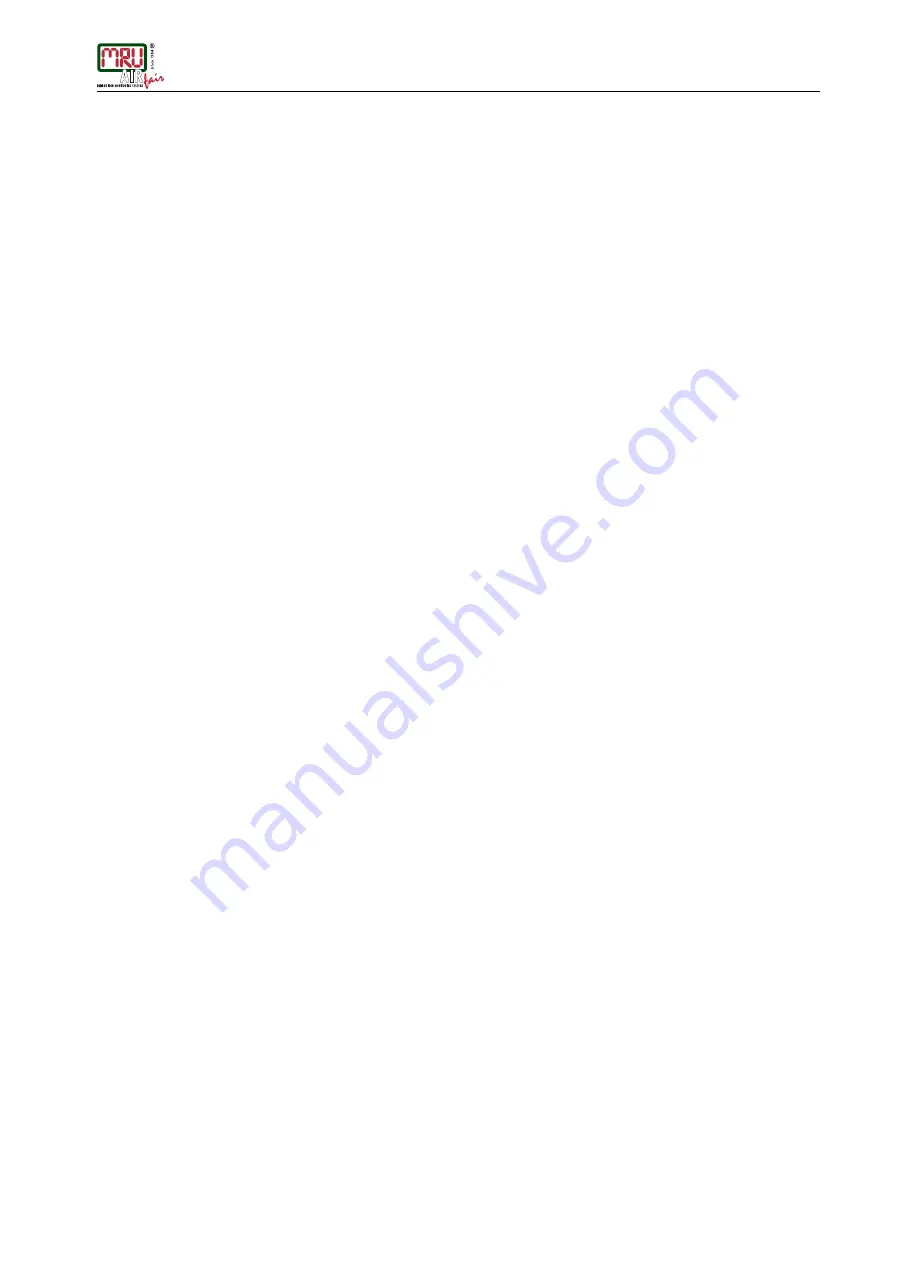
OPERATING MANUAL OXYGEN MONITORING SYSTEM
OMS 420
8
4
Safety
•
The O
2
probe may only be used in original, undamaged condition and in accordance with the operation manual.
•
All individuals dealing with the installation, commissioning, operation and maintenance of the analyzer or probe must be
qualified to do so and must strictly observe this operation manual.
•
Unauthorized modifications to any part of the analyzer or probe can create safety risks and are not permitted.
•
Power other than that specified in this manual must never be provided to the probe.
•
Service of transmitter electronics by non skilled personnel is not allowed.
•
Do not allow condensate to come into contact with the sensors.
•
Do not attempt to clean the probe with water.
•
The probe shall not be used in under-stoichiometric combustion conditions, due to the possible presence of flammable
gases, eventually over the LEL (low explosion level).
•
Power must always be provided to the probe, even during boiler shut-down, to prevent the formation of condensate
which can damage the sensors.
•
Do not use the probe for any purpose other than that specified in this manual.
•
Exposure to corrosive gases such as silicone vapor, alkaline and heavy metals, P, Pb, high SO
2
, etc. will shorten the life
time of the sensors.
•
It is mandatory to the user to insure that all persons operating this equipment are properly trained in
its operation and fully understand the operating principals of the equipment.
•
MRU GmbH, its affiliates and agents cannot be held responsible in any way for damage or injuries re-
sulting from improper use, misuse or neglect in operating this equipment.
Caution
Probes installed inside flue ducts and stacks operate at elevated temperatures (often 1.000
o
F and higher) cre-
ate danger of serious skin burns to operators if proper handling precautions and extreme care are not taken.
www.
GlobalTestSupply
.com
Find Quality Products Online at: