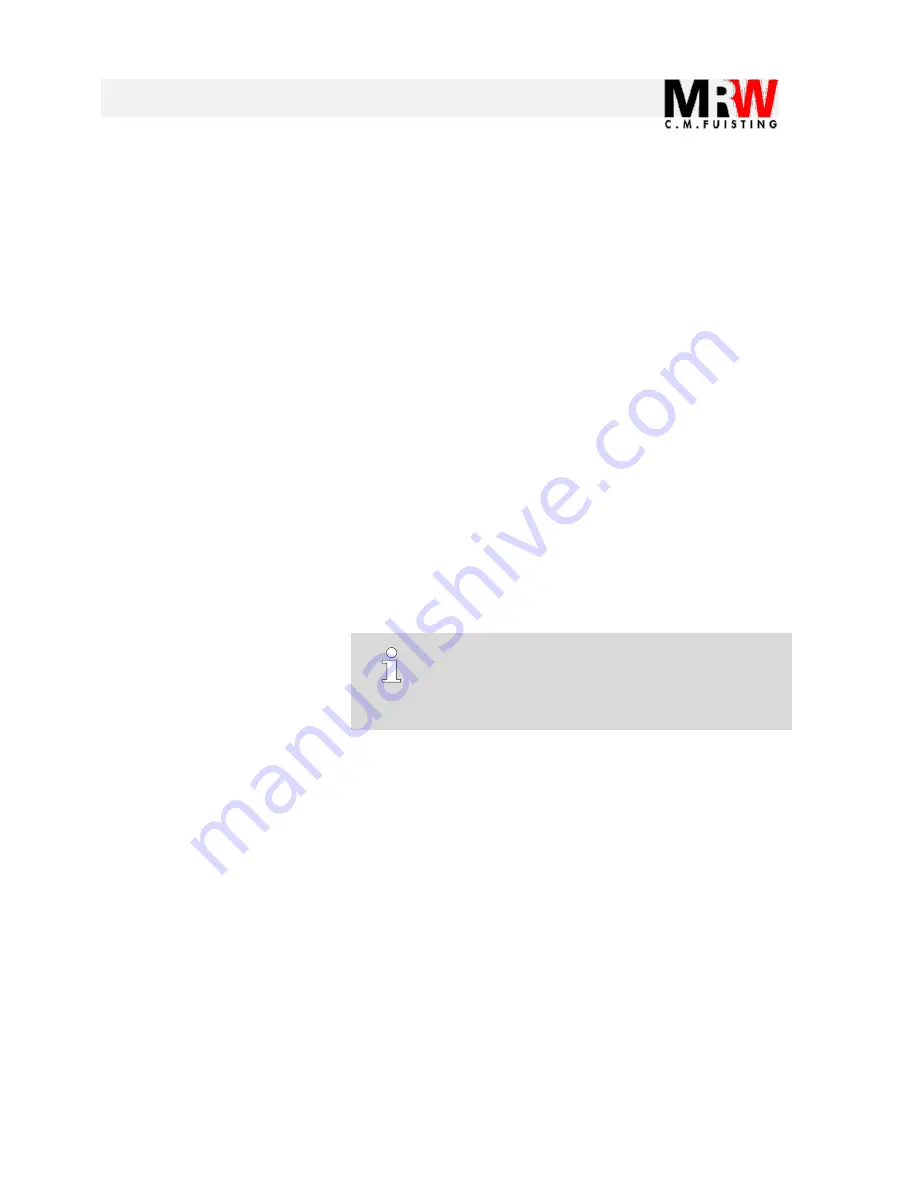
MRW Vib-Control 04
18 v. 34
27. Oktober 2014
Structure
and function
4.4
Explanation of special menu functions
Freq. Automatic
Each vibratory driver has a natural frequency. It is mostly set to
50/60 Hz (mains frequency) or the respective double value by the
manufacturer.
This natural frequency changes if superstructural parts and loads
are placed on the vibratory drive.
Instead of bringing in the natural frequency to the target value again
with time-consuming work by means of spring configuration,
gyrating mass and clearances, the Vib-Control 04 control unit can
search for the new natural frequency and operate the device with
the new optimal frequency.
After starting the frequency search, the software of the Vib-Control
04 tests the frequency band of 147 - 17 Hz and measures the
power consumption of the vibratory drive. The optimal frequency for
operating the “vibratory drive and superstructure” unit is determined
in this way.
A prerequisite for a successful frequency search is a fault-free
vibratory drive (clearances, coils and springs in perfect condition)
and a firm connection between the vibratory drive and the
superstructure. Loose parts on the superstructure interfere with the
frequency search.
Tips and recommendations
NOTE!
If the magnets strike their counter-bearings during the
frequency search, the maximum feed performance can
be limited in the “Max speed” menu before the
frequency search.
Frequency preselection
For vibratory drives with unstable superstructures, the optimal
vibration frequency can be set manually.
It is best to start with the rated frequency of the drive (this can
mostly be found on the type plate).
The power consumption of the drive is always displayed as a guide.
The lower the power consumption, the closer it is to the natural
frequency or the harmonised frequency (double / half value) and the
system is protected.
If one observes the parts to be fed in the superstructure of the
vibratory drive at the same time, the optimal compromise between
power consumption and feed performance can be found.