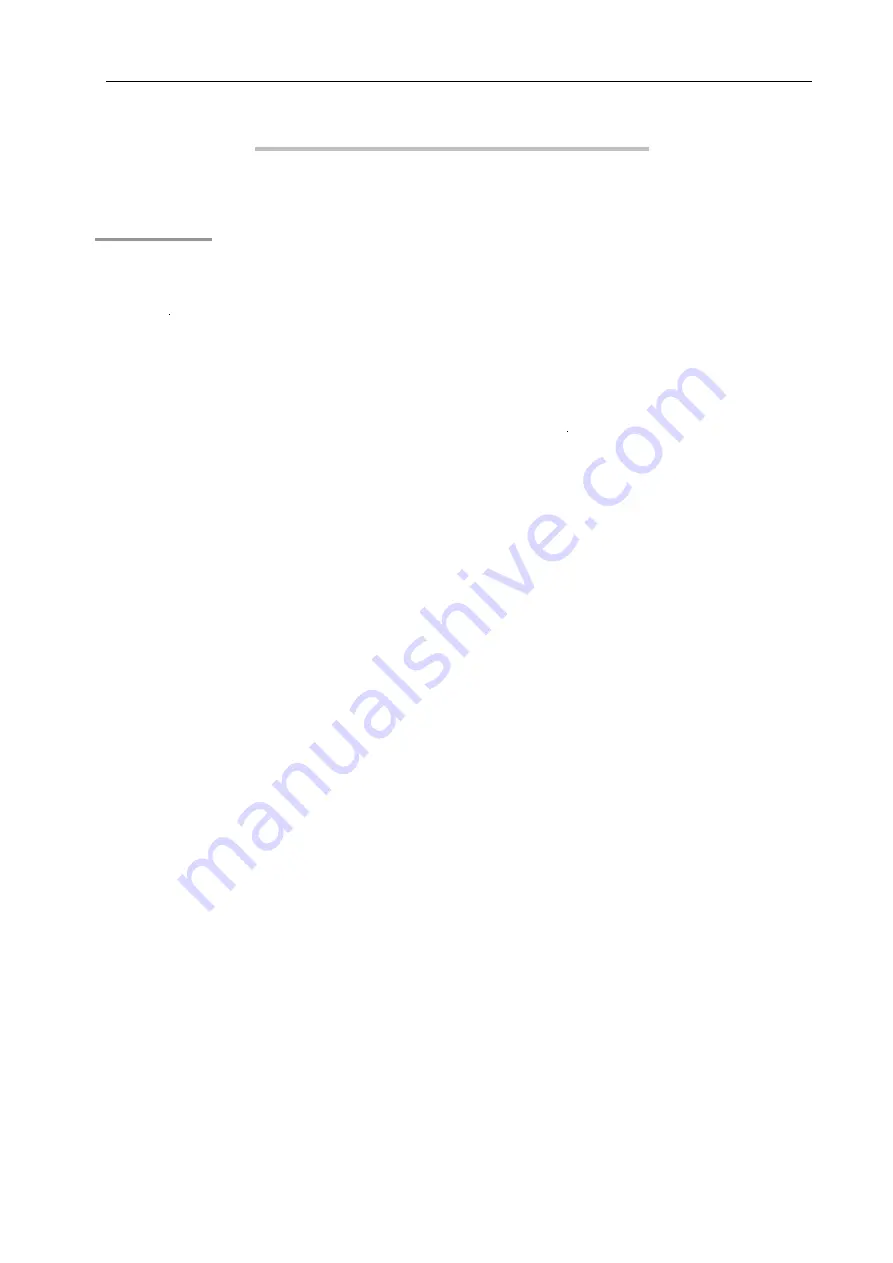
LAUNCH
TLT830WA INSTALLATION MANUAL
1
INSTALLATION MANUAL
Contents
1 Precautions
…………………………………………………2
2 Structure and Working Principle
……………………….3
2.1 Structure …………………………………………………..3
2.2 Electrical Diagram………………………………………..4
2.3 Hydraulic Diagram………………………………………..5
2.4 Hydraulic Components in the Control Desk……………5
2.5 Pneumatic Diagram ……………………………………..6
3 Tools for Installation and Adjustment
…………………7
4 Unpacking
………………………………………………….7
5 Installation of the Lift
…………………………………….7
5.1 Overall Position……………………………………………7
5.2 Installation on Floor Surface……………………………..8
5.3 Installation on Ditch……………………………………....9
5.4 Control Desk Installation………………………………...10
5.5 Power Connection………………………………………..10
5.6 Hydraulic Hoses Connection…………………………….11
5.7 Anchoring………………………………………………….12
5.8 Air Hose connection……………………………………...13
6 Lift Adjustment
……………………………………………13
6.1 Preparation………………………………………………..13
6.2 Adjustment Procedure…………………………………...13
7 Parts List
…………………………………………………...14