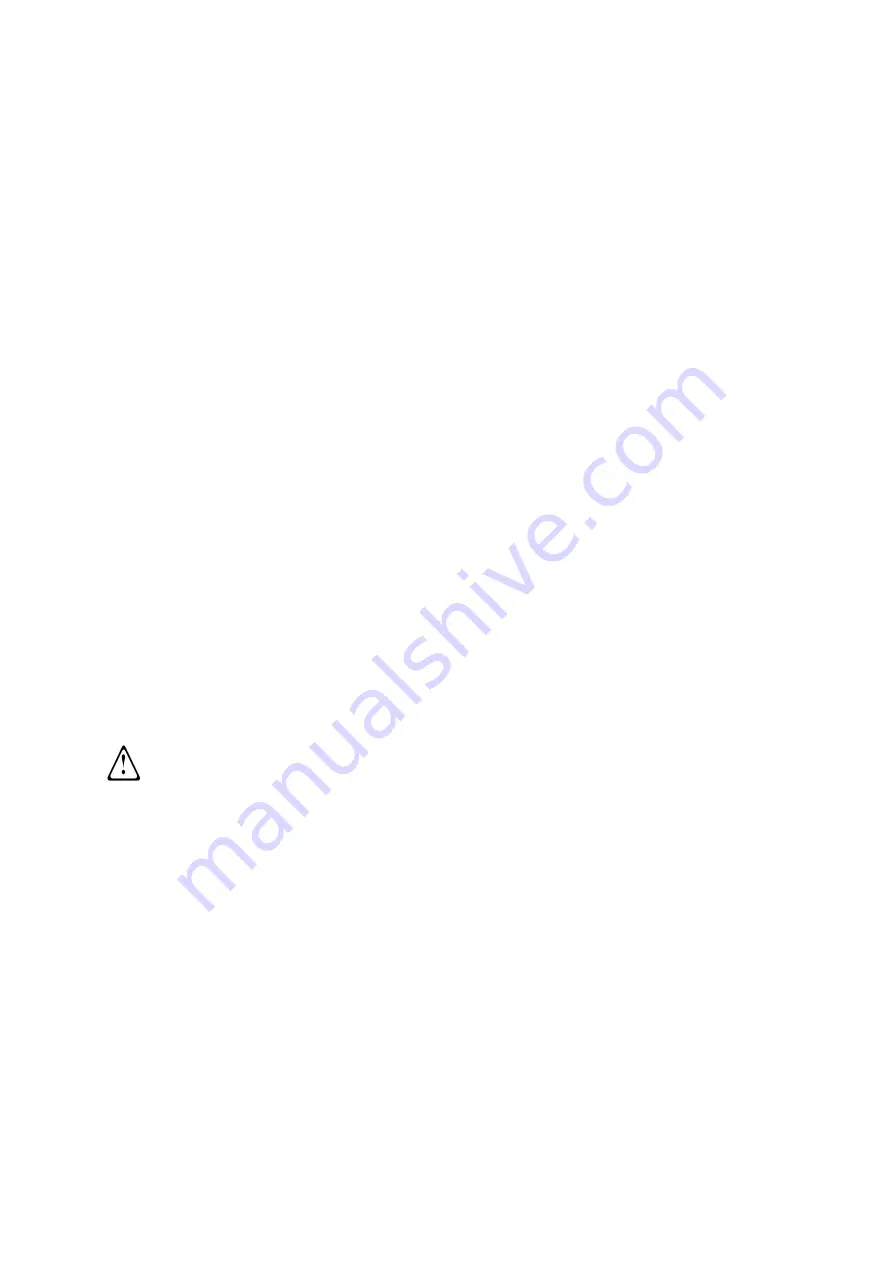
20
I. Emergency stop switch
The function of emergency stop switch is to make the machine stop immediately in any case, to
prevent the expansion of injury or loss.
J. Air switch
The function of air switch is to provide protection for the short circuit, severe overload and
under-voltage of the circuit or electrical equipment.
2.3 Precautions for Use
Before
starting
up
the
machine
for
the
operation,
please
confirm
the
rated
voltage
and
frequency
of
the
equipment
and
the
parameters
of
the
input
power
are
consistent
again,
so
as
not
to
damage
the
electrical
components,
and
even
lead
to
fire
A
reliable
grounding
operation
must
be
performed
on
the
equipment
to
ensure
safe
use
If
abnormal
noise,
odor,
smoke,
etc.
occur
during
use,
disconnect
the
power
supply
immediately.
Users
should
not
blindly
hands-on
repair,
but
notify
MRC
maintenance
department
or
local
special
maintenance
point,
and
the
equipment
should
be
checked,
repaired
by
the
professional
technical
personnel
When
the
dispensing
booth
is
working,
do
not
rinse
the
cabinet
directly
with
water,
otherwise
it
will
cause
malfunction,
leakage,
and
even
fire
Please
put
down
the
transparent
curtain
when
the
dispensing
booth
is
being
used
There
is
airflow
regulating
panel
on
the
upper
front
cabinet
of
the
dispensing
booth,
the
equipment
has
been
tested
in
the
factory
and
well
adjusted,
the
user
is
not
allowed
to
adjust
arbitrarily
When
the
dispensing
booth
is
in
the
sterilization
process,
the
staff
shall
not
enter
the
work
area,
to
look
the
UV
germicidal
lamp
directly
is
prohibited
2.4 Daily Maintenance
Maintenance should be done every year or every 1000 work hours, and every restart.
Please firstly turn off the power before conducting the daily maintenance;
Since the statistics of the operating time will directly affect the judgment of the
maintenance needs, we recommend that you can prepare a detailed record of the
operating time for reference and inquiry when you are using the equipment;
Maintenance method
:
Daily or weekly maintenance
Surface cleaning: In order to keep the cabinet clean, please regularly (at least once a week)
clean it. The wipe should be done with a dry soft cloth with soapy water being wringed. Do
not spray any chemical reagents on the operator panel or other labels to prevent
discoloration of the label film or the writing is unclear . Clean the outer surface of the
cabinet and the anti-static curtain with a flexible detergent or glass-specific cleaning agent.
Check whether the various functions of the equipment are abnormal;
Record the maintenance.
Monthly maintenance
Regularly replace or clean the filter (when the pressure is more than 1.5 times of the initial