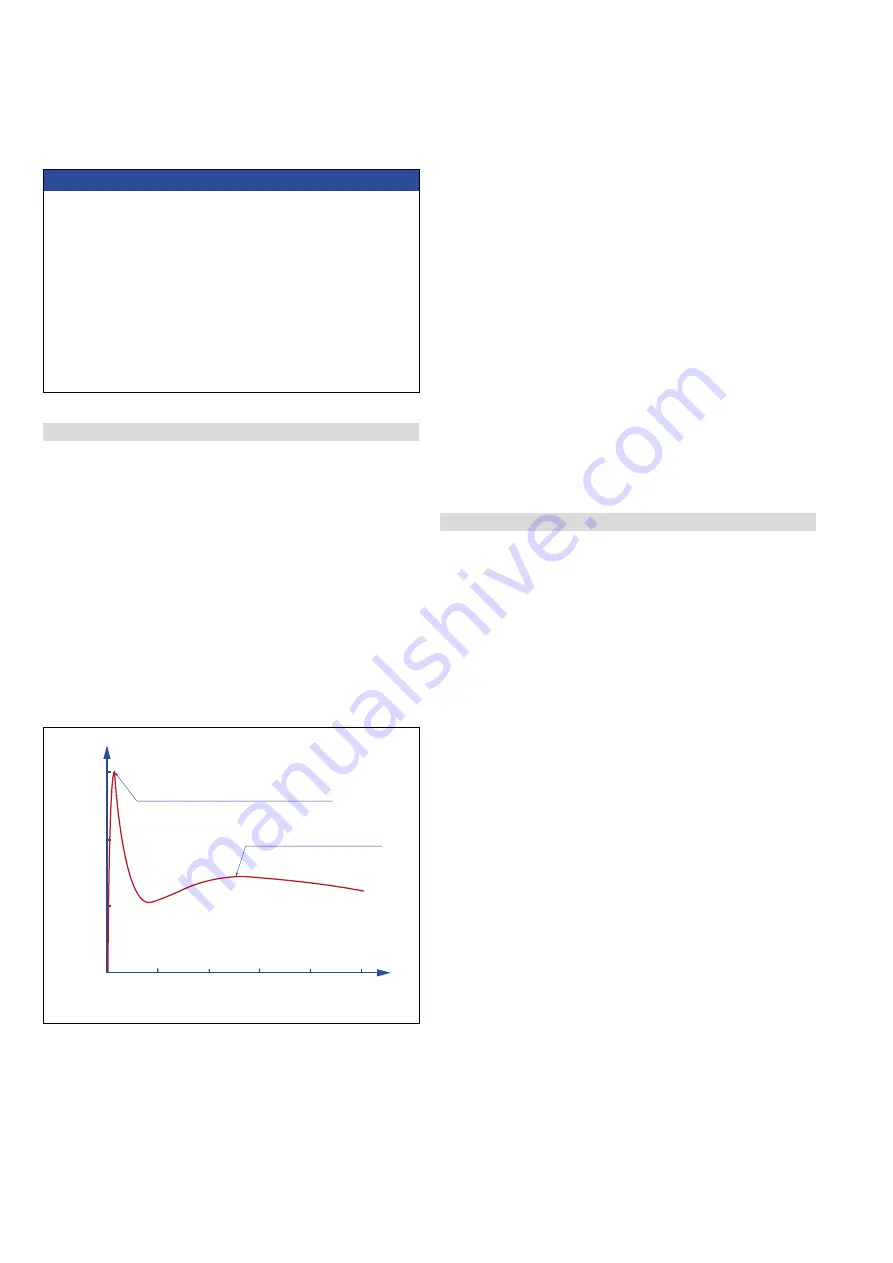
C-Series Off-Highway
Installation Manual
I 16 I
NOTICE
• Cut or disconnect all sensor connections during welding.
• Never fasten the grounding point at the piston rod or at the
cylinder pipe.
• Never perform welding work on a part of the cylinder, if a sensor
has been installed.
• Never perform welding work near a cylinder, if a sensor has been
installed.
• Due to isolating bearings, plastic slide bearings or grease in the
contact points, electric potentials/voltages can build up at every
bearing point of machines. Accordingly, similar effects as on
hydraulic cylinders can be produced.
6.6 Electrostatic effects
Electrostatic charge is caused due to friction and separation of charge.
This phenomenon is widely known and can be produced e.g. by
carpets or car seats. Mostly, the charge is noticed only in the event of
discharge, when the associated „shock“ occurs. The voltages due to
electrostatic discharge can have very high values, for example:
• Walking over carpet floors up to 30,000 V
• Walking over synthetic floors up to 12,000 V
• Moving at the workplace up to 6,000 V
Not only the high voltages, but especially the sudden discharge and
related currents (up to 50 Ampere!) can cause destruction of electrical
components. The effects are similar to those occurring due to
electrostatic discharge during dry painting.
5
10
15
0
0
10
20
30
40
50
Initial spike, discharge of hand capacitance
Discharge of body capacitance
Time [ns]
Amplitude [A]
Fig. 16: Current flow curve during electrostatic discharge of a human body
Current flow curve during electrostatic discharge of a human body
To avoid electrostatic discharge, workplaces and persons working
with or on electronic components must be grounded. This also applies
to sensor installation into the hydraulic cylinder as well mounting
procedure the cylinder to the machine.
Suitable protective measures are:
• Persons wear ribbons connected to the grounding point by means
of spiral cable around their wrist. Please, contact us, if you need
information on suppliers for suitable protective equipment.
• Work is only performed on diverting material, i.e. charges can
be diverted gently (e.g. work plate of wood, rubber, ESD foam
material).
• Avoid hard discharge. Do not deposit components on metal plates
or metal film.
• Do not remove electrostatically sensitive components from the
packaging without grounding.
• Caution when cutting adhesive tapes, do not tear to open.
6.7 Compatibility of seals with hydraulic oils
The sensors with a measuring rod are designed for installation in
hydraulic cylinders. The seals used in the sensors come into contact
with the hydraulic oil. Hydraulic oils that are moderately to not
compatible with the material of the seals can damage the seal.
In general, sensors from MTS Sensors are equipped with seals made
of NBR, FKM and PTFE. These seals can be used with hydraulic oil
type HLP (according to DIN 51524-2).
Other oils, such as bio oils (e.g. HEES, HETG and HEPG), are, without
prior testing, bio-oils should not be used on sensor seals. Due to the
large number of different oils and their different mixing ratios, not all
seal materials can be tested with the corresponding oils. These tests
are very time-consuming and therefore cost-intensive. It should also
be noted that the composition and mixing ratios of oil types change
continuously.
If hydraulic oil other than type HLP is to be used, we recommend
testing the oil-seal combination in a test laboratory. Two tests are
required per oil seal combination:
• Storage in oil for 1000 hours at an oil temperature of 80 °C
• Storage in oil for 168 hours at an oil temperature of 100 °C
During these tests, the components must be extensively tested for
installation dimensions.