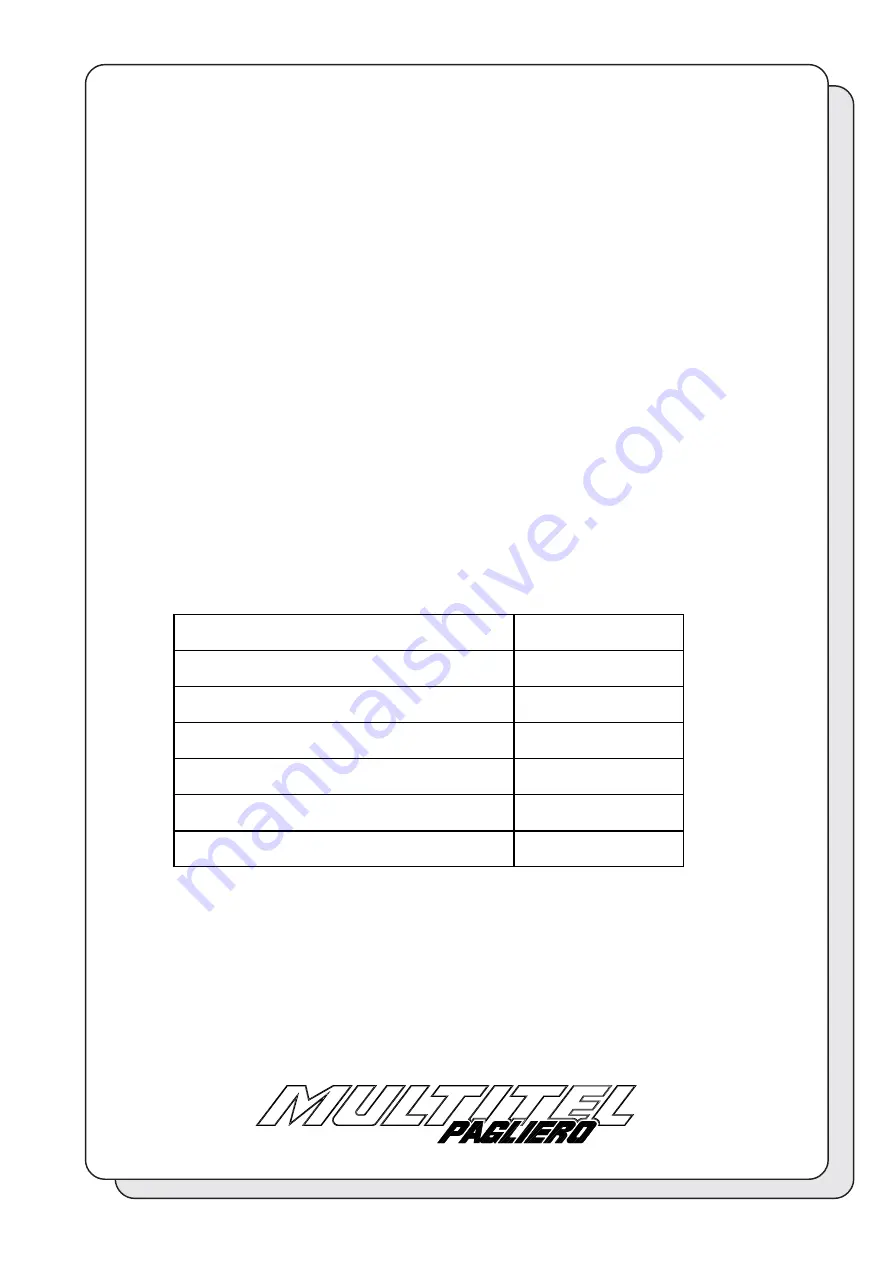
21
ROTATION GEAR BOX
Check the level of the oil in the reduction gear every six months.
It was originally filled with
AGIP ROTRA 80 W/90
oil.
The oil should be replaced with the reduction gear warm, taking the opportunity also to wash the
guards.
ROTATION SLEW RING
Regular lubrication using quality lubricants is essential for proper operation.
It is recommended that lubrication should be carried out in such a way that the grease comes out of
the slits in the rings so as to form a collar around the whole circumference. Make sure that the
grease is evenly distributed, turning the bearing as it is being greased. Choose the lubrication
frequency depending on the operating conditions so that the average interval corresponds to about
100 hours of use.
LIST OF RECOMMENDED GREASES AND TEMPERATURES FOR USING THEM:
GREASE
TEMPERATURES
IP Alvania 32
-30° +130°
IP Fluid 12
-20° +60°
MOBIL Mobilux 2
-35° +130°
MOBIL Mobiltac 81
-30° +120°
ESSO Beacon 2
-30° +130°
ESSO Surret Fluid 30
-20° +60°