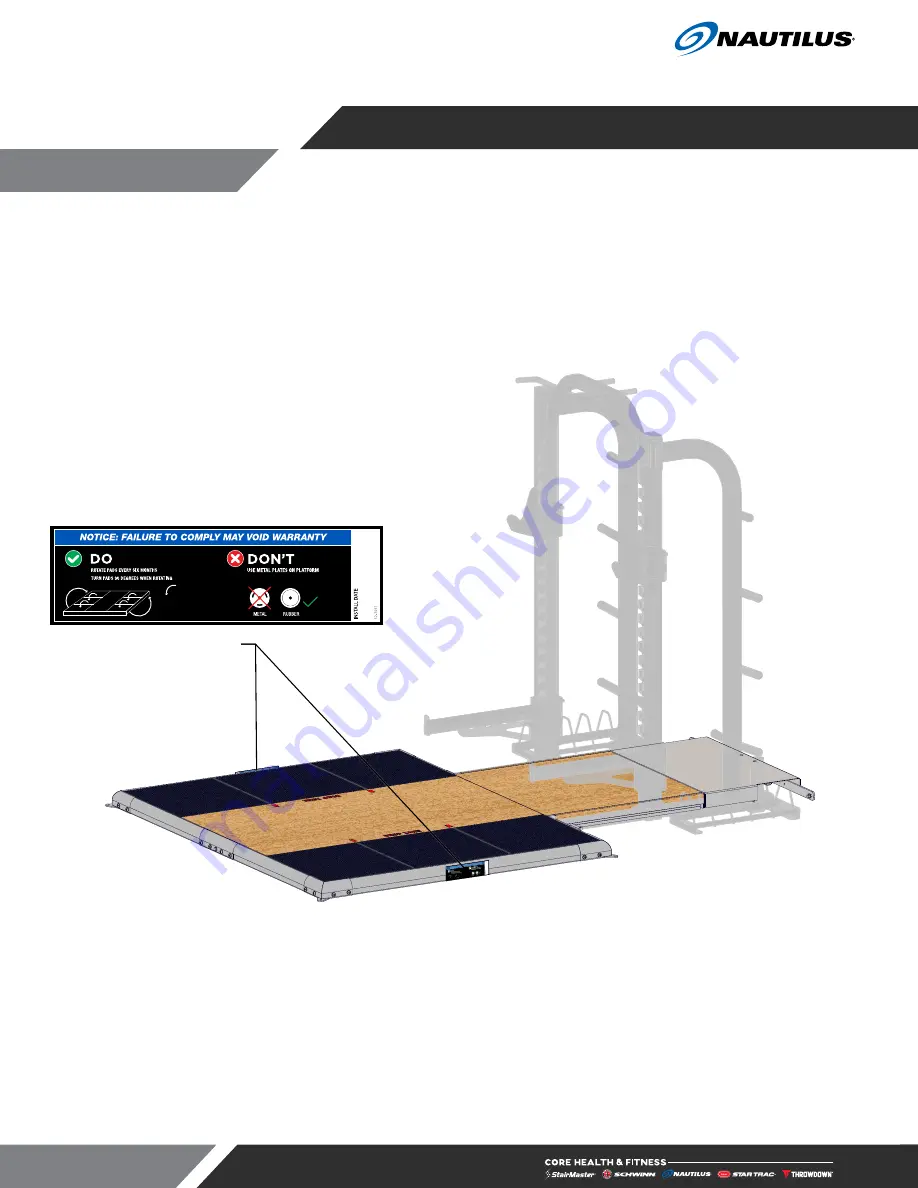
Page 4
This page shows examples of the warning labels and communication stickers placed on the equipment as part of the manufacturing process. It is critical that own-
ers maintain the integrity and placement of these stickers. If you find any stickers missing or damaged the replacement numbers are shown on the support site.
See Support and Service to order replacements. NOTE: STICKERS AND LABELS ARE NOT SHOWN TO SCALE
N12-7051
IMPORTANT LABEL LOCATIONS
Fig. 2