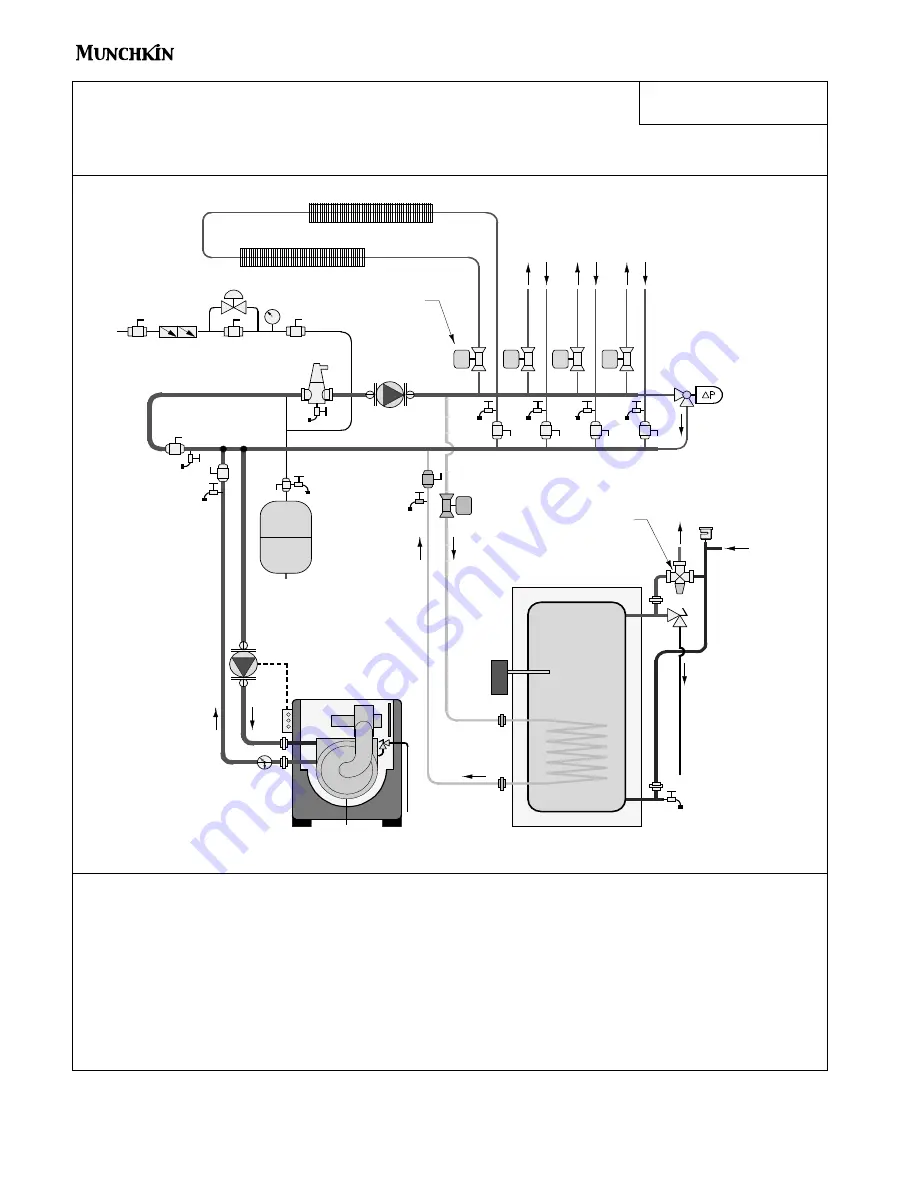
21
GAS-FIRED BOILER
Boiler Manual
Standard Munchkin boiler
Preferred piping (zoning with valves)
Space heating mode
Munchkin boiler
P1
Super Stor
indirect DHW tank
T/P
Drawing 2A
make-up water
zone valves
NOTES:
1.
This drawing is meant to show system piping concept only.
Installer is responsible for all equipment & detailing required by local codes.
2.
Adjust differential pressure bypass valve to eliminate any flow velocity noise when zone with highest pressure
drop operates by itself.
3.
The minimum pipe size for connecting a Super Stor water heater is 1 inch.
4.
The minimum pipe size for connecting a Munchkin boiler is 1.25 inches and 2 inches for the 399M.
5.
All pumps are shown with isolation flanges. The alternative is standard flanges with full port ball valves.
6.
The anti-scald mixing valve is recommended if the DHW temperature is set above the factory setting of 119˚F.
7.
Install a minimum of 12 diameters of straight pipe upstream of all circulators.
8.
A purging valve may be used in lieu of the ball valve / hose bib combination shown.
9.
A minimum of 6 pipe diameters of straight pipe shall be installed upstream and downstream
of all closely spaced tees.
V1
differential
pressure
bypass
valve
anti-scald
mixing valve
purging
valves
closely
spaced
tees
P2
cold
water
OFF
NOTE: For Vision piping applications, refer to the Vision Installation Piping Diagrams.
Summary of Contents for Gas-Fired Hot Water Boiler
Page 11: ...10 GAS FIRED BOILER Boiler Manual DIMENSIONS 80M 140M 199M Figure 2 2 Figure 2 3...
Page 52: ...51 GAS FIRED BOILER Boiler Manual PART 9 FIELD WIRING CONTINUED Fig 9 5...
Page 77: ...76 MAINTENANCE NOTES...
Page 78: ...77 MAINTENANCE NOTES...
Page 79: ...78 MAINTENANCE NOTES...
Page 80: ...2007 Heat Transfer Products Inc www HTproducts com LP 185 REV 12 10 07...