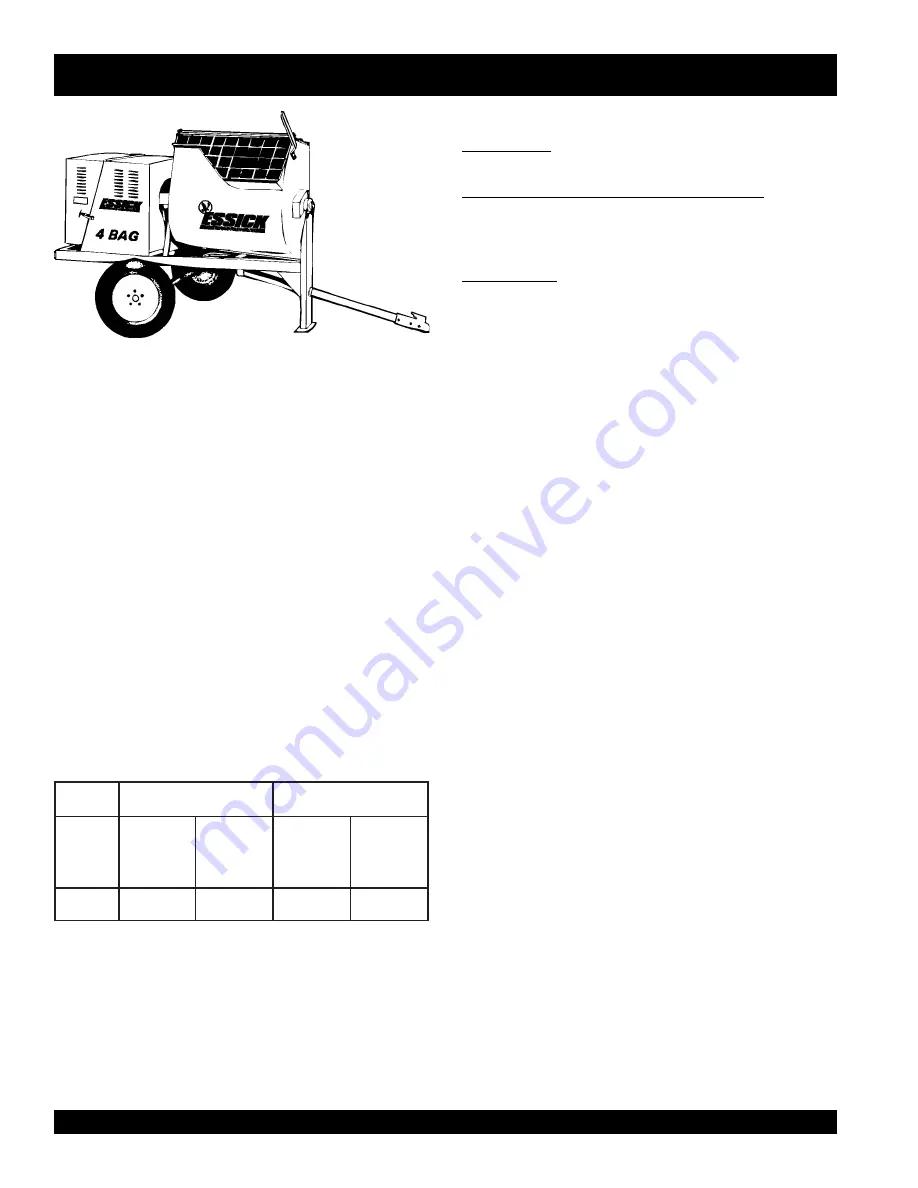
PAGE 8 — ESSICK EM-900S & 900P — PARTS & OPERATION MANUAL — REV. #7 (06/26/01)
EM-900S & 900P — OPERATIONS
GENERAL
The Essick EM-700 and EM-900 Series plaster and mortar
mixers are quality mixers that have a batch capacity of 2.5 and
3.5 bags respectively. With proper care, they will give continuous
service year-after-year.
GASOLINE ENGINE CARE
For care and operation of the gasoline engine, refer to the
engine manufacturer’s operating instructions furnished with the
engine. We recommend draining and refilling the engine
crankcase at least every thirty hours of operation. Check the
engine oil level daily.
ELECTRIC MOTOR CARE
For lubrication care and operation of the electric motor, refer to
your electric motor instruction booklet furnished with the motor.
Protect the electric motor from dust as much as possible and
keep ventilating openings clean. Do not spray water on the
electric motor.
Refer to the following chart. For recommend plug sizes.
CONTROLS
KILL SWITCH: (Gasoline Engine Only) Located on the side of
the engine cover.
ENGINE THROTTLE AND CHOKE CONTROLS: Please refer
to the engine owners manual for specific instructions. The electric
motor switch ( electric motor only) located on the motor — is
used to start and stop the mixer.
DUMP LATCH: To dump the tub, grasp the dump handle and
lift the dump latch, then rotate the tub to discharge the mix. After,
discharge, return the tub to the vertical mixing position.
CLUTCH
The paddle shaft and mixing blades are engaged and
disengaged by tightening and loosening the drive belts with a
spring loaded idler pulley. To engage the clutch, rotate the
lever locates at the front of the mixer counterclockwise. The
spring maintains the correct belt tension. To disengage the
clutch, rotate the lever clockwise against the lever stop. The
engine base is slotted to adjust for belt wear and to bring the
idler pulley into operating range.
CAUTION: Stop the engine before allowing anybody to put
their hands in the mixing drum.
WHEEL BEARINGS
After every 3 months of operation, remove the hub dust cap
and inspect the wheel bearings. Once a year, or when required,
disassemble the wheel hubs remove the old grease and
repack the bearings forcing grease between rollers, cone and
cage with a good grade of high speed wheel bearing grease
(never use grease heavier than 265 A.S.T.M. penetration “No.
2.”) Fill the wheel hub with grease to the inside diameter of the
outer races and also fill the hub grease cap. Reassemble the
hub and mount the wheel. Then tighten the adjusting nut, at
the same time turn the wheel in both directions, until there is a
slight bind to be sure all the bearing surfaces are in contact.
Then back-off the adjusting nut 1/6 to 1/4 turn or to the nearest
locking hole or sufficiently to allow the wheel to rotate freely
within limits of .001" to .010" end play. Lock the nut at this
position. Install the cotter pin and dust cap, and tighten all
hardware.
R
O
T
O
M
Ø
1
T
L
O
V
5
1
1
0
0
7
M
E
Ø
1
T
L
O
V
0
3
2
0
0
9
M
E
E
S
R
O
H
R
E
W
O
P
P
A
C
L
I
A
T
G
I
P
/
A
M
E
N
K
C
I
S
S
E
Y
D
O
B
N
N
O
C
/
A
M
E
N
K
C
I
S
S
E
P
A
C
L
I
A
T
G
I
P
/
A
M
E
N
K
C
I
S
S
E
Y
D
O
B
N
N
O
C
/
A
M
E
N
K
C
I
S
S
E
P
H
3
&
½
1
5
4
5
0
4
9
/
P
0
3
-
5
L
6
4
5
0
4
9
/
R
0
3
-
5
L
0
5
5
0
4
9
/
P
5
1
-
6
L
1
5
5
0
4
9
/
R
5
1
-
6
L