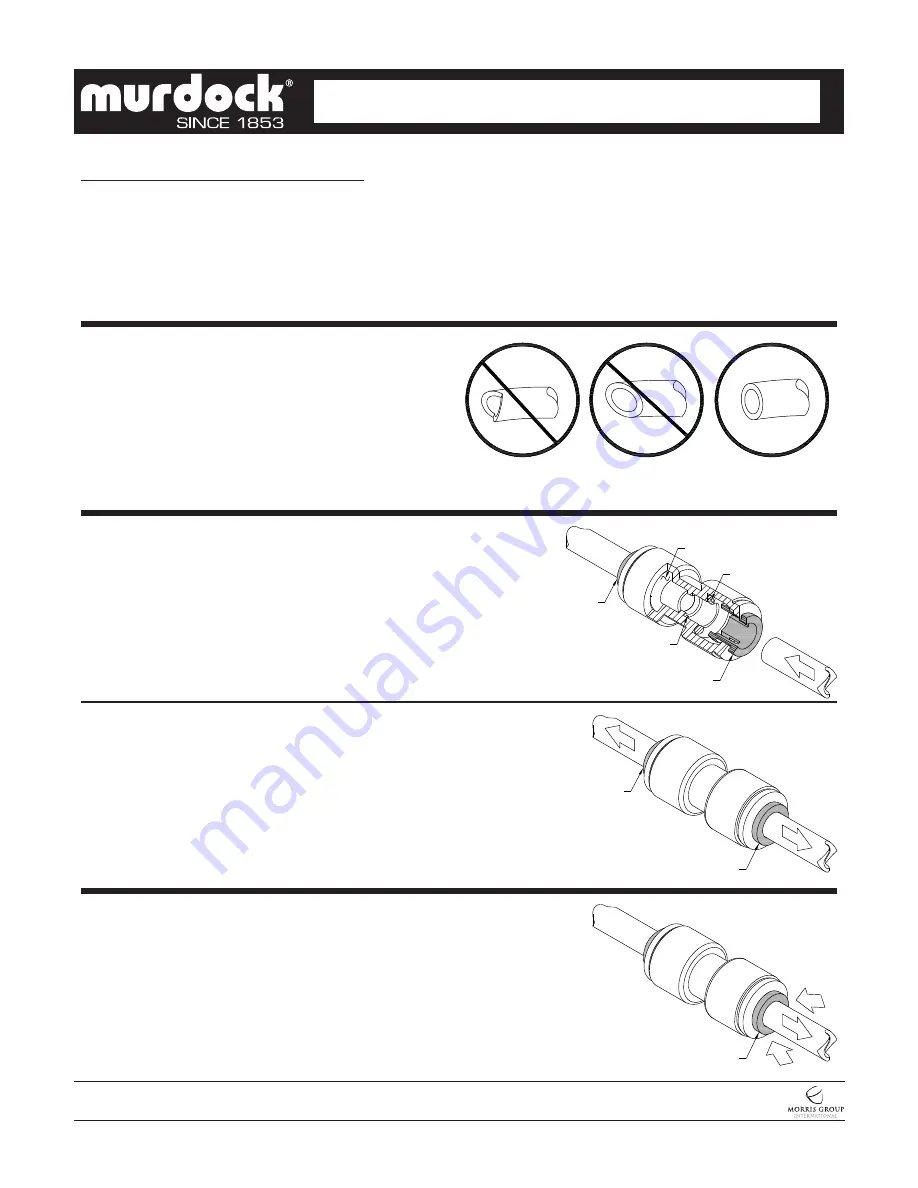
PUSH-IN FITTING INSTALLATION
NOTE: FITTINGS AND TUBE SHOULD BE KEPT
CLEAN, BAGGED AND UNDAMAGED PRIOR TO
INSTALLATION.
2. Pull on the fitted tubing to ensure it is secure. Tube
should not come free from the fitting. Water test the
connection assembly prior to leaving the site to ensure
there are no leaks.
DISCONNECTING THE TUBE:
To disconnect the tube from the fitting ensure that the
water line is depressurized. Push collet square towards
the push-in fitting body and hold. While holding the collet
in, pull on the PE tubing to remove from the push-in fitting.
TO CUT TUBE:
Cut to fit length of 1/4” PE tubing and remove any burrs
or sharp edges. Ensure that the outside diameter is free
from score marks. Tube ends should be square.
INSERTING THE TUBE:
1. Firmly and fully insert the tubing end into the push-in
fitting up to the tube stop located approximately ½”
deep.
COLLET
COLLET
O-RING
O-RING
TUBE STOP
COLLET
COLLET
COLLET
A151.8-VR
Page 10 of 11
Date:
11/10/2020
7021-024-001
MURDOCK MFG. •
15125 Proctor Avenue • City of Industry, CA 91746 USA
Phone 800-453-7465 or 626-333-2543 • Fax 626-855-4860 • www.murdockmfg.com
Member of
CONTEMPORARY WATER COOLERS
I N S TA L L AT I O N / M A I N T E N A N C E I N S T R U C T I O N S
DRINKING FOUNTAINS