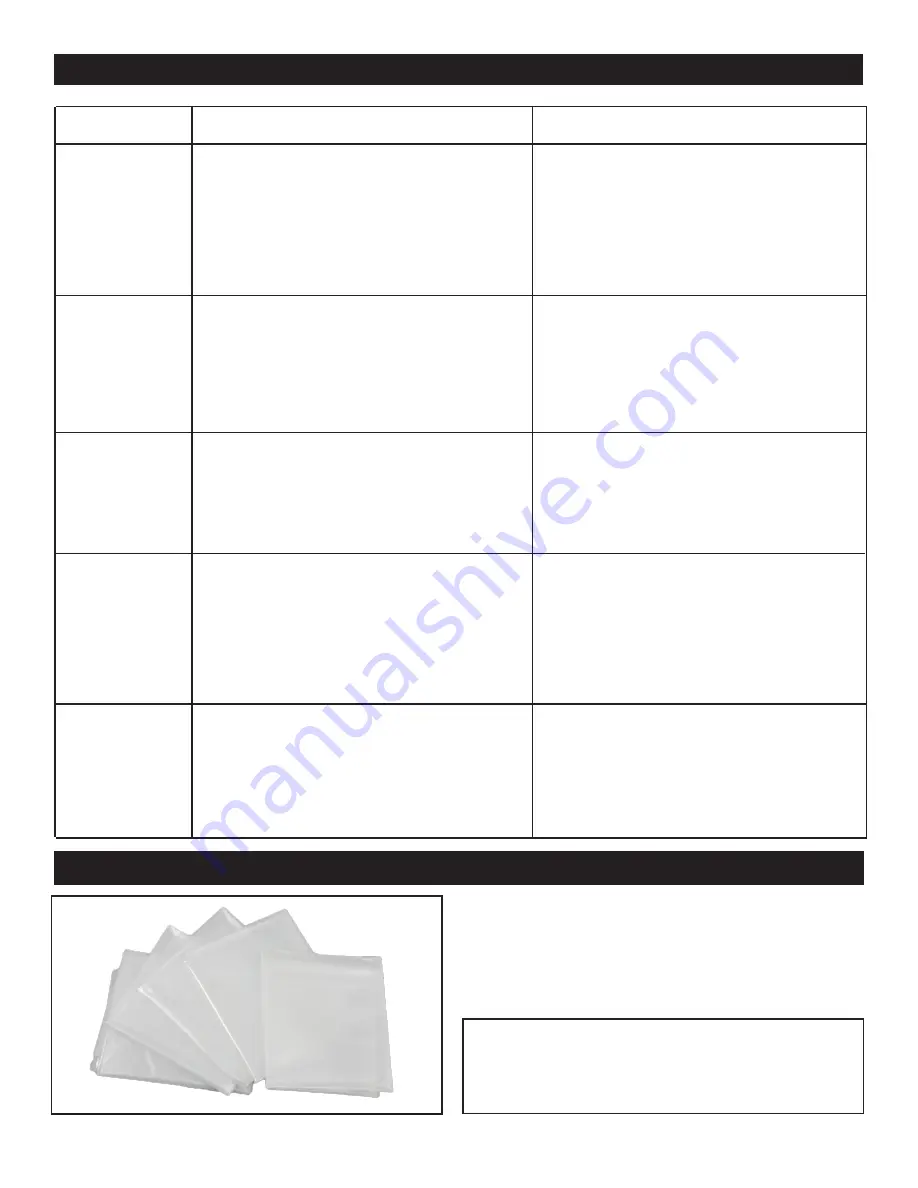
TROUBLESHOOTING
PROBLEM
POSSIBLE CAUSE
SOLUTION
Reduction of
dust collection
suction power
Loud or unusual
noises from
motor or fan
1. Malfunction of the filter cleaning system.
2. Plugged hose lines.
3. Retaining of dust in the collector due to low
density.
4. Wetting of filter.
5. Filter is dirty or permeability of the cloth
has increased.
1. Check all system components.
2. Check and clean inlets and hoses for
obstructions.
3. Clean or replace filter and check all
connections for leakage.
4. Control intake of moisture. Dry wet filter.
5. Clean or replace filter.
1. Motor, fan housing, base or parts of the
frame are loose.
2. Impeller fan is rubbing the housing.
3. Motor bearings are loud.
4. Impeller fan is loose, unbalanced, or
damaged.
1. Inspect and tighten all parts or replace as
needed.
2. Check position of the fan and adjust or
replace any loose/damaged parts.
3. Replace worn bearings.
4. Secure fan on motor shaft, and replace if
any damage is found.
1. Incorrect line voltage.
2. Motor capacitor has failed.
3. Extension cord is being used.
4. Impeller is clogged with debris.
1. Restricted air flow due to dirty filter or
blockage in the hoses.
2. Motor overloaded.
3. Extension cord is used.
4. Machine used for extended time.
5. Poor air flow in work area.
1. Have qualified electrician check circuit
for proper line voltage.
2. Replace motor capacitor.
3. Do not use an extension cord. Plug the
collector directly into an outlet.
4. Clean debris from blocked impeller.
1. Clean filter and hoses for maximum air
flow through the system.
2. Reduce load on the motor.
3. Do not use an extension cord. Plug the
collector directly into an outlet.
4. Reduce run time of machine.
5. Reposition machine for better air flow.
Motor stalls or
does not have
full power
Motor runs hot
Motor does not
start
1. Machine not plugged in.
2. Power switch in ‘OFF’ position.
3. Power switch or cord is faulty.
4. Fuse or circuit breaker are open.
5. Low line voltage.
6. Defective motor capacitor.
7. Motor does not wo
rk.
1. Plug cord into electrical outlet.
2. Lift switch to ‘ON’ position. The safety
key must be in place. See page 11.
3. Replace switch or cord.
4. Correct overloaded electrical circuit.
5. Correct low line voltage condition.
6. Replace motor capacitor.
7. Repair or replace the motor.
ACCESSORIES
CLEAR PLASTIC BAGS - PACK OF 5 EACH
60-910 Dust Bucket Bag for RIKON 60-1750
60-911 Filter Element Plastic Bag for 60-1750
60-913 Dust Bucket Bag for RIKON 60-2500
60-91
2
Filter Element Plastic Bag for 60-2500
To order replacement parts or accessories for the
Cyclone Dust Collectors or other RIKON machines,
contact your local RIKON Distributor, or visit the
RIKON website at www.rikontools.com.
8