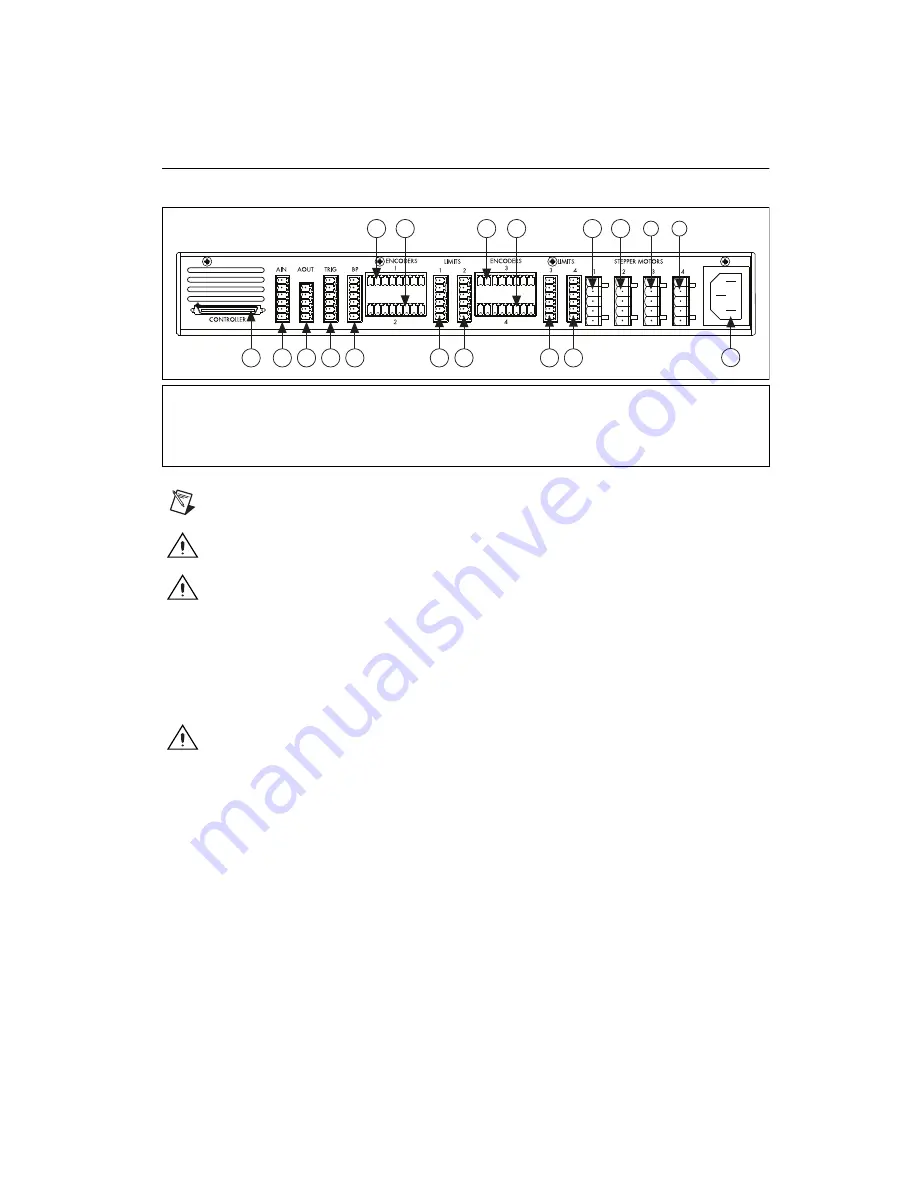
©
National Instruments Corporation
7
MID-7604/7602 Stepper Power Motor Drive User Guide
Back Panel Connector Wiring
Figure 2 shows the connectors located on the back panel of your MID-7604/7602.
Figure 2.
MID-7604/7602 Back Panel Connectors
Note
Items followed by an asterisk (*) are available on the MID-7604 only.
Caution
Be sure to turn off the ENABLE switch and the main AC power to your MID-7604/7602
and host computer
before
connecting the accessory to your motion controller.
Caution
The stepper motor connectors on this drive are energized when the unit is powered
on. Disconnect the MID-7604/7602 unit from the power outlet
before
connecting wires to or
disconnecting wires from the stepper connectors. Strip back the insulation of the stepper wires to the
stepper connectors no more than 7 mm.
Failure to do so could result in electric shock leading to
serious bodily injury or death.
1.
Use the interface cable to connect the motion controller to the MID-7604/7602. Wire the motor
power, limit switch, encoder, and I/O terminal blocks as described in this guide and to your specific
system requirements.
Caution
You
must
change the MID-7604/7602 main input fuse on the front panel if you change the
line voltage from the factory setting. Refer to the
section of this guide for fuse
specifications.
2.
Use the
LINE VOLTAGE SELECT
switch to configure the MID-7604/7602 for 115 VAC, 60 Hz
or 230 VAC, 50 Hz operation. For proper operation, you must set this switch to match your power
source.
3.
Finally, install the power cord into the back panel AC connector and plug it in to a correctly rated
power source.
1
Motion Controller Connector
2
Analog Input Connector
3
Analog Output Connector
4
Trigger Connector
5
Breakpoint Connector
6
AC Power
Encoder Connectors
7
Axis 1
8
Axis 2
9
Axis 3*
10 Axis 4*
Limit Connectors
11 Axis 1
12 Axis 2
13 Axis 3*
14 Axis 4*
Motor Connectors
15 Axis 1
16 Axis 2
17 Axis 3*
18 Axis 4*
1
4
11
12
8
9
7
10
1
3
14
6
15
16
17
1
8
5
3
2