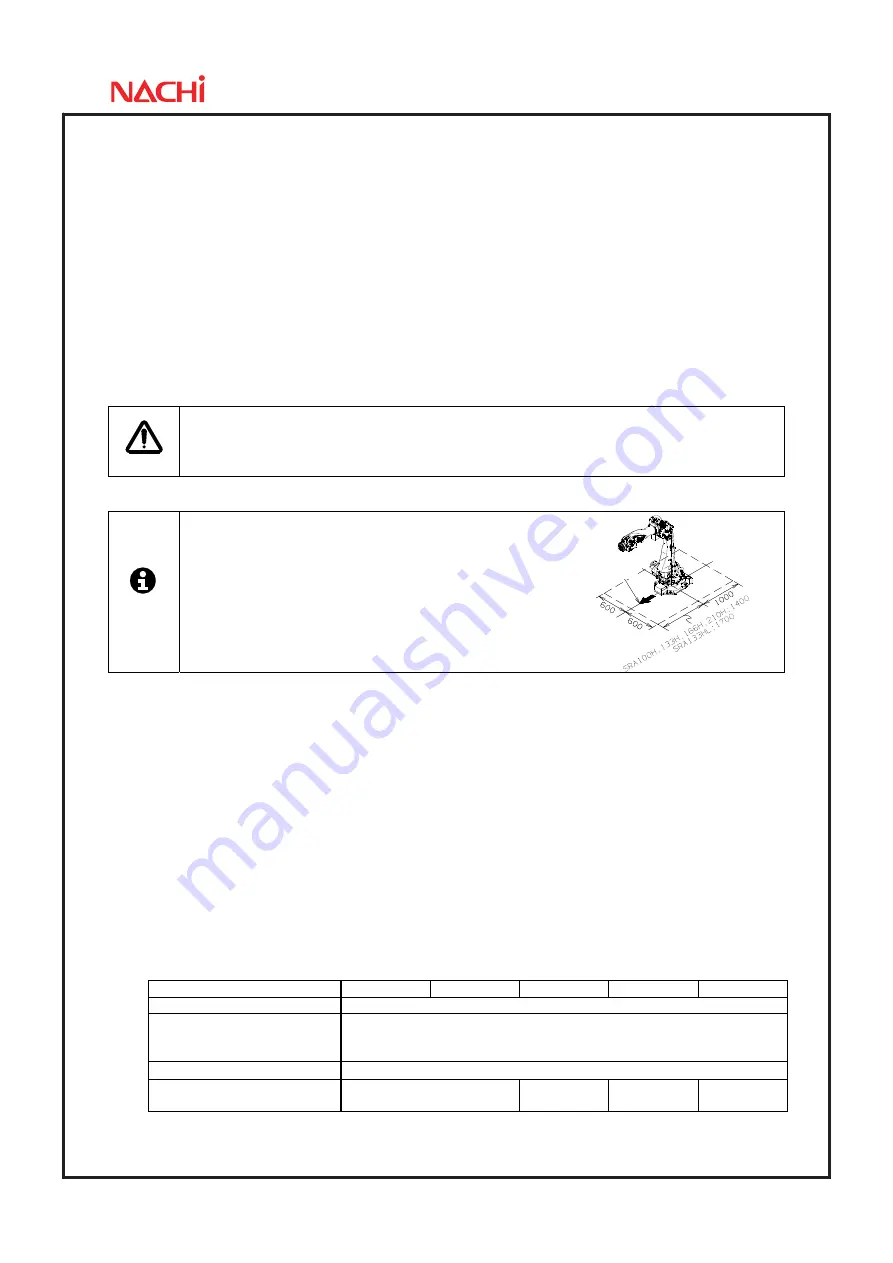
Page-8
5. Installation procedure
The installation location and the installation procedure of the robot are critical factors to maintain robot
functions. The ambient conditions of installation location not only have influence on the life of mechanical
sections of the robot, but also get involved in safety issues. Consequently, strictly observe the
environmental conditions shown below. Furthermore, utmost care should be exerted for the installation
procedure and the foundation for the robot in order to maintain the robot performance. Strictly observe
the installation procedure for the robot provided below.
Installation
To install the robot, give it first priority to thoroughly consider safety of workers and take safety
measures. The following describes precautions for this purpose.
Safety measures against entry in the robot operating area
WARNING
While the robot is in operation, workers are in danger of coming in contact with the
robot. To avoid that, install a
guard fence
so as to keep the worker away from the robot.
Not doing so will cause the workers or other persons to accidentally enter the operating
area, thus resulting in accidents.
■
Space surrounding robot
IMPORTANT
When installing this robot, open space written
in figure is necessary for maintenance work such
as motor replacement, balancer replacement and
other work.
■
Installation location and ambient conditions
Conditions (temperature, humidity, height and vibration) are written in “2. Basic Specifications”.
Further ambient conditions listed below must be observed.
(1) Location with the drainage structure so that swivel base is not flooded, when the liquid such
as water or cutting fluid is splashed on the robot body
(2) Location with no flammable or corrosive fluid or gas.
(3) Type D grounding (the grounding resistance is 100
Ω
or less) is necessary.
■
Installation procedure
While robot moves, large reaction force is applied to the swiveling base from all directions.
Consequently, the robot should be installed in such a manner that the foundation endures not
only the static loads but also the reaction force caused by robot movement.
Repair uneven spots, cracks, and others on the floor, and then install the robot by following to
the table below. If thickness of floor concrete is less than needed level, an independent
foundation should be constructed. Inspect the foundation prior to the robot installation, and then
construct the foundation, if necessary.
Robot Model
SRA100H-01 SRA133H-01 SRA166H-01 SRA210H-01
SRA133HL-01
Thickness of floor concrete
Not less than 160 mm
Installation parts *1
8 bolts of M20 (JIS: Strength class 12.9) not less than 65mm
8 plain washers of not less than 4.5 mm in thickness
and HRC35 in hardness
Tightening torque *2
560
±
30 N
m
Allowable repeated tensile *3
Approx.
22,000 N
Approx.
28,000 N
Approx.
30,000 N
Approx.
28,000 N
*1 : Installation parts are not accessory of robot.
*2 : Apply a coating of lubricating oil to the threaded parts of bolts, and then tighten bolts by using torque wrench to the
specified tightening torque.
*3 : This tensile is per installation bolt when robot is installed with all bolts written in table above.
Axis1 = 0 degree
Summary of Contents for SRA-H Series
Page 1: ...Standard specifications SRA H 01 FD11 SRA HL 01 FD11 6th edition 1608 SSRAEN 071 006 001 ...
Page 5: ...Page 3 3 Robot dimensions and working envelope SRA100H 01 SRA133H 01 ...
Page 6: ...Page 4 SRA166H 01 SRA210H 01 ...
Page 7: ...Page 5 SRA133HL 01 ...
Page 14: ...Page 12 SRA166H 01 SRA210H 01 ...
Page 16: ...Page 14 SRA166H 01 SRA210H 01 Axis 4 5 Axis 6 Axis 4 5 Axis 6 ...
Page 19: ...Page 17 SRA133HL 01 When wrist load is 133kg ...
Page 29: ......