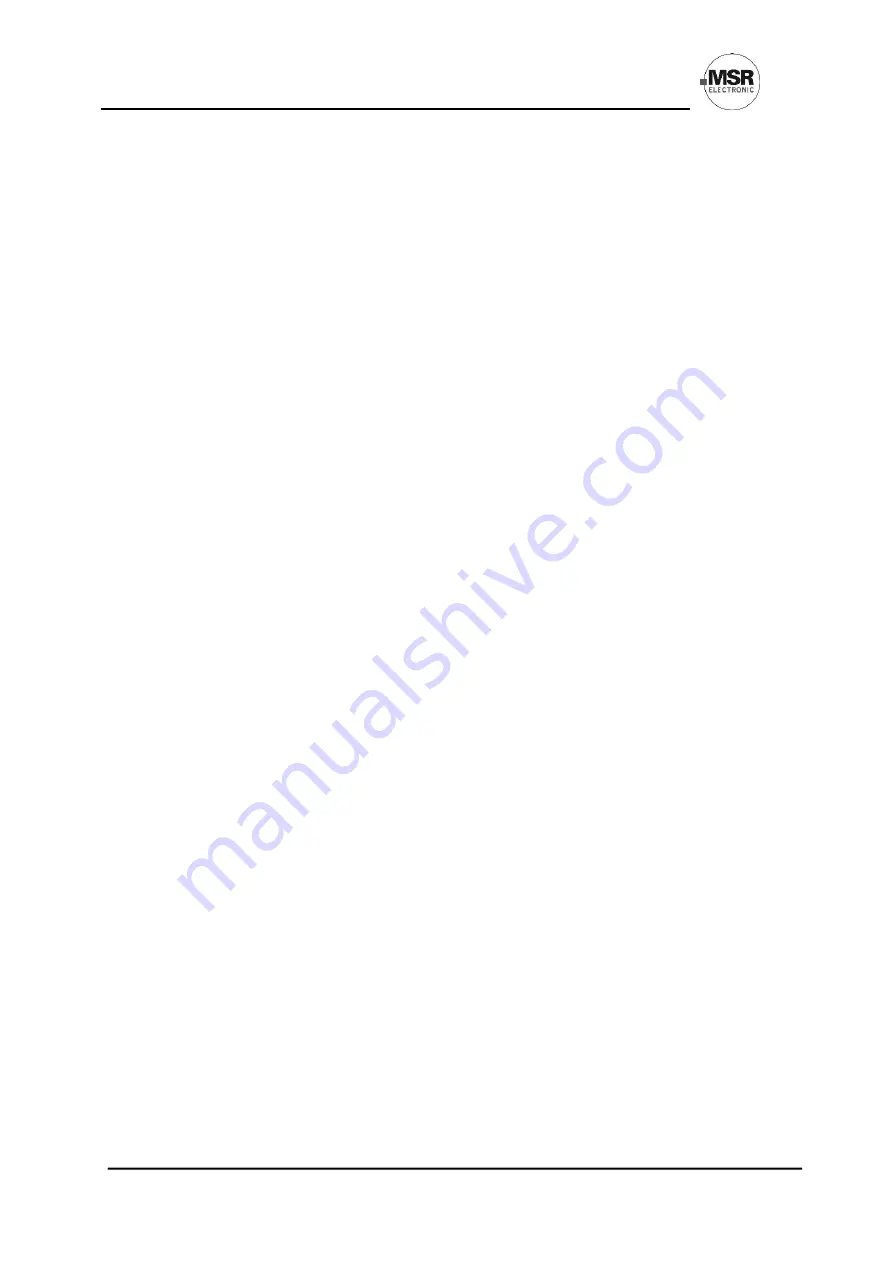
User Manual - PolyXeta
®
2 Detector with HL Sensor
for Refrigerant Gases - May_2020
Page
17
PolyXeta
is a registered trademark of MSR
Made in Germany
GAPX2_Freon_E_2020_05_18
Phone: +49 8531 9004-0 Fax: +49 8531 9004-54
Specification subject to change without notice
MSR-Electronic GmbH, Buergermeister-Schoenbauer-Str. 13, D 94060 Pocking
www.msr-electronic.de
7
Notes on Usage
7.1
Ambient Conditions
The PX2 gas detector series is intended for continuous, fixed monitoring of gas-air mixtures under
atmospheric conditions.
The
PX2-1
gas detector series is marked with the device category II 2 G and thus approved for use in
hazardous areas of zones 1 and 2. The
PX2-2
gas detector series is marked with the device category II
3 G and thus approved for use in hazardous areas of zone 2.
The PX2 gas detector series is approved for an oxygen-enriched atmosphere of maximum 25% vol.
oxygen.
Permitted ambient temperature range for version without display: -25 ° C < Ta < +60 ° C
Permitted ambient temperature with display: -20 °C <Ta <+60 °C
Permitted ambient humidity range: 20 to 90 % RH non-condensing.
With a humidity level above this
limit, reliable gas detection is no longer guaranteed. A functional test according to Chapter 8.2
has to be carried out then.
Operating pressure range: 800 to 1200 mbar ¨
Flow speed: 0 to 6 m/s. Use a special wind screen for stronger air flow.
Mounting position: wall mounting with the sensor downwards to prevent dust and liquids from
clogging the gas inlet.
The PX2 gas detector must not be exposed to direct sunlight to avoid overheating.
High concentrations of certain compounds may contaminate the sensor when used for a longer period.
In environments contaminated with such substances, calibration has to be performed more frequently
to ensure reliable operation.
Dust deposits at the gas inlet can significantly extend the response time. Therefore check the device
regularly for dust deposits and clean it, if necessary.
In addition, a functional test according to
Chapter 8.2 should be carried out after cleaning.
During painting, care should be taken that the gas inlet is not clogged with paint deposits. Emissions
of colours, such as solvents, etc. can affect the performance of the sensor or damage the sensor
completely. Therefore, we recommend sealing the gas inlet when painting.
Certain substances and gases in the monitored ambient can affect the sensitivity of the sensor
element or destroy the sensor completely. This is called poisoning. The following are currently known:
•
Polymerizing substances, such as ethylene oxide, acrylonitrile, butadiene, styrene, silicone.
•
Corrosive substances, such as halogenated hydrocarbons.
•
Catalytic poisons, such as sulphur and phosphor compounds, silicon compounds, metal vapours.
Depending on the type of built-in sensor head the PX2 gas warning device is used for:
- Monitoring of the ambient air to detect Freon refrigerant gases according to the built-in sensor head.
Series PX2-X-X-X
2X
XX-X
7.2
Further Notes and Restrictions
The maximum operating voltage and the terminal voltage of the relays have to be limited to 30 V by
adequate measures. The maximum switching current of the two relay contacts should be limited to 1 A by
appropriate external measures.
Concerning the cable specification, the details of the cross-sections and lengths in the table 4.1 Cables must
strictly be followed.
Repairs to pressure-resistant slits are not intended and lead to the immediate loss of the type approval for
the pressure-resistant casing.