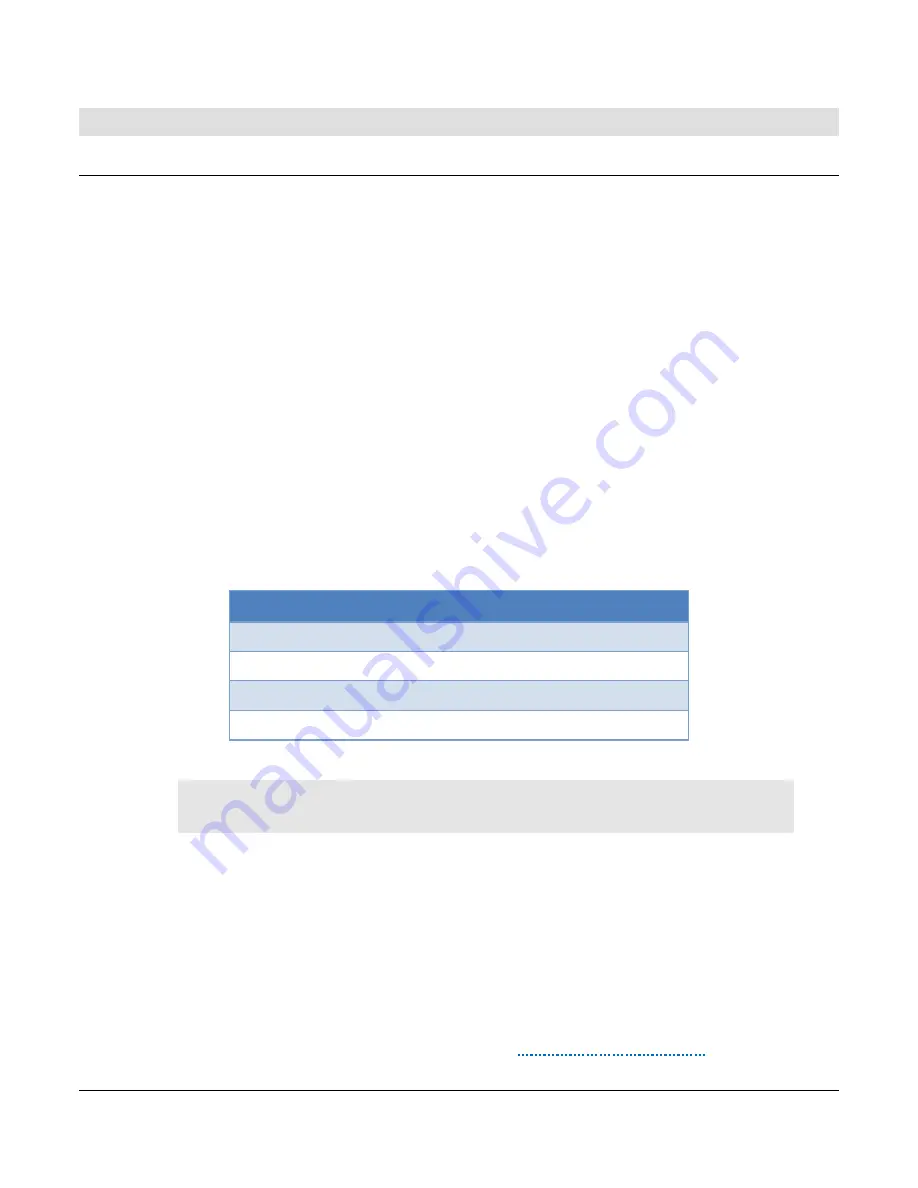
Section 80
00-02-0829
2018-02-26
-
16 -
4 Communication
4.1 Overview
The IX3212 PDM uses proprietary SAE J1939 CAN messages to configure control, and
communicate the I/O status. PowerView displays or a compatible CAN 2.0B CAN bus device
can be used to send CAN messages.
Each CAN message has an identifier in the first byte that determines the message context.
There are five unique identifiers associated with command and configuration and nine unique
identifiers associated with input status, feedback, diagnostics and data reported by the PDM.
4.1.1 Source Address
The Source Address (SA) is set using the first two digital inputs. A 1/open indicates the input
is open circuit or at high potential (i.e., connected to battery positive DC). A 0 indicates the
input is connected to a low potential (i.e., ground). Inputs contain a pull-up resistor that
interprets the input as High if left unconnected. Table 1 lists the available source addresses
and allows for up to four PDM modules on a single CAN bus. The PDM defaults to SA 30
(17h) if the inputs are not connected. The PDM does not support SA arbitration according to
J1939.
Digital Input 1 Digital Input 2
SA
1/open
1/open
30 (1Eh)
default
0
1/open
31 (1Fh)
1/open
0
32 (20h)
0
0
33 (21h)
Table 1 – Source Address Selection
IMPORTANT: When multiple PDMs are connected to the same CAN
bus, each PDM must have a unique SA.
The PDM sends messages to and expects to receive messages from SA 17 (11h) regardless
of the actual SA claimed by the configuring and controlling device(s). If a system has a cruise
control or steer axle controller, the SA may conflict with the PDM.
4.1.2 Loss of Communication
The PDM expects to receive commands from a controlling device every second. If a CAN
command message is not received, the PDM assumes that the CAN bus is faulted and goes
into a Loss of Communication mode. Each output can be individually configured to respond in
prescribed way and is further defined in the section on