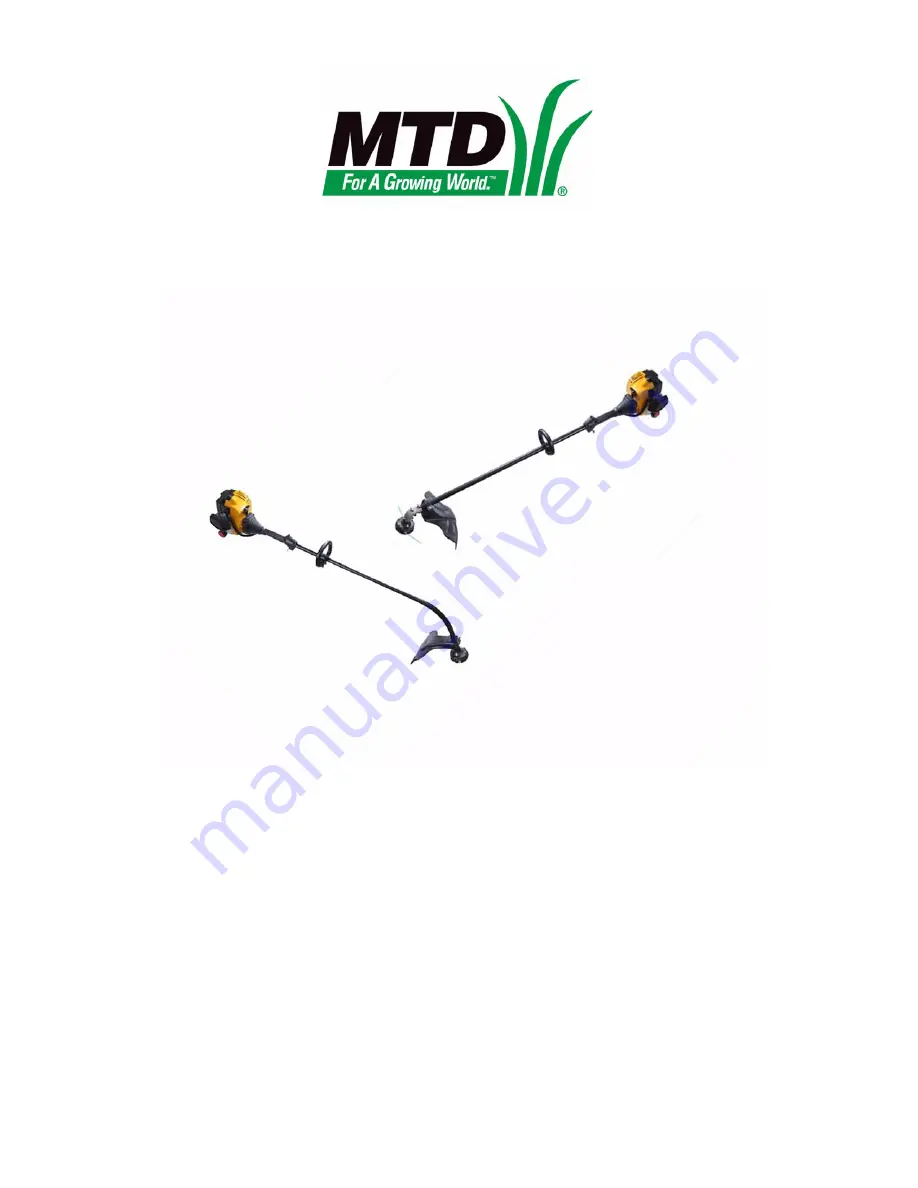
Professional Shop Manual
25cc 2-Cycle P25 Series Engines
NOTE:
These materials are for use by trained technicians who are experienced in the service and repair of outdoor power
equipment of the kind described in this publication, and are not intended for use by untrained or inexperienced individuals.
These materials are intended to provide supplemental information to assist the trained technician. Untrained or inexperi-
enced individuals should seek the assistance of an experienced and trained professional. Read, understand, and follow all
instructions and use common sense when working on power equipment. This includes the contents of the product’s Oper-
ators Manual, supplied with the equipment. No liability can be accepted for any inaccuracies or omission in this publication,
although care has been taken to make it as complete and accurate as possible at the time of publication. However, due to
the variety of outdoor power equipment and continuing product changes that occur over time, updates will be made to these
instructions from time to time. Therefore, it may be necessary to obtain the latest materials before servicing or repairing a
product. The company reserves the right to make changes at any time to this publication without prior notice and without
incurring an obligation to make such changes to previously published versions. Instructions, photographs and illustrations
used in this publication are for reference use only and may not depict actual model and component parts.
© Copyright 2010 MTD Products Inc. All Rights Reserved
For Parts Call 606-678-9623 or 606-561-4983
www.mymowerparts.com
Summary of Contents for 25cc
Page 2: ...For Parts Call 606 678 9623 or 606 561 4983 www mymowerparts com...
Page 14: ...P25 Series of engines 10 For Parts Call 606 678 9623 or 606 561 4983 www mymowerparts com...
Page 28: ...P25 Series of Engines 24 For Parts Call 606 678 9623 or 606 561 4983 www mymowerparts com...
Page 62: ...P25 Series of Engines 58 For Parts Call 606 678 9623 or 606 561 4983 www mymowerparts com...
Page 63: ...For Parts Call 606 678 9623 or 606 561 4983 www mymowerparts com...