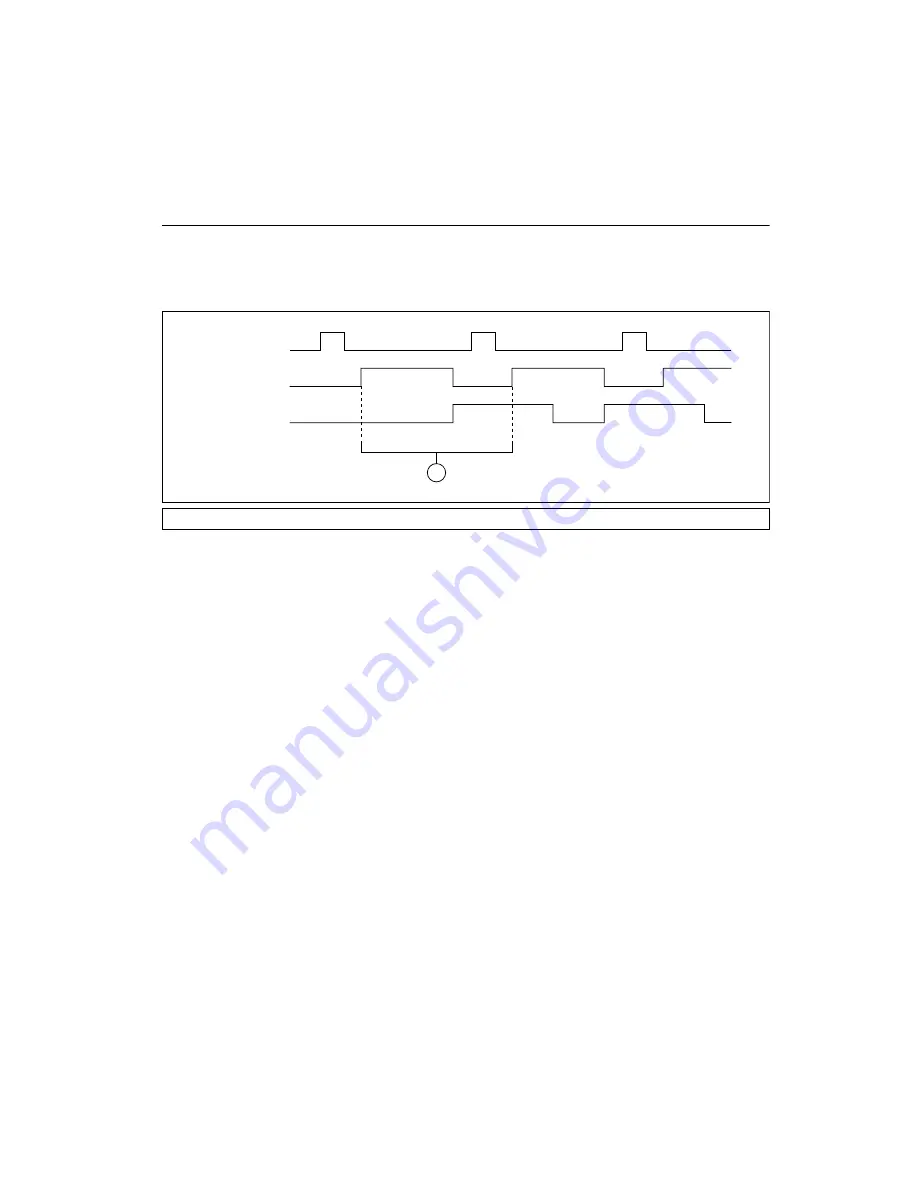
Chapter 6
Image Acquisition
©
National Instruments Corporation
6-5
NI 177x Smart Camera User Manual
Maximum Frame Rate
Frame rate is the inverse of the frame period. The frame period is the time
from the start of exposure on one frame to the start of exposure on the next
frame, as shown in Figure 6-2.
Figure 6-2.
Frame Period
The frame period is affected by the following factors:
•
Exposure time, as described in the
section of this chapter
•
Trigger delay, as described in the
section of this
chapter
Determining the Maximum Frame Rate
You can determine the maximum frame rate for your configuration in
software by reading the
Max Frame Rate
indicator in Vision Builder AI,
reading the
AcquisitionFrameRateLimit
attribute in LabVIEW, or
reading the
Max Frame Rate
indicator in MAX.
When external triggering is enabled, do not trigger faster than the
maximum frame rate. If a trigger occurs faster than the maximum frame
rate, the camera exhibits the following behavior. If an incoming trigger is
received during exposure, the incoming trigger is ignored. If an incoming
trigger is received during readout, the trigger is delayed until readout
concludes.
1
Frame Period
Trigger
Expo
su
re
Im
a
ge Re
a
do
u
t
1