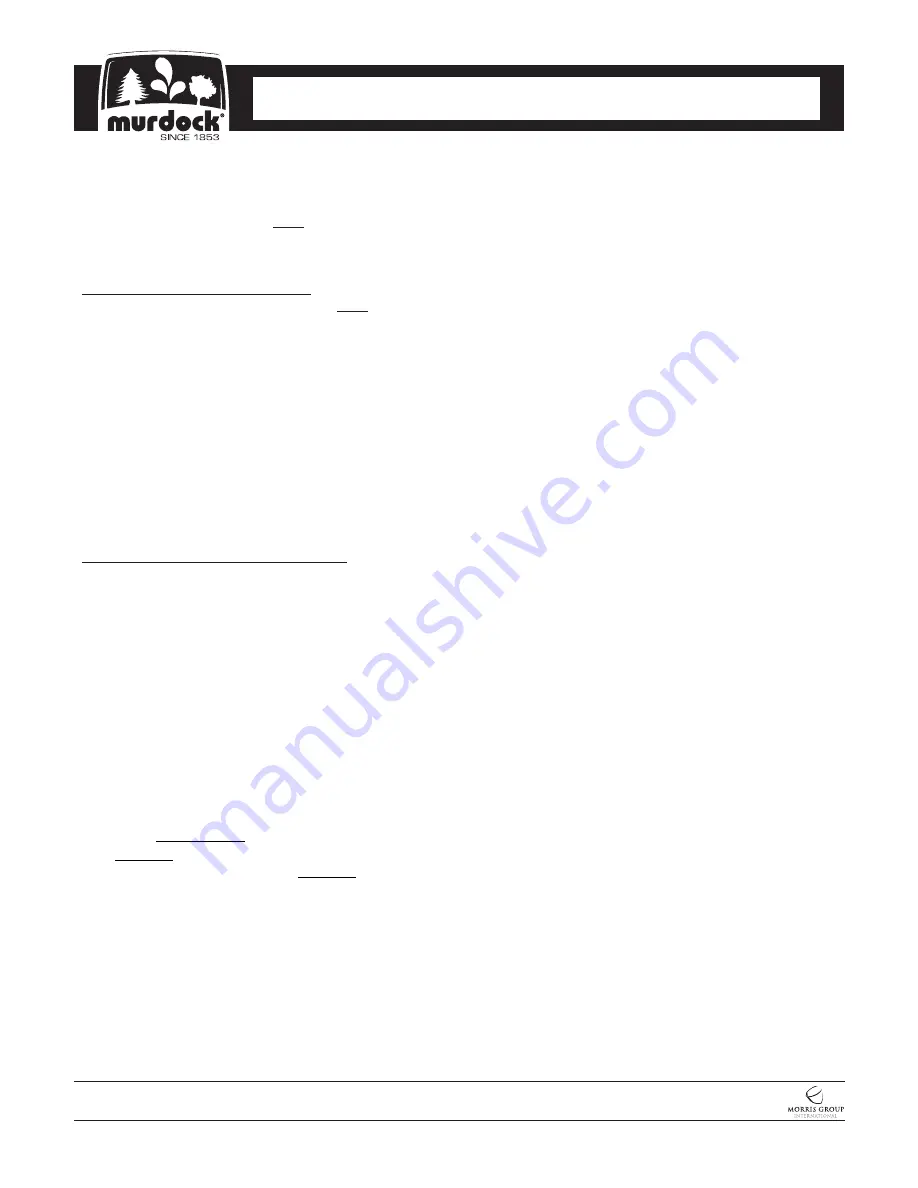
a. Verify 120VAC input & 9VDC output transformer output 9VDC.
7. WATER DRIPS OR WILL NOT SHUT OFF:
b. Replace valve cartridge.
a. Repair bad connection from sensor to solenoid.
1. To Remove water spots or rust spots, stainless steel cleaner/polish on a cloth is
recommended.
8. IF LIGHT WITHIN SENSOR DOES NOT FLASH ONCE WHEN USER IS WITHIN RANGE:
3. Apply stainless steel cleaner/ polish to the synthetic abrasive pads and carefully rub the
panel with the grain.
For Stainless steel units:
b. Replace defective transformer.
a. Open fixture. Loosen nuts holding valve bracket assembly to bottom of fixture but, do not remove. Move
complete valve bracket assembly further back from the front push pad and tighten to lock in place.
c. Transformer polarity crossed. Replace transformer, sensor may be damaged and also need replacement.
d. Sensor in “Security Mode” after 30 seconds of consistent detection. Remove source of detection and wait
30 seconds before checking.
CLEANING & MAINTENANCE GUIDE:
For Powder coated units:
Units should be cleaned using a mild soap solution with a sponge or cotton cloth.
Wipe down surfaces then rinse with clean water.
evaporator coil. This indicates a refrigeration problem or thermostat failure; in which, case the water
chiller needs to be checked by a qualified technician.
I. No power to transformer connections, loose or wires cut.
b. There is debris or scale in the solenoid assembly. Remove solenoid, pull out plunger and spring. Clean
with scale remover solution.
SENSOR TROUBLE SHOOTING:
c. There is debris or scale in the center or two holes in convolution of the water diaphragm. Remove and
clean.
1.
Motors have lifetime lubrication and do not require scheduled maintenance.
2.
Excess dirt or poor ventilation will cause the compressor overload protector to turn the compressor off and it
will cycle on and off with no cold water coming out of bubbler. Periodically clean with vacuum cleaner, air
hose or brush the condenser fins and cabinet ventilation louvers. In environments where dirt and dust is
more prevalent, clean more frequently.
3.
Periodically remove fountain top and clean out in-line strainer.
4.
Periodically remove access panel of cooler and clean out inline “Y’’ strainer
9. IF LIGHT WITHIN SENSOR LENS FLASHES ONCE WHEN THE USER IS WITHIN RANGE:
e. Sensor is picking up a highly reflective surface. Eliminate cause of reflection and wait 30 seconds before
checking.
2. If there are stubborn spots or if you wish to treat a scratch, using synthetic abrasive general
purpose pads, such as Scotch-Brite™, are recommended.
4. DO NOT use harsh chemicals, abrasive or petroleum based cleaners. Use of these will
void the Murdock warranty. DO NOT use abrasives on powder coated units.
5. Stainless steel should be kept clean at all times. If a coating of stainless steel cleaner/
polish is maintained, stainless steel surfaces will retain their new, clean, polished
appearance indefinitely.
I N S TA L L AT I O N / M A I N T E N A N C E I N S T R U C T I O N S
CONTEMPORARY WATER COOLERS
I N S TA L L AT I O N / M A I N T E N A N C E I N S T R U C T I O N S
DRINKING FOUNTAINS
A152.8-BF4
Page 19 of 23
Revised:
07/18/18
7020-949-001
MURDOCK MFG. •
15125 Proctor Avenue • City of Industry, CA 91746 USA
Phone 800-453-7465 or 626-333-2543 • Fax 626-855-4860 • www.murdockmfg.com
Member of