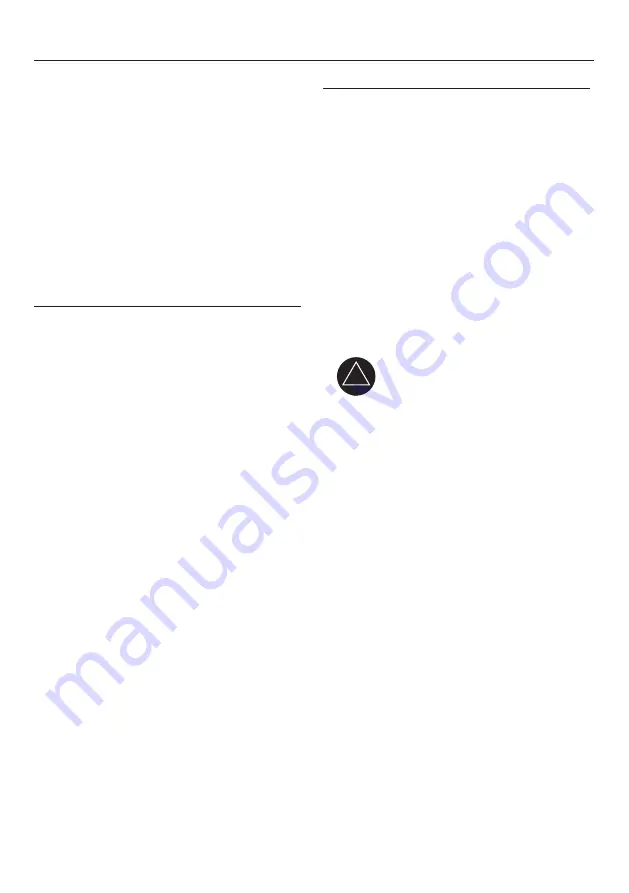
12. COMMISSIONING AND ANNUAL MAINTENANCE TESTING
Before commissioning the following checks and tests
need to have taken place:
• All the pipe work has been flushed through before
fitting the valve and there are no leaks.
• The supply pressures and temperatures are
checked and all are in the range specified in these
instructions.
• The isolation valves and strainers are fitted and
clean of any unwanted material and do not restrict
flow.
• The valve has been fitted to the pipework with all
connections correctly tightened.
COMMISIONING PROCEDURE
1. Ensure both isolation valves are fully open. Turn the
temperature control to cold and turn the flow on.
Check the temperature is at the required
minimum.
2. Rotate the temperature controller gradually until
it reaches the preset stop. Let it flow until the hot
water has reached the valve and the temperature
has stabilized.
Check the temperature is 38˚C +/-2˚C.
This is the factory preset. If the valve does not
operate properly check and confirm that the hot
and cold water supplies are fitted to the correct
inlets.
3. Override the temperature stop button by pressing
the button and rotate to maximum being careful to
avoid scalding.
Measure the temperature.
4. The valve should then be checked to confirm the
water isolation performs correctly. Run the valve at
the 38˚C stop position.
Check the water temperature.
5. Turn off the feed of cold water using the isolation
valve.
The water flow should fall to a very low flow,
(possibly only a drip) after a few seconds.
6. Collect the water after 5 seconds and 30 seconds.
M
easure the temperature – it should be below
46˚C +/- 2˚C .
7. Turn on the cold water again and
it should return
after a few seconds to stabilise to 38˚C +/- 2˚C
.
TEMPERATURE SETTING ADJUSTMENT
NOTE: Adjustment of the temperature settings is only
to be carried out by a competent TMV engineer as it is
a technically difficult operation in which the valve can
easily be broken.
1. Remove the handle on the temperature controller,
(noting carefully the assembly of the components).
2. Rotate the internal stops a few degrees in the
required direction.
3. Reassemble.
4. All the commissioning checks should be done
again to ensure it now meets the required
specification before using the shower.
Before use, ensure that you instruct
all users in the safe operation of the
shower as outlined in this document.
!
!
Summary of Contents for Atmos Energy
Page 15: ...NOTES...