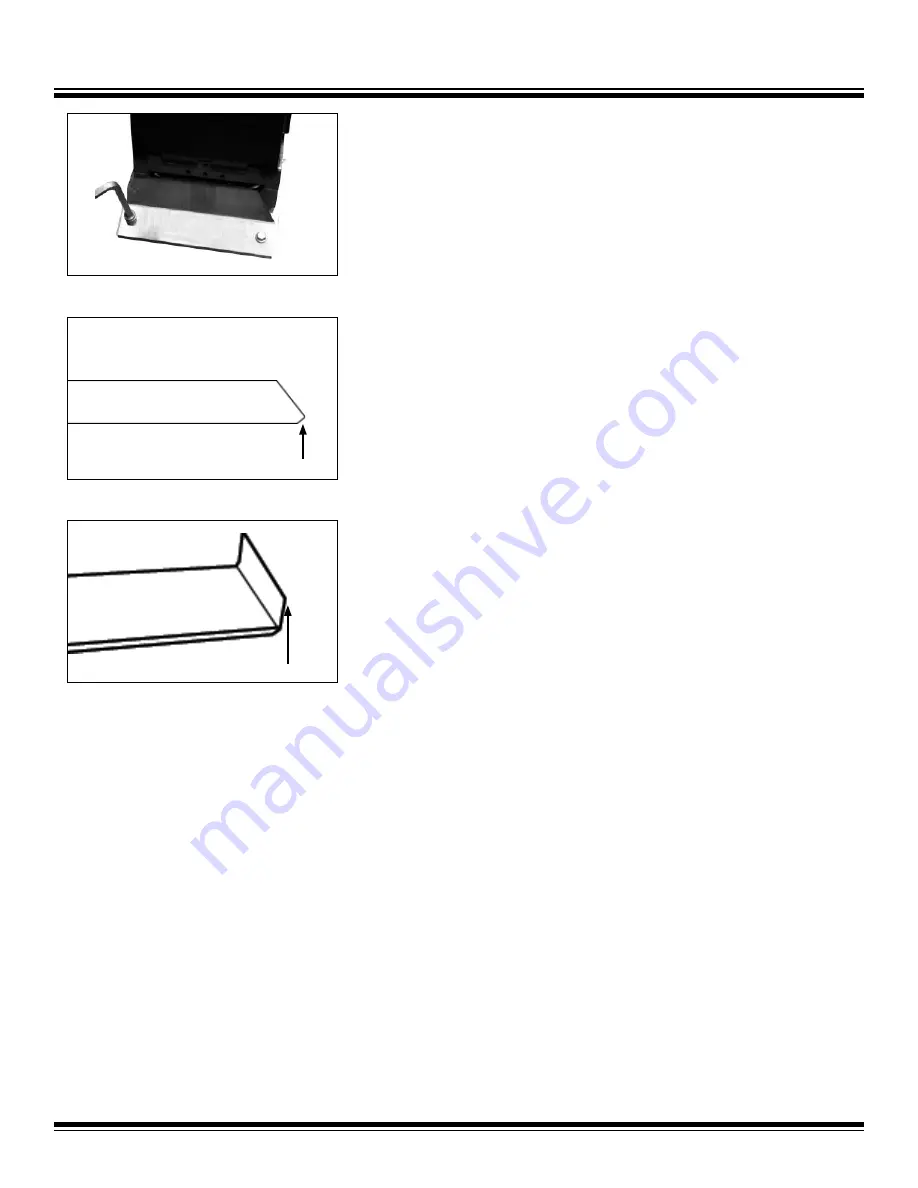
Machine Operation
FIG. M
APPLICATION SET-UP
VCT TILE
Never use a blade wider than the size of the tile being removed. If goods being removed
still do not come up clean or machine jumps on top of goods, reduce blade size to a
smaller blade until proper blade size is found or use a smaller portion of the blade.
PURE VINYL RUBBER TILE
Goods will need to be scored down to 25.4 to 30.5 cm (10” to 12”) for proper removal.
Self scoring blades can be used with some materials. A 25.4 cm (10”) blade is recom-
mended for this product, but determine what size blade works best.
DIRECT GLUED CARPET
Can be done with either self scoring blades or pre-score carpet to blade width prior to
stripping with #584 Scoring Tool. Pre-scored carpet makes machine easier to control
and blades stay sharper longer. Blades up to 40.6 cm (16”) wide can be used. Normally
30.5 to 35.6 cm (12” to 14”) blades are used on direct glued carpet, secondary backed,
unitary, double glued, vinyl foam, urethane foam. Latex foams come up easily with a 16”
blade.
CONCRETE
When working on concrete slab, normal blade position is bevel up for best performance,
especially when cleaning adhesive. On occasion, bevel down gives better blade life. Test
each job for best performance.
GIBCRETE AND SOFT POURED FLOORING
Requires blade bevel down to create a better wearing surface.
BLADE SHARPENING
Dull blades greatly reduce cutting ability. Re-sharpen or replace as needed. In use,
blades develop a back-bevel (Figure N). When re-sharpening, blade will not be truly
sharp until all back-bevel is gone.
NOTE: THINNER BLADES ARE EASIER TO SHARPEN, BUT THEY ALSO BREAK EASIER.
•
Always wear gloves and safety glasses.
•
Grind blade using a 10.2 cm (4”) diameter disk with 120 or fi ner grit. Be careful not
•
to catch disk on edge or corner of blade.
•
Pass grinder along blade edge starting on one end and continuing in one direction
being careful to hold grinder at proper angle of blade. Grind until sharp.
•
Using a good quality fi ne tooth hand fi le, use same procedure as above.
•
Blades are sharp. Use extreme caution.
•
Have plenty of sharp blades on each job so on-the-job blade sharpening is elimi-
nated.
•
It is best to resharpen dull blades on proper bench or belt grinder in the shop, so
the blades are ready for the next job.
SELF-SCORING BLADE SHARPENING
It is important to keep the “wings” on a self-scoring blade sharp (Figure O). Use a fi le on
the “wing” edge. Sharpen the fl at part of the blade, the same way as described above.
FIG. N
FIG. O
Fax: 763-535-8255
12
FRONT OF BLADE
BACK BEVEL
FRONT OF BLADE
SELF-SCORING WING
Summary of Contents for 5280-AUS
Page 32: ......