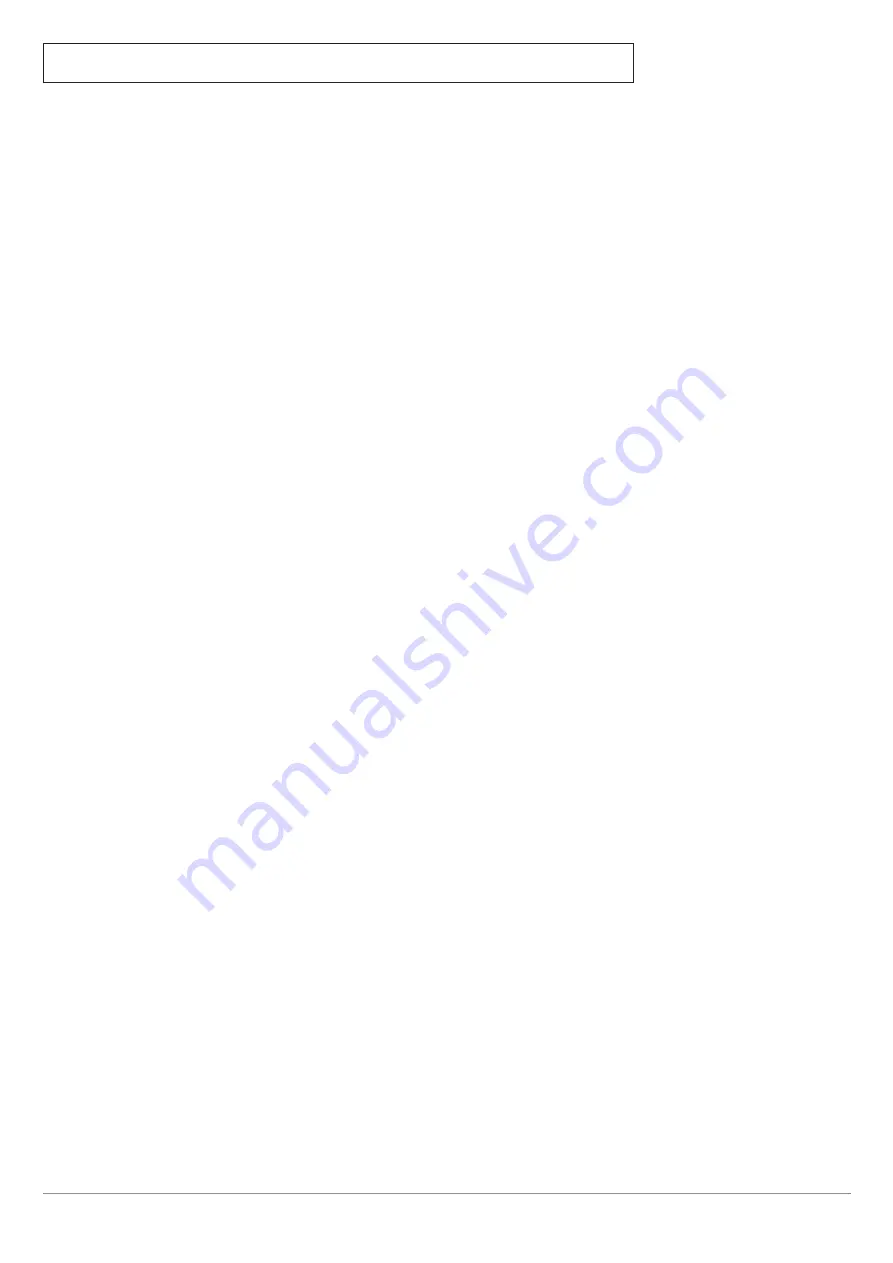
24
Subject to modifications
13. SAFETY WHILE LIFTING AND DUMPING *
This device is essential for working when people are present near the load (*optional).
Complies with standard EN 12525 + A2 2010; this equipment is compatible with the Shock Eliminator and the float detent
position.
13.1 Extract from the Front Loaders standard E A2 2010:
4.4.4 Protection against unintended lowering
If the front loader is also designed for lifting operations requiring the presence of someone near the load when the loader
is in raised position, the hydraulic circuit of the lifting arm cylinders must be fitted with a safety device in compliance with
Annex E, with the aim of preventing unintended lowering of the lifting arm, and which must remain active in the event of
rupture of the power supply of the control circuit.
If this safety device can be put in on/off or enabled/disabled positions for operations that do not require the presence of
someone near the load, then the following additional specifications apply:
– it must be possible to put the safety device into on/off or enabled/disabled position from the driver’s cab;
– it must be possible to put the safety device into on or enabled position from the ground and not be near the load;
– the control for putting the safety device into off or disabled position must be designed and located so that the operator
cannot actuate it unintentionally;
– the status (on/off or enabled/disabled) of the safety device must be clearly indicated and clearly visible from the driver’s
cab and from the loading area.
In compliance with 7.1.2, the correct operating method must be explained, including the warnings, in the instruction manual.
The loader must be fitted with a warning informing that for lifting operations requiring the presence of a
person near
the load, when the loader is in raised position, the safety device must be in the on position (enabled) (see 7.2).
Information for using front loaders that are not designed for lifting operations requiring the presence of an operator near
the load when the loader is in raised position must comply with 7.1.4 and 7.2.
"Appendix E
(normative)
Test method and acceptance criteria for means to avoid unintended lowering
E.1 Terms and definitions
E.1.1
discharge device
hydraulic valves used to simulate a rupture of the loader’s hydraulic piping.
E.1.2
test load
weight (50 ± 10)% of nominal lifting capacity specified by the manufacturer of the loader.
E.2 Test procedure
The test specified from E.2.1 to E.2.2 must be carried out according to each of the following conditions:
– position held after lowering the test load to a height of (1 ± 0.1) m (static test);
– position held after lifting the test load to a height of (1 ± 0.1) m (static test);
and at oil temperatures of the hydraulic system between 40°C and 50°C.
E.2.1 The discharge device between the lifting rams and the control valve must be open.
E.2.2 Complete lowering of the load must be measured at the implement’s pivot point.
E.3 Acceptance criterion
Complete lowering measured in E.2.2, during the first 10 seconds must not exceed:
– 100 mm, in the event of a stop or manual disabling of the safety device;
– 300 mm, in the case of a continuously actuated safety device.
After 5 min, lowering must not exceed an additional 100 mm.
Summary of Contents for MX A104
Page 2: ......
Page 4: ......
Page 6: ......
Page 33: ...31 Subject to modifications...
Page 35: ......