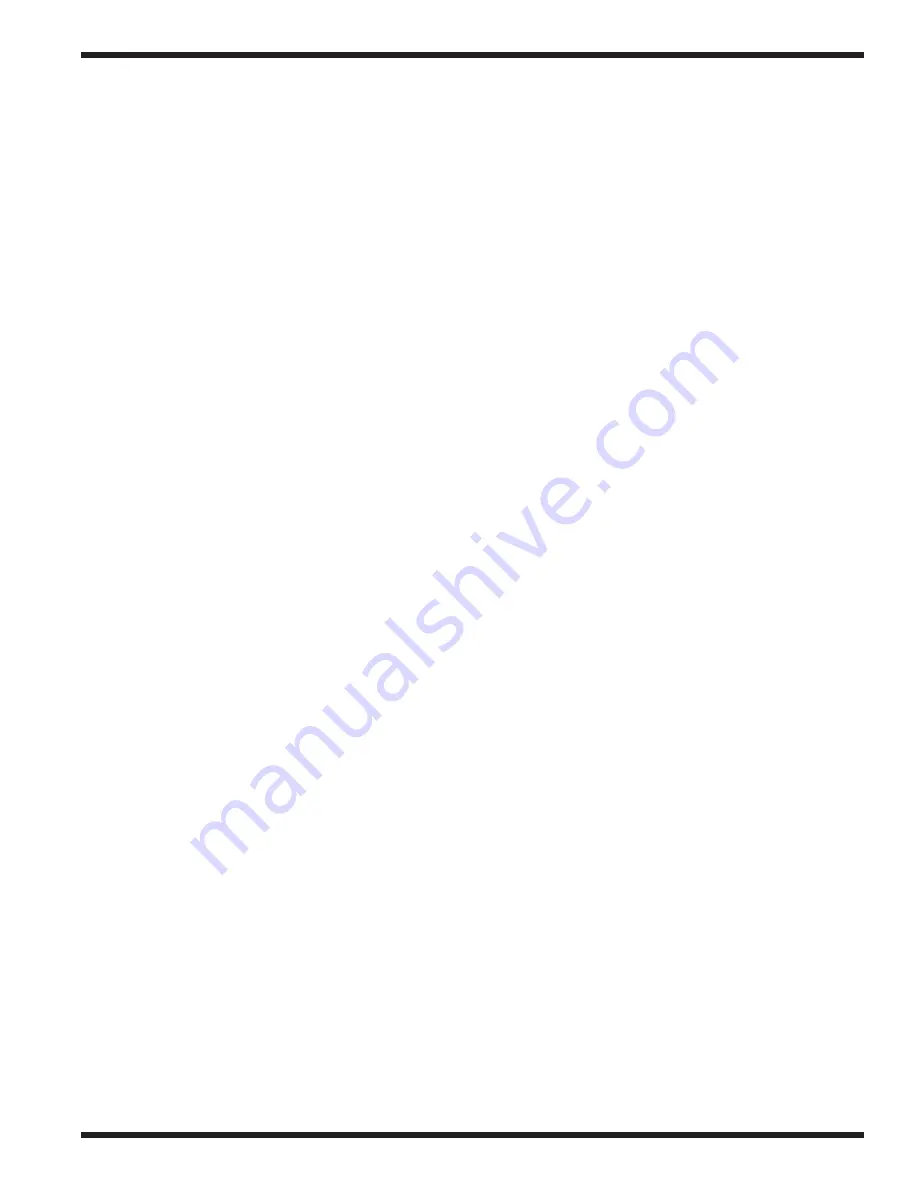
5
MAINTENANCE:
IMPORTANT:
Before carrying out the cleaning and maintenance operations, turn off the main discon-
nect switch for the equipment.
Frequently check and clean the nozzles. Blocked nozzles will prevent the machine from
cleaning properly.
Do not use corrosive products such as sodium hypochlorite (bleach), acids, steel wool or
steel brushes to clean the inside and outside of the machine.
The presence of calcium and magnesium salt in the water can compromise machine
performance. Ask a qualified chemical person to remove the deposits periodically.
Stainless steel surfaces should be well cleaned in order to avoid some oxidation risks, or
chemical reactions.
OPTIMAL RESULTS:
Poor wash results can be noted when residue remains on the dishware.
Poor results can be caused by an insufficient rinse: in this case check that the rinse nozzles
are clean and that there is sufficient water supply pressure (20-22 PSI/138-151 kPa) during
machine rinse cycle..
In case of dishware residue check that:
• the washing nozzles are clean
• the wash water temperature is a minimum of 60°C/140°F
• there is detergent in the container
• the pump suction filter is clean
• the racks are suitable for the dishes and cutlery that are to be washed
• the position of the cutlery and the dishes in the racks are correct
• the racks are not overloaded with wares
TEMPORARY MACHINE NONUSE:
In case the machine is not used for a prolonged period, it is recommended to fill the
wash tank and run the machine with clean water, then drain, in order to avoid the
forming of bad odors.
If necessary repeat this step until all water leaving the machine is clean.
If the machine is not used for long periods, it is recommended to oil the stainless steel
surfaces with paraffin oil and to empty the water from the booster tank and the wash
pump.
PART 1:
OPERATION
Summary of Contents for MH65-M2
Page 4: ...ii REVISION RECORD Revision Record CONT ...
Page 8: ...vi ThisPage Intentionally Left Blank Part 1 INSTALLATION AND MAINTENANCE ...
Page 18: ...10 This Page Intentionally Left Blank ...
Page 19: ...11 Part 3 REPLACEMENT PARTS PART3 REPLACEMENT PARTS ...
Page 20: ...12 Part 3 REPLACEMENT PARTS Figure 3 1 Hood and Tank 1 2 1 B 4 A A A 7 3 5 6 6 ...
Page 26: ...18 Part 3 REPLACEMENT PARTS Figure 3 4 Tracks and Screens 2 1 3 See Note on Parts ...
Page 30: ...22 Part 3 REPLACEMENT PARTS Figure 3 6 Wash Tank Components 13 12 10 6 5 1 2 3 9 8 7 14 15 ...
Page 36: ...28 Part 3 REPLACEMENT PARTS Figure 3 9 Wash PumpAssembly 1 2 3 4 5 6 7 A A ...
Page 46: ...38 Part 3 REPLACEMENT PARTS ThisPage Intentionally Left Blank Part 4 ELECTRICAL SCHEMATICS ...
Page 47: ...39 Part 3 REPLACEMENT PARTS Part 4 ELECTRICAL SCHEMATICS PART 4 ELECTRICAL SCHEMATICS ...
Page 48: ...40 Part 3 REPLACEMENT PARTS ThisPage Intentionally Left Blank Part 4 ELECTRICAL SCHEMATICS ...
Page 51: ...42 REPLACEMENT PARTS ...