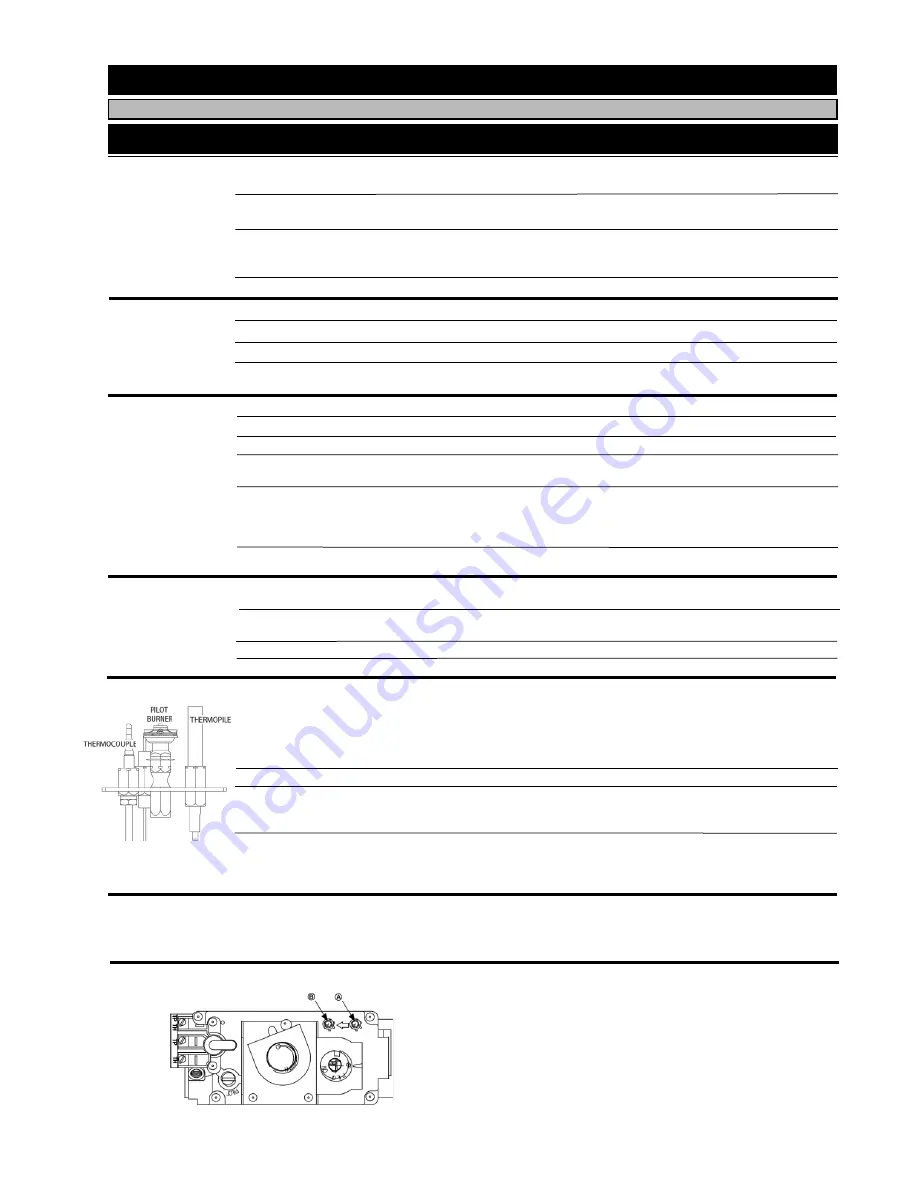
27
W415-0381 / H / 12.07.07
Pilot will not light.
- check if pilot can be lit by a match
- check that the wire is connected to the push button igniter.
- check if the push button igniter needs tightening.
- replace the wire if the wire insulation is broken or frayed.
- replace the electrode if the ceramic insulator is cracked or broken.
- replace the push button igniter.
No spark at pilot burner
- fi ll the tank.
Out of propane gas
Spark gap is incorrect
- spark gap should be 0.150" to 0.175" (5/32" to 11/64" approx.) from the electrode
tip and the pilot burner. To ensure proper electrode location, tighten securing nut
(fi nger tight plus 1/4 turn).
No gas at the pilot burner
- check that the manual valve is turned on.
- check the pilot orifi ce for blockage.
- replace the valve.
- call the gas distributor.
Main burner goes out;
pilot stays on.
Pilot fl ame is not large enough or
not engulfi ng the thermopile
- turn up pilot fl ame.
- replace pilot assembly.
Thermopile shorting
- clean thermopile connection to the valve. Reconnect.
- replace thermopile / valve.
Remote wall switch wire is too
long; too much resistance in the
system.
- shorten wire to correct length or wire gauge.
Faulty thermostat or switch.
- replace.
5" fl exible vent has become dis-
connected from fi replace.
Pilot goes out when the
gas knob is released.
The gas valve has
an interlock device
which will not allow
the pilot burner to be
lit until the thermo-
couple has cooled.
Allow approximately
60 seconds for the
t h e r m o c o u p l e t o
cool.
System is not correctly purged.
- purge the gas line with the glass door removed.
Out of propane gas.
- fi ll the tank.
Pilot fl ame is not large enough
- turn up the pilot fl ame.
- gently twist the pilot head to improve the fl ame pattern around the thermo-
couple.
Pilot fl ame is not engulfi ng the
thermocouple.
Thermocouple shorting / faulty.
- loosen and tighten thermocouple.
- clean thermocouple and valve connection.
- replace thermocouple.
- replace valve.
Faulty valve.
- replace.
Pilot burning; no gas
to main burner; gas
knob is on 'HI'; wall
switch / thermostat
is on.
Thermostat or switch is defec-
tive.
- connect a jumper wire across the wall switch terminals; if main burner lights,
replace switch / thermostat.
Main burner orifi ce is plugged.
- remove stoppage in orifi ce.
Faulty valve.
- replace.
Wall switch wiring is defective.
- disconnect the switch wires & connect a jumper wire across terminals 1 & 3; if
the main burner lights, check the wires for defects and / or replace wires.
Main burner goes out;
pilot goes out.
Refer to "MAIN BURNER GOES OUT; PILOT STAYS ON"
Vent is blocked
Vent is re-circulating
- check for vent blockage.
- check joint seals and installation.
- re-attach to fi replace.
TROUBLE SHOOTING GUIDE
SYMPTOM
PROBLEM
TEST SOLUTION
B
EFORE
ATTEMPTING
TO
TROUBLESHOOT
,
PURGE
YOUR
UNIT
AND
INITIALLY
LIGHT
THE
PILOT
AND
THE
MAIN
BURNER
WITH
THE
GLASS
DOOR
REMOVED
.
Flames are consist-
ently too large or too
small. Carboning oc-
curs.
- check pressure readings:
Inlet pressure can be checked by turning screw (A) counter-clockwise 2 or 3
turns and then placing pressure gauge tubing over the test point. Gauge should
read 7" (minimum 4.5") water column for natural gas or 13" (11" minimum) water
column for propane. Check that main burner is operating on "HI".
Outlet pressure can be checked the same as above using screw (B). Gauge
should read 3.5" water column for natural gas or 10" water column for propane.
Check that main burner is operating on "HI".
AFTER TAKING PRESSURE READINGS, BE SURE TO TURN SCREWS CLOCK-
WISE FIRMLY TO RESEAL. DO NOT OVERTORQUE.
Leak test with a soap and water solution.
Unit is over-fi red or under-fi red.
Pilot goes out while
standing; Main burner
is in 'OFF' position.
Gas piping is undersized.
- turn on all gas appliances and see if pilot fl ame fl utters, diminishes or extin-
guishes, especially when main burner ignites. Monitor appliance supply working
pressure.
- check if supply piping size is to code. Correct all undersized piping.