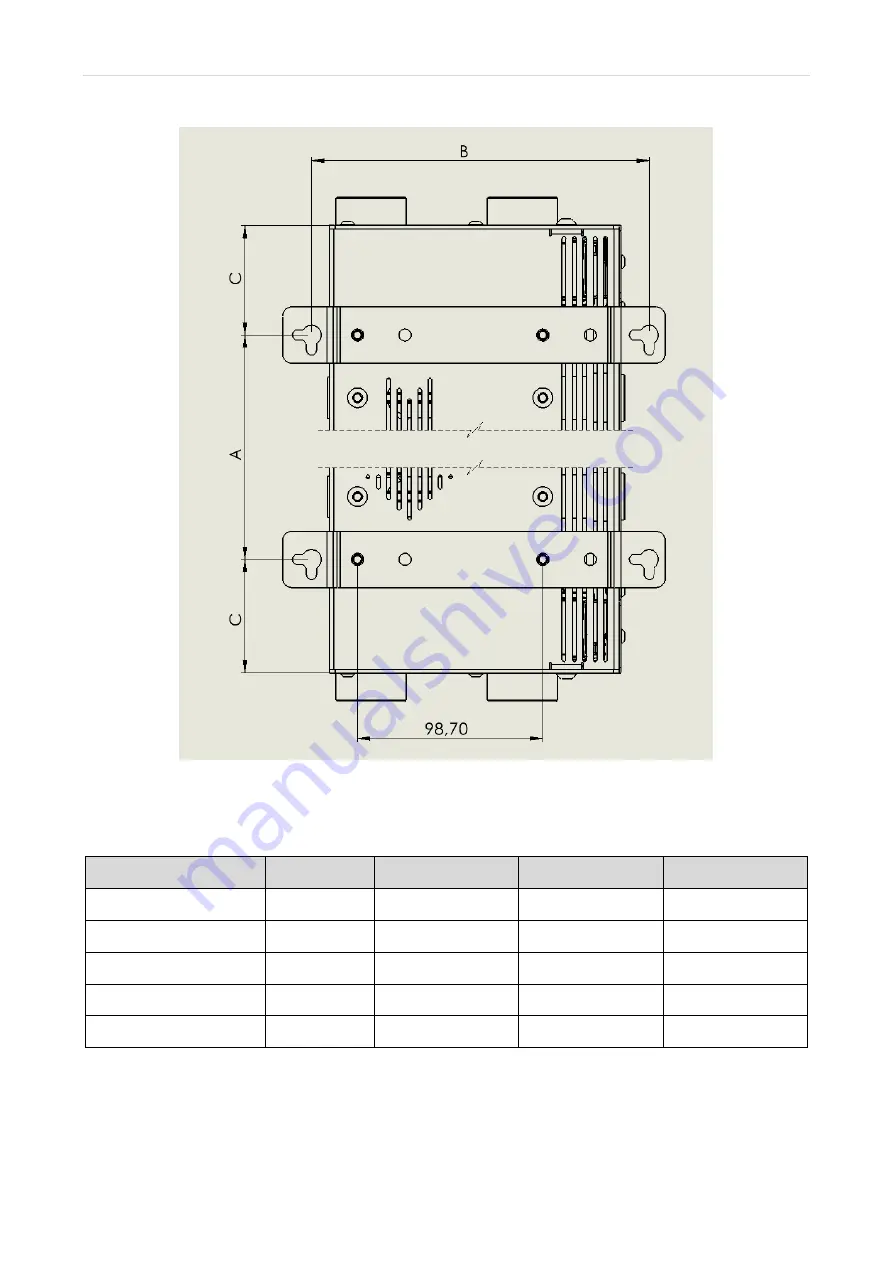
P a g e
|
16
User Guidelines
– Flosense 4.0 Manifold 16-06-2020
Version 002
The position of the holes for the bracket can be seen in the figure above, and the dimensions
for each model can be seen in the table below.
Model
Channels
A [mm]
B [mm]
C [mm]
Flosense 4-Zone
4
100.50
180
59.5
Flosense 6-Zone
6
167.50
180
59.5
Flosense 8-Zone
8
234.50
180
59.5
Flosense 10-Zone
10
301.50
180
59.5
Flosense 12-Zone
12
368.5
180
59.5