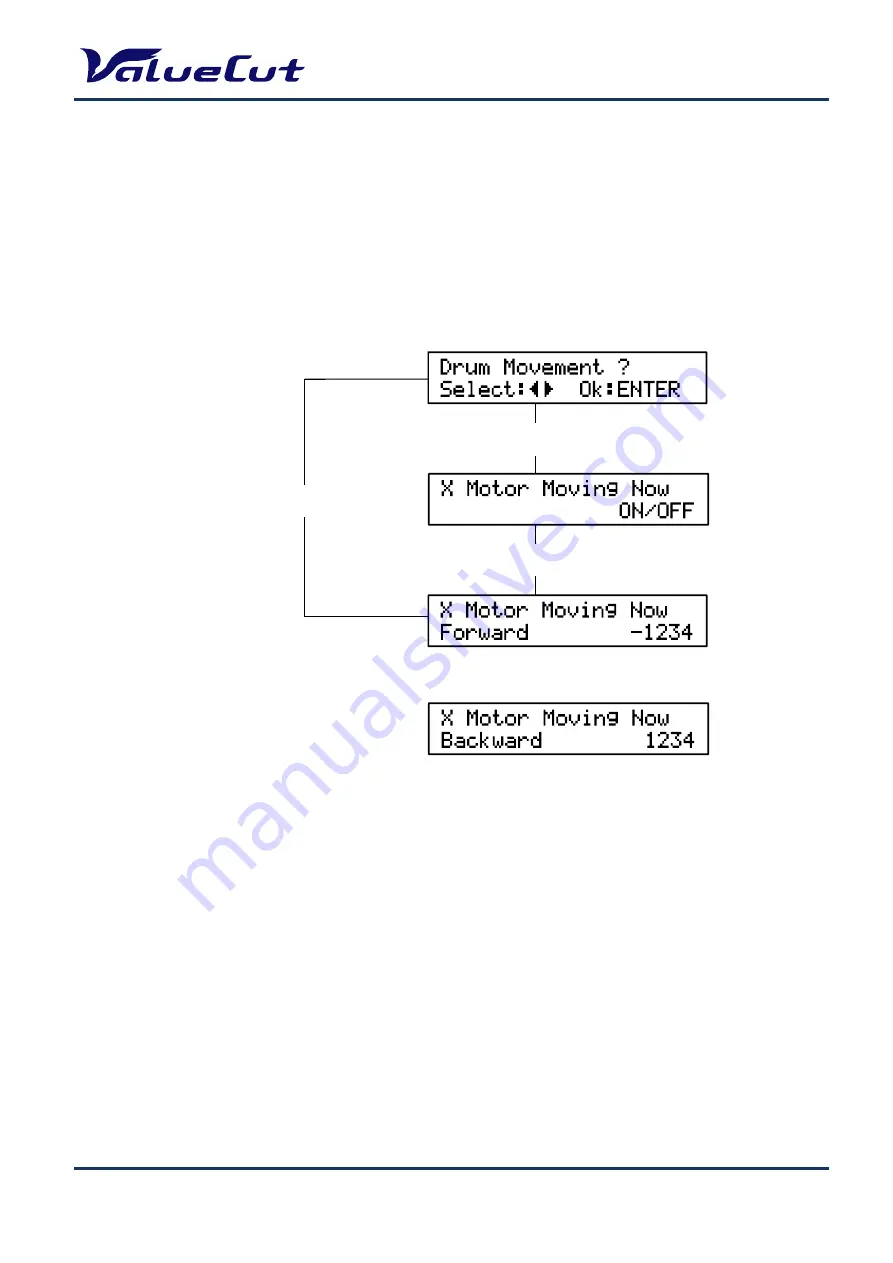
MAINTENANCE MANUAL
VC2E-MM-00
52
Diagnostic Test for Motor Movement
It diagnoses the X and Y motors and drivers. If you encounter a motor movement problem, try to change
the main board first. If the problem still remains after replacing the main board, try replacing the motor.
Drum Movement
ENTER
key
ON/OFF LINE
key
Forward
key
Backward
key
Summary of Contents for ValueCut VC2-1300
Page 1: ...No VC2E MM 00 Cutting Plotter VC2 600 VC2 1300 VC2 1800 MAINTENANCE MANUAL...
Page 9: ...MAINTENANCE MANUAL VC2E MM 00 9 B Electronic and Electrical Assembly Recommend Service Parts...
Page 10: ...MAINTENANCE MANUAL VC2E MM 00 10 C Left End Assembly Recommend Service Parts...
Page 11: ...MAINTENANCE MANUAL VC2E MM 00 11 D Right End Assembly Recommend Service Parts...
Page 12: ...MAINTENANCE MANUAL VC2E MM 00 12 E X Motor Bracket and Belt Assembly Recommend Service Parts...
Page 13: ...MAINTENANCE MANUAL VC2E MM 00 13 F Carriage Assembly Recommend Service Parts...
Page 14: ...MAINTENANCE MANUAL VC2E MM 00 14 G Pinch Roller Assembly Recommend Service Parts...
Page 15: ...MAINTENANCE MANUAL VC2E MM 00 15 H Main Beam Assembly Recommend Service Parts...
Page 16: ...MAINTENANCE MANUAL VC2E MM 00 16 I Drum Assembly Recommend Service Parts...
Page 17: ...MAINTENANCE MANUAL VC2E MM 00 17 J Stand and Basket Recommend Service Parts...
Page 18: ...MAINTENANCE MANUAL VC2E MM 00 18 System Diagram and Wiring Diagram...
Page 51: ...MAINTENANCE MANUAL VC2E MM 00 51 Holder Encoder Test ENTER key ON OFF LINE key 3 seconds later...