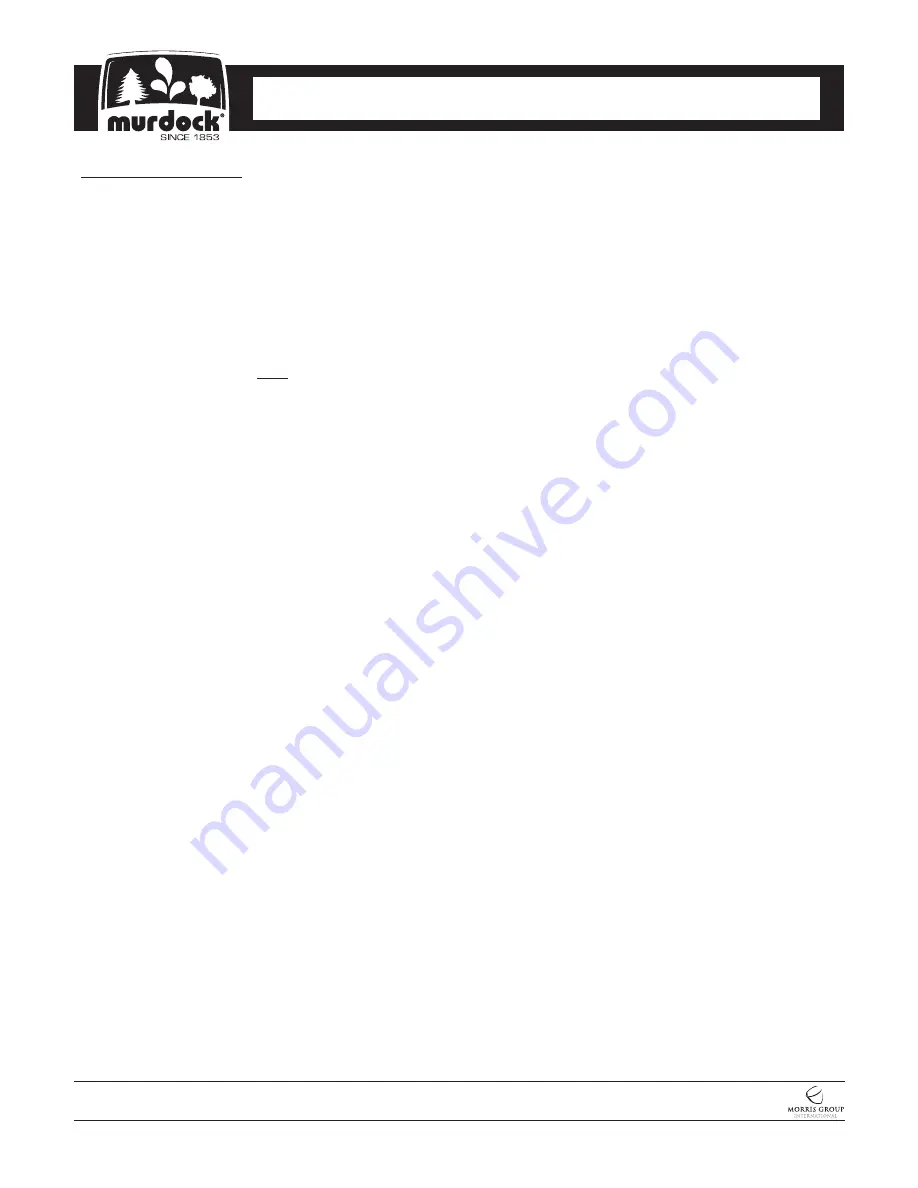
a. Cartridge – The water flow can be adjusted using a slotted narrow blade screwdriver and turning
clockwise to increase flow and counterclockwise to decrease flow.
TROUBLE SHOOTING:
IMPORTANT: BEFORE MAKING ANY OF THE REPAIRS LISTED, MAKE SURE THE
WATER CHILLER IS DISCONNECTED FROM THE ELECTRICAL SUPPLY AND THE
WATER SUPPLY VALVE IS SHUT OFF.
1. ADJUSTMENTS:
b. Cold Water Thermostat – The water temperature can be adjusted using a slotted screwdriver and turning
clockwise to make colder and counterclockwise to make warmer.
2. COMPRESSOR DOES NOT RUN:
a. Check the electrical supply for power and correct voltage. The incoming voltage must be within 10% of
the rated voltage on the serial nameplate.
c. Bubbler Stream - Bubbler can be rotated slightly to direct the stream backwards or forwards. Adjust the
stream to minimize splashing. Splashing may occur from bubbler stream if the unit is not level. Shim lower
mounting point, if necessary, to level chiller.
b. If the cold thermostat capillary bulb loses its charge or becomes kinked, it will fail in the open position
causing a disruption of power to the compressor. Disconnect electrical supply to the water chiller and
using an ohm meter, check for continuity across the two electrical terminals on the thermostat. Install a
new thermostat if there is no continuity.
c. Check for loose wires within the compressor box. The incoming power leads must be connected to the
overload and relay.
d. If all components check positive for continuity, then test the wiring harness plug for continuity to see if
there is a broken wire within the wiring harness insulation.
3. COMPRESSOR RUNS - WATER IS WARM:
b. Make sure the condenser fan motor is operative. The fan blade must turn freely to help remove the heat
of compression.
c. An incorrect refrigerant charge, restriction or defective compressor (not pumping) will also cause the
compressor to run without producing cold water. All these signs indicate a problem within the refrigeration
system and the water chiller must be checked by an authorized service company.
a. The most common cause for a water chiller to run without producing cold water is a loss of refrigerant.
The water chiller must be taken to a certified refrigerant technician for repairs.
a. Check to make sure the fan blade is rotating freely.
c. A restriction or moisture in the system will also cause intermittent cycling. A certified refrigeration
mechanic should be contacted in this situation.
5. NOISY OPERATION:
a. Ensure water supply service stop valve is fully open.
b. Verify minimum 20 psig supply line flow pressure.
f. Check flow adjustment. See start up note #3.
b. Check the incoming voltage to make sure it is within 10% of the serial nameplate rating.
c. Check for twists or kinks in outlet tubing.
d. Check the water inlet “Y” strainer. Sediment from the main supply can get trapped in the screen along
with installation materials such as pipe dope and flux. The screen should be cleaned and checked on a
regular basis and replace if needed.
g. Flow control in solenoid valve outlet elbow clogged remove & clean.
b. Check the compressor mounting to make sure the pins and clips are not rattling. If the compressor
appears to be noisy internally, it must be replaced.
a. A dirty condenser or a blocked fan will cause a high head pressure and frequent cycling of the overload
protector.
h. The water chiller may also develop a freezing condition in which the water will become frozen inside the
6. RESTRICTED OR NO WATER FLOW:
e. The cartridge valve located in the water control assembly or bubbler can also become clogged with
foreign material. The cartridge valve can only be replaced and not repaired.
4. COMPRESSOR CYCLING ON OVERLOAD PROTECTOR:
d. Change the overload or relay if defective.
I N S TA L L AT I O N / M A I N T E N A N C E I N S T R U C T I O N S
CONTEMPORARY WATER COOLERS
I N S TA L L AT I O N / M A I N T E N A N C E I N S T R U C T I O N S
DRINKING FOUNTAINS
A152.8-BF4
Page 18 of 23
Revised:
07/18/18
7020-949-001
MURDOCK MFG. •
15125 Proctor Avenue • City of Industry, CA 91746 USA
Phone 800-453-7465 or 626-333-2543 • Fax 626-855-4860 • www.murdockmfg.com
Member of