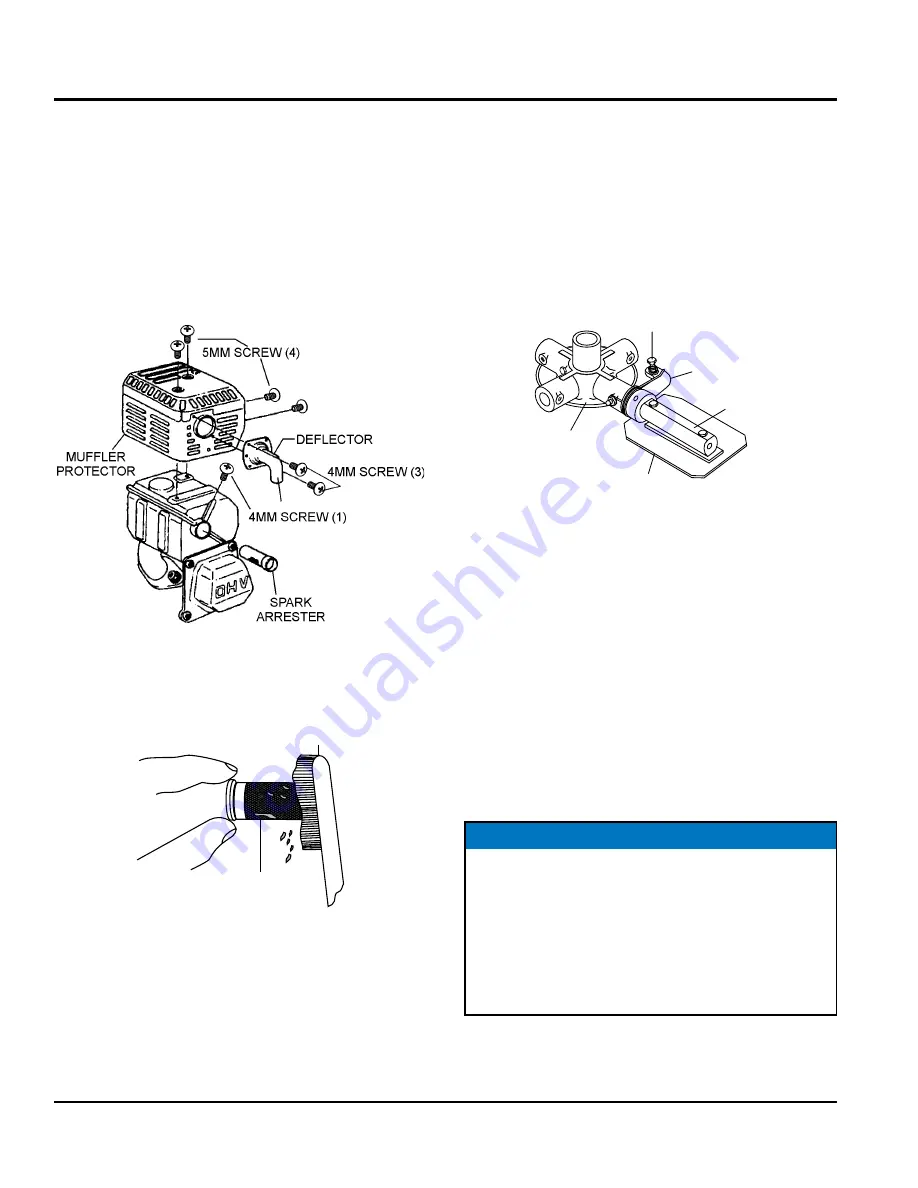
PAGE 32 — JS36 SERIES WALK-BEHIND TROWEL • OPERATION AND PARTS MANUAL — REV. #5 (06/02/16)
MAINTENANCE
SPARK ARRESTER CLEANING
Clean the spark arrester every 6 months or 100 hours.
1. Remove the 4 mm screw (3) from the exhaust deflector,
then remove the deflector. See Figure 46
2. Remove the 5 mm screw (4) from the muffler protector,
then remove the muffler protector.
3. Remove the 4 mm screw from the spark arrestor, then
remove the spark arrester.
Figure 46. Spark Arrester Removal
4. Carefully remove carbon deposits from the spark
arrester screen (Figure 47) with a wire brush.
Figure 47. Cleaning The Spark Arrester
5. If the spark arrester is damaged and has breaks or
holes, replace with a new one.
6. Reinstall the spark arrester and muffler protector in
reverse order of disassembly.
SPARK
ARRESTER
SCREEN
WIRE
BRUSH
BLADE PITCH ADJUSTMENT PROCEDURE
The maintenance adjustment of blade pitch is an adjustment
that is made by a bolt (Figure 48) on the arm of the trowel
arm lever. This bolt is the contact point of the trowel arm
lever to the lower wear plate on the thrust collar. The goal
of the adjustment is to promote consistent blade pitch and
finishing quality. Adjustments are made by tightening or
loosening the blade pitch adjustment bolt.
Figure 48. Blade Pitch Adjustment Bolt
Watch for the following indications when determining if
blade pitch adjustments are necessary:
• Is the machine wearing out blades unevenly, (i.e. one
blade is completely worn out while the others look
new)?
• Does the machine have a perceptible rolling or
bouncing motion when in use?
• Look at the machine while it is running, do the guard
rings “rock up and down” relative to the ground?
If it is determined that blade pitch adjustments are required
do the following:
1. Place the trowel on a flat, level area free of dirt and
debris.
SPIDER
PLATE
BLADE PITCH
ADJUSTMENT
BOLT
TROWEL
ARM
TROWEL LEVER
FINGER
TROWEL
BLADE
NOTICE
Before any blade pitch adjustments can be made it
is essential to have a clean level area free of dirt and
debris to test the trowel. Any unlevel spots in the floor
or debris under the trowel blades will give an incorrect
perception of adjustment. Ideally, a 5 x 5 ft. (1.5 x 1.5
meter), three-quarter inch (19 mm) thick
FLAT
steel
plate should be used for testing.