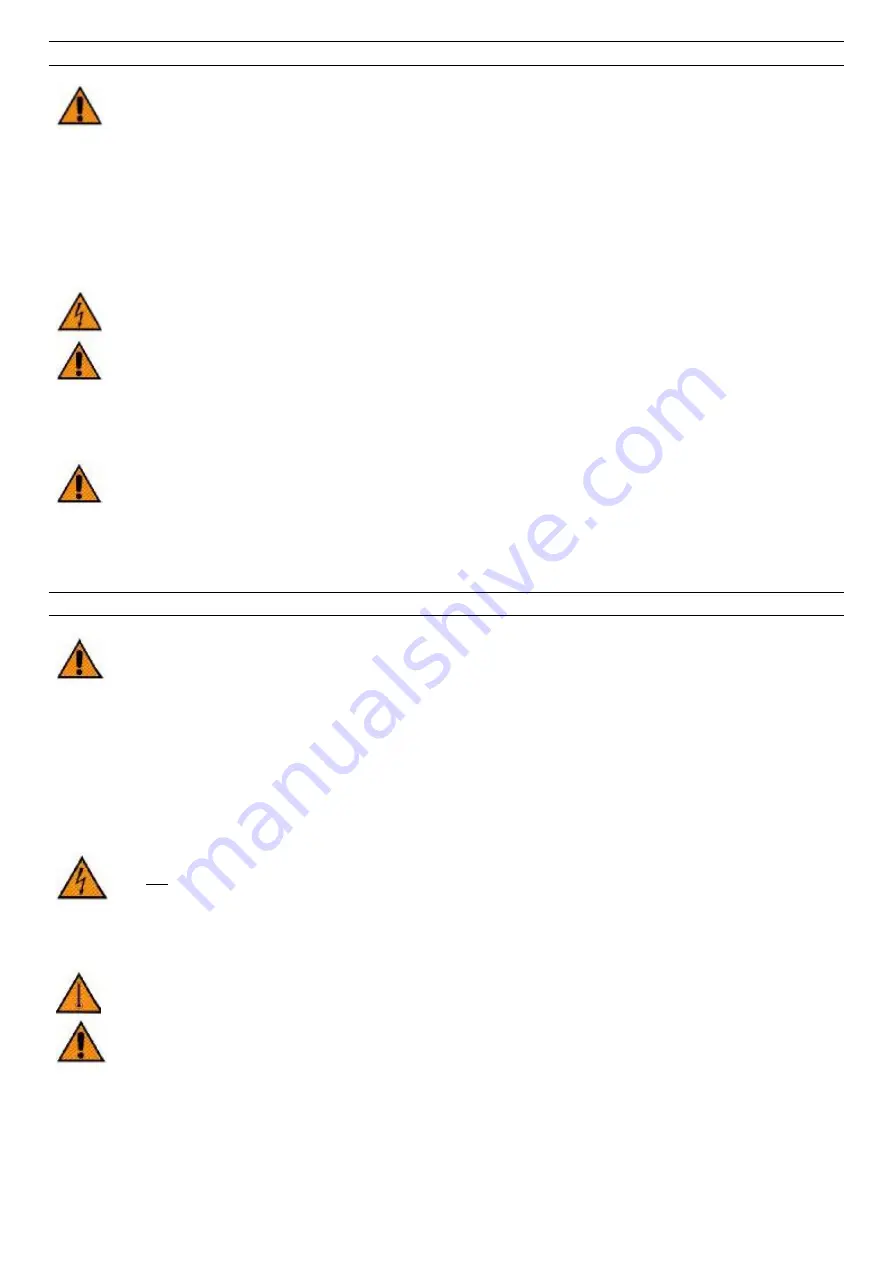
26
8.
DISPOSAL
All work on the chiller may only be carried out by specialist personnel!
Follow this procedure if you need to shut down the chiller:
- Stop the chiller and permanently isolate it from the electricity mains.
- Disconnect the power cable.
- Open the bypass valves (if present) for the liquid circuit and isolate the chiller from the circuit by closing the stop
valves for the feed and return lines at the inlet and outlet as necessary.
- Disconnect the chiller from the cooling medium lines.
- Empty the tank and the internal cooling medium circuits.
- If the chiller has to be dispatched, use the original or similar packaging and keep the chiller in an upright position.
Before carrying out any work on the electrical parts, make sure that the main switch interrupts
the electricity supply to the chiller and then affix appropriate warning signs to avoid the ma-
chine being reconnected to the electricity mains!
Please consult the contents and the safety instructions in the relevant sections of these instruc-
tions for details of the correct handling and storage of the chiller.
Remove the residual cooling medium from the chiller in a manner appropriate to its properties and in accordance
with the legislation in force.
If the chiller has to be disposed of:
Never open the sealed cooling assembly (compressor, evaporator and condenser) if there may
be any refrigerant or lubricating oil present!
Send the chiller to an approved waste disposal company in accordance with current environmental protection legis-
lation.
The other materials/waste constituents must be treated in line with the provisions of the valid legislation.
9.
MALFUNCTIONS/TROUBLESHOOTING
All service and maintenance operations may only be carried out by specialized personnel!
If you have to take off or dismantle any components or assemblies, remove them and handle them with suitable
tools.
A number of possible problems are listed in the following table, together with notes on the causes and recommen-
dations on which remedial measures can be carried out.
Some of these operations are classified as extraordinary maintenance work and may require access to internal
parts of the chiller and the removal of some parts.
The table in Section 10.3 of these instructions shows which components weigh more than 20 kg.
You will find further information on safety precautions in the general warnings at the start of these instructions.
Please note the following warnings in particular:
Do not remove (even only partially) the protective panels of the chiller unless it is necessary!
If the protective panels still have to be removed, disconnect the chiller from its energy sources (electricity and wa-
ter), and affix a sign stating
”
Maintenance work on chiller in progress
’
on the operating panel.
Replace the protective panels afterwards as quickly as possible.
Wait at least 15 minutes before removing the protective panels so that the chiller can cool
down. Certain internal components have a very high and dangerous operating temperature!
Never open the sealed cooling assembly (compressor, evaporator and condenser) if there may
be any refrigerant or lubricating oil present!
Never carry out any welding or soldering on the cooling system when it contains refrigerant in order to avoid the
risk of generating toxic substances.
Summary of Contents for PCGE Series
Page 69: ...69 11 2 WIRING DIAGRAM MODELS PCGE 11 to PCGE 25 PCGEZ 08 230V 1Ph 50Hz POWER COMMAND DIAGRAM...
Page 70: ...70 MODEL PCGE 28 230V 1Ph 50Hz POWER COMMAND DIAGRAM...
Page 71: ...71 MODEL PCGE 28 400V 3Ph 50Hz POWER COMMAND DIAGRAM...
Page 72: ...72 MODELS PCGE 31 to PCGE 41 OCGE 31 to OCGE 41 230V 1Ph 50Hz POWER SECTION...
Page 73: ...73 MODELS PCGE 31 to PCGE 41 OCGE 31 to OCGE 41 230V 1Ph 50Hz COMMAND SECTION...
Page 78: ...78 MODELS PCGE 590 to PCGE 3300 PCGEZ 360 to PCGEZ 480 400V 3Ph 50Hz...
Page 79: ...79...
Page 80: ...80...
Page 81: ...81...
Page 86: ...86 MODEL PCGE 1100 with tank and pump MODEL PCGE 1300 with tank and pump...
Page 87: ...87 MODEL PCGE 1900 2200 with tank and pump MODEL PCGE 2900 3300 with tank and pump...
Page 89: ...89 MODELS PCGE 370 to PCGE 520 PCGEZ 180 to PCGEZ 300 without tank MODEL PCGE 590 without tank...
Page 91: ...91 MODEL PCGE 1100 without tank MODEL PCGE 1300 without tank...
Page 92: ...92 MODEL PCGE 1900 2200 without tank MODEL PCGE 2900 3300 without tank...
Page 97: ...97 710 1789 00 00 02B 07 05 2008...
Page 166: ...69 11 2 WIRING DIAGRAM MODELS PCGE 11 to PCGE 25 PCGEZ 08 230V 1Ph 50Hz POWER COMMAND DIAGRAM...
Page 167: ...70 MODEL PCGE 28 230V 1Ph 50Hz POWER COMMAND DIAGRAM...
Page 168: ...71 MODEL PCGE 28 400V 3Ph 50Hz POWER COMMAND DIAGRAM...
Page 169: ...72 MODELS PCGE 31 to PCGE 41 OCGE 31 to OCGE 41 230V 1Ph 50Hz POWER SECTION...
Page 170: ...73 MODELS PCGE 31 to PCGE 41 OCGE 31 to OCGE 41 230V 1Ph 50Hz COMMAND SECTION...
Page 175: ...78 MODELS PCGE 590 to PCGE 3300 PCGEZ 360 to PCGEZ 480 400V 3Ph 50Hz...
Page 176: ...79...
Page 177: ...80...
Page 178: ...81...
Page 183: ...86 MODEL PCGE 1100 with tank and pump MODEL PCGE 1300 with tank and pump...
Page 184: ...87 MODEL PCGE 1900 2200 with tank and pump MODEL PCGE 2900 3300 with tank and pump...
Page 186: ...89 MODELS PCGE 370 to PCGE 520 PCGEZ 180 to PCGEZ 300 without tank MODEL PCGE 590 without tank...
Page 188: ...91 MODEL PCGE 1100 without tank MODEL PCGE 1300 without tank...
Page 189: ...92 MODEL PCGE 1900 2200 without tank MODEL PCGE 2900 3300 without tank...
Page 194: ...97 710 1789 00 00 02B 07 05 2008...