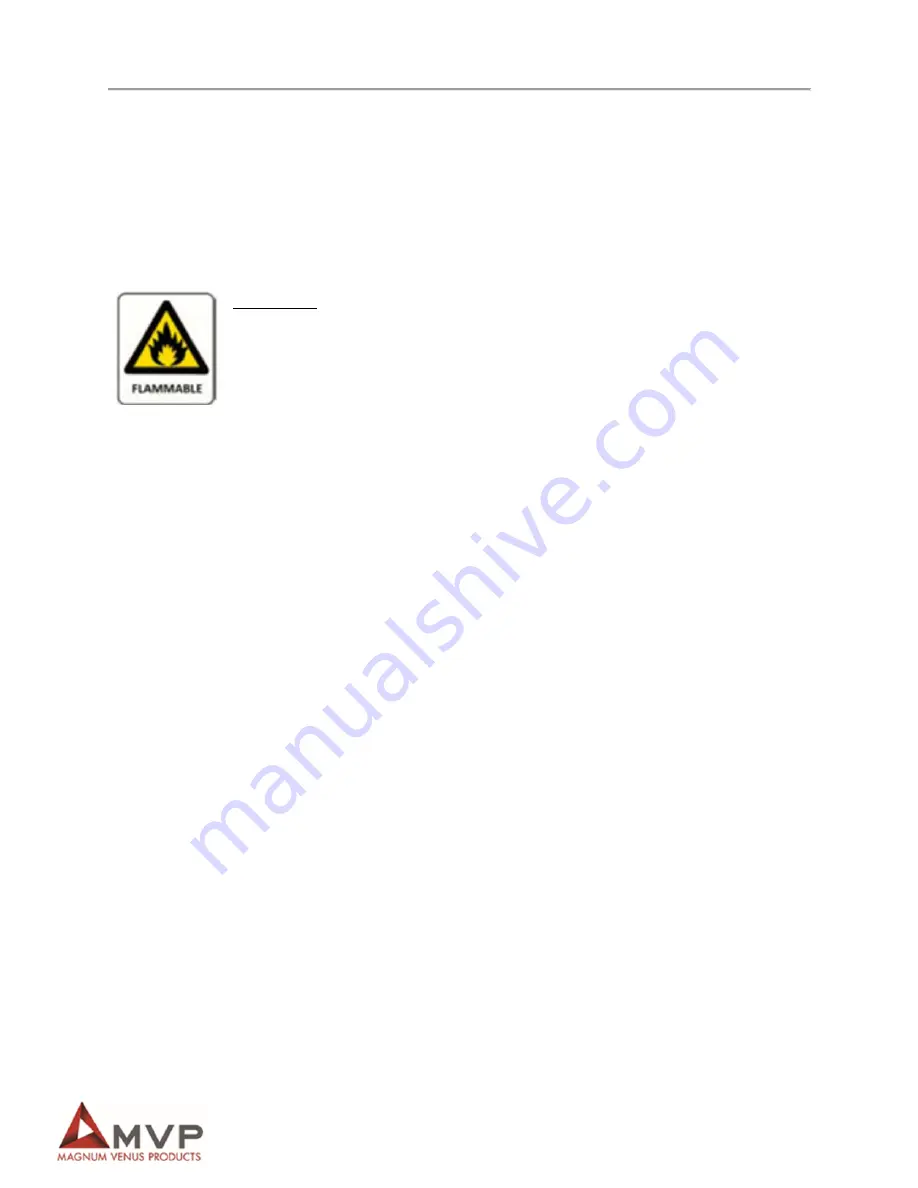
Mini Link Hydraulic System Operations Manual
Page | 12
Catalyst Diluents
Magnum Venus Products spray-up and gel-coat systems currently produced are designed so that
catalyst diluents are not required. Magnum Venus Products therefore recommends that diluents
not be used to avoid possible contamination which could lead to an explosion due to the handling
and mixing of MEKP and diluents. In addition, it eliminates any problems from the diluent being
contaminated through rust particles in drums, poor quality control on the part of the diluents
suppliers, or any other reason. If diluents are absolutely required, contact your catalyst supplier
and follow his instructions explicitly. Preferably the supplier should premix the catalyst to prevent
possible “on the job” contamination while mixing.
WARNING
If diluents are not used, remember that catalyst spillage and gun, hose,
and packing leaks are potentially more hazardous since each drop
contains a higher concentration of catalyst and will therefore react more
quickly with overspray and the leak.
Cured Laminate, Overspray and Laminate Sandings Accumulation
Remove all accumulations of overspray, Fiberglass Reinforced Plastic (FRP) sandings, etc. from
the building as they occur. If this waste is allowed to build up, spillage of catalyst is more likely to
start a fire; in addition, the fire would burn hotter and longer.
Floor coverings, if used, should be non-combustible.
Spilled or leaked catalyst may cause a fire if it comes in contact with an FRP product, over-
sprayed chop or resin, FRP sandings or any other material with MEKP.
To prevent spillage and leakage, you should:
1.
Maintain your Magnum Venus
Products System.
Check the gun several times daily for catalyst and
resin packing or valve leaks. REPAIR ALL LEAKS
IMMEDIATELY.
2.
Never leave the gun hanging over
or lying inside the mold.
A catalyst leak in this situation would certainly
damage the part, possibly the mold, and may cause
a fire.
3.
Inspect resin and catalyst hoses
daily for wear or stress at the entry
and exits of the boom sections and
at the hose and fittings.
Replace if wear or weakness is evident or
suspected.
4.
Arrange the hoses and fiberglass
roving guides so that the fiberglass
strands DO NOT rub against any of
the hoses at any point.
If allowed to rub, the hose will be cut through,
causing a hazardous leakage of material which
could increase the danger of fire. Also, the material
may spew onto personnel in the area.