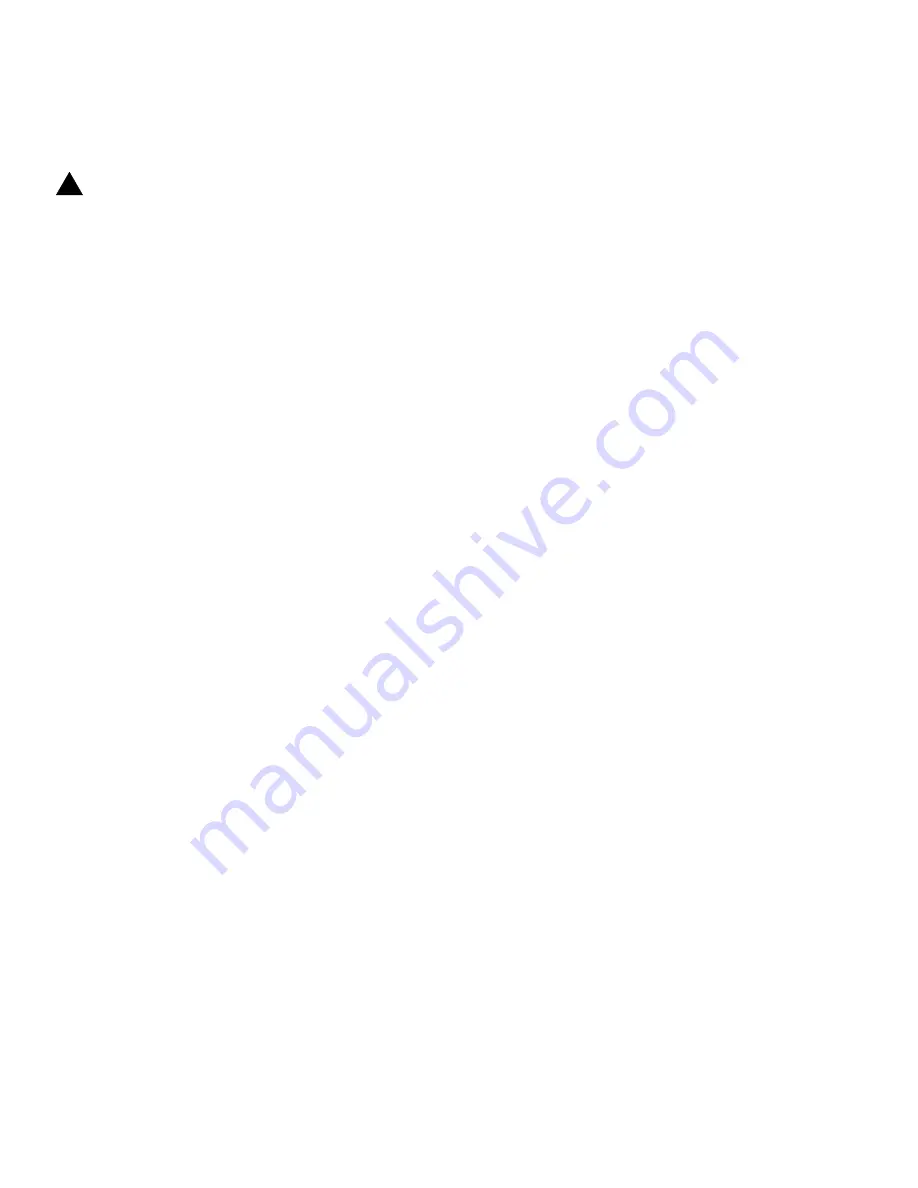
13
REPLACEMENT PROCEDURE SKILL LEVEL
Level I :
Low - very little mechanical knowledge or exposure.
Level II :
Intermediate - some experience with mechanical procedures
Level III :
Advanced - knowledgeable about mechanical procedures
!
Disconnect all power to the machine before you service it.
When disposing of old parts, obey the applicable local and provincial requirements.
For instructions to replace the following parts, please refer to the Assembly Manual for your bike:
• AC Adapter
• Seat
• Seat Post
• Front Stabilizer
• Rear Stabilizer
• Water Bottle Holder