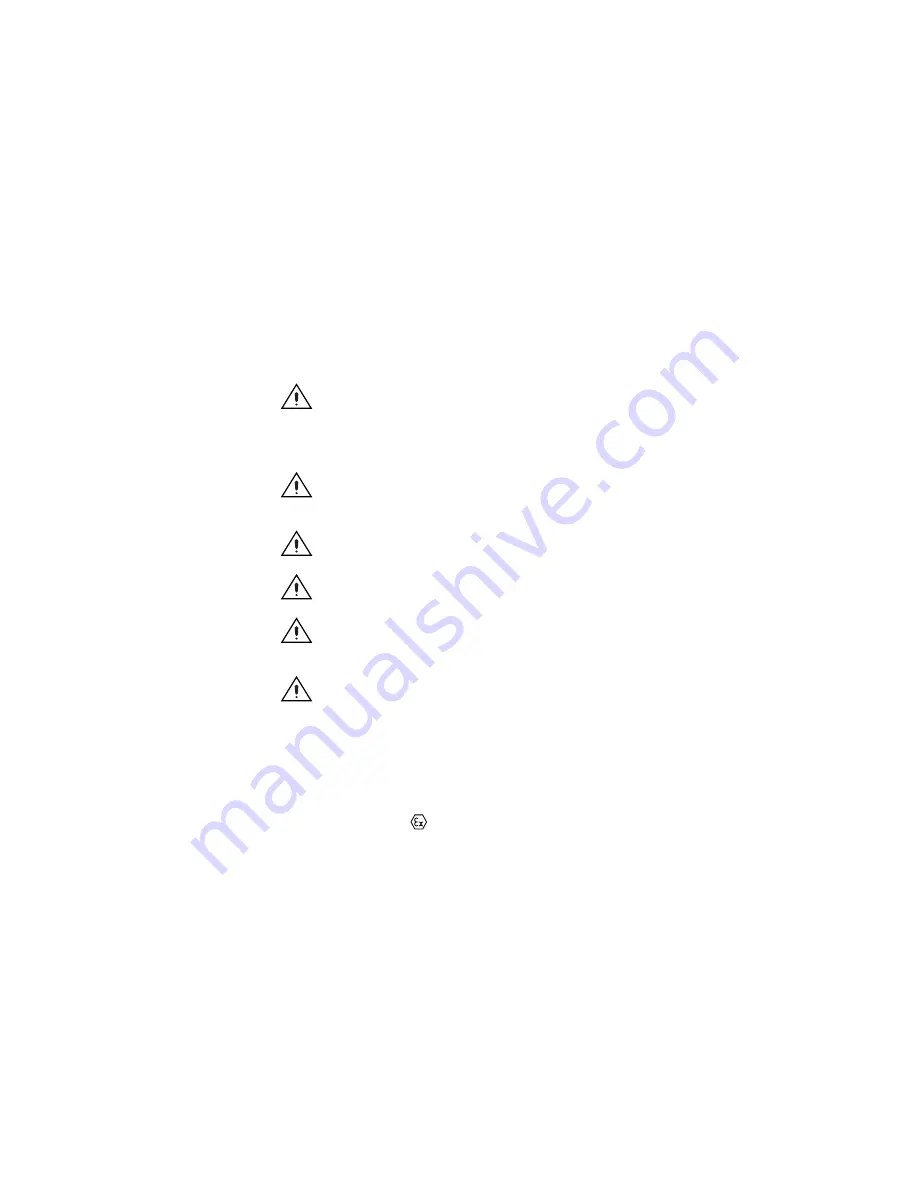
©
National Instruments Corp.
11
FP-PWM-520 and cFP-PWM-520
Safety Guidelines for Hazardous Locations
The cFP-PWM-520 is suitable for use in Class I, Division 2,
Groups A, B, C, D, T4 hazardous locations; Class I, Zone 2,
AEx nC IIC T4 and Ex nC IIC T4 hazardous locations; and
nonhazardous locations only. Follow these guidelines if you are
installing the cFP-PWM-520 in a potentially explosive
environment. Failing to follow these guidelines may result in
serious injury or death.
Caution
Make sure that all products you use in hazardous
locations are certified for such use. Refer to the product
label or visit
ni.com/certification
, search by model
number or product line, and click the appropriate link in
the Certification column.
Caution
Do
not
disconnect I/O-side wires or connectors
unless power has been switched off or the area is known
to be nonhazardous.
Caution
Do
not
remove modules unless power has been
switched off or the area is known to be nonhazardous.
Caution
Substitution of components may impair
suitability for Class I, Division 2.
Caution
For Zone 2 applications, install the Compact
FieldPoint system in an enclosure rated to at least IP 54
as defined by IEC 60529 and EN 60529.
Caution
For Zone 2 applications, install a protection
device across the external power supply and the COM
terminal. The device must prevent the external power
supply voltage from exceeding 42 V if there is a transient
overvoltage condition.
Special Conditions for Hazardous Locations Use in Europe
The cFP-PWM-520 has been evaluated as EEx nC IIC T4
equipment under DEMKO Certificate No. 03 ATEX 0251502X.
Each module is marked
II 3G and is suitable for use in Zone 2
hazardous locations.