025 inch (0.13 to 0.64mm) thick. While we have found
that the stated thickness is nominal, subject to variation up to ±0.0004 inch (0.01mm), these shims
can be used to readily determine the minimum thickness that can be expected from a given
transducer.
Under ideal conditions, parts having very smooth, parallel surfaces can be measured to an
accuracy approaching ±0.0001 (±0.003mm). To achieve such accuracy, not only is it necessary
to have an appropriate transducer, the thickness gaging instrument must have extremely stable,
high speed electronic circuitry. TG400 fulfills this requirement admirably. For a procedure to
demonstrate this capability, see Section 4.3.2.3, below.
Single Element, Focused Immersion Transducers.
Some transducers of this type have been designed specifically for precision thickness gaging of
metals 0.010 inch (0.25mm) thick and greater. Small diameter, high frequency, short-focused
immersion transducers also can be used to measure the distance to quite small internal reflectors.