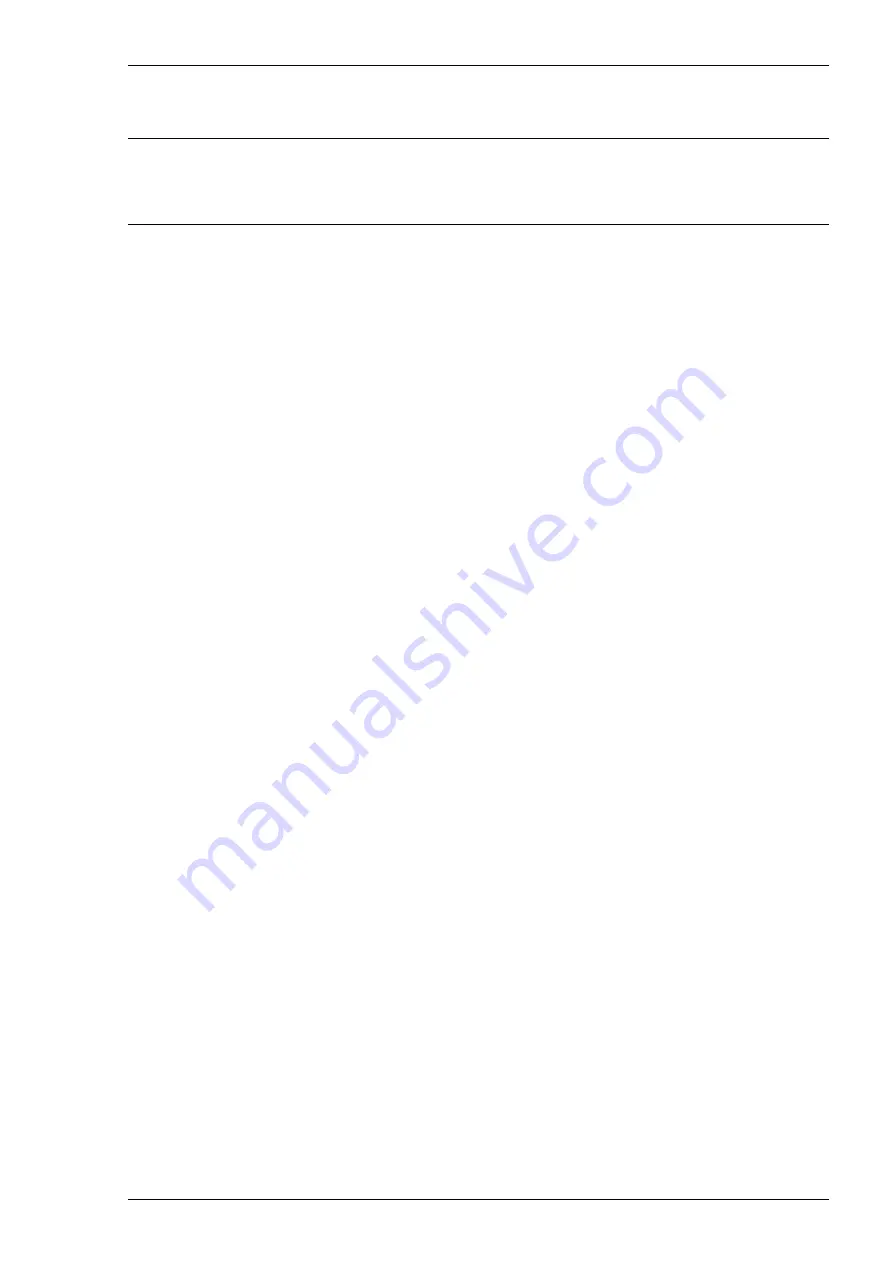
MYDATA
MY500 JetPrinter
Routine Maintenance
P-030-0014-EN – Service Manual
Rev. 0003 2008-06
5 - 9
Monthly Maintenance
This preventive maintenance shall only be carried out by authorized service
engineers.
Equipment
– Lint-free cloths.
– Vacuum cleaner or blow nozzle.
Machine
– Remove dust from the ventilation areas on the top back hood.
Use a vacuum cleaner or an air blow nozzle.
Optional Refrigerated Air Dryer
– Remove dust from the ventilation area on the optional Refrigerated
Air dryer. Use a vacuum cleaner or an air blow nozzle.
– Check valves for scratches, gouges, abrasion, and corrosion.
– Check tubes and valves for air leakage.
– Check tubes for twisting, flattening, or distortion.
– Check tubes for hardening, deterioration, or softness.
Replace components as necessary. Refer to the Refrigerated Air Dryer
manual.
Summary of Contents for MY500 JetPrinter
Page 1: ...MY500 JetPrinter Service Manual English For a fast changing world P 030 0014 EN...
Page 2: ......
Page 10: ...Preface MY500JetPrinter MYDATA viii Rev 0003 2008 06 P 030 0014 EN Service Manual...
Page 24: ...Safety MY500JetPrinter MYDATA 1 14 Rev 0003 2008 06 P 030 0014 EN Service Manual...
Page 75: ...MYDATA MY500JetPrinter Machine Systems P 030 0014 EN Service Manual Rev 0003 2008 06 3 29...
Page 76: ...Machine Systems MY500JetPrinter MYDATA 3 30 Rev 0003 2008 06 P 030 0014 EN Service Manual...
Page 111: ......