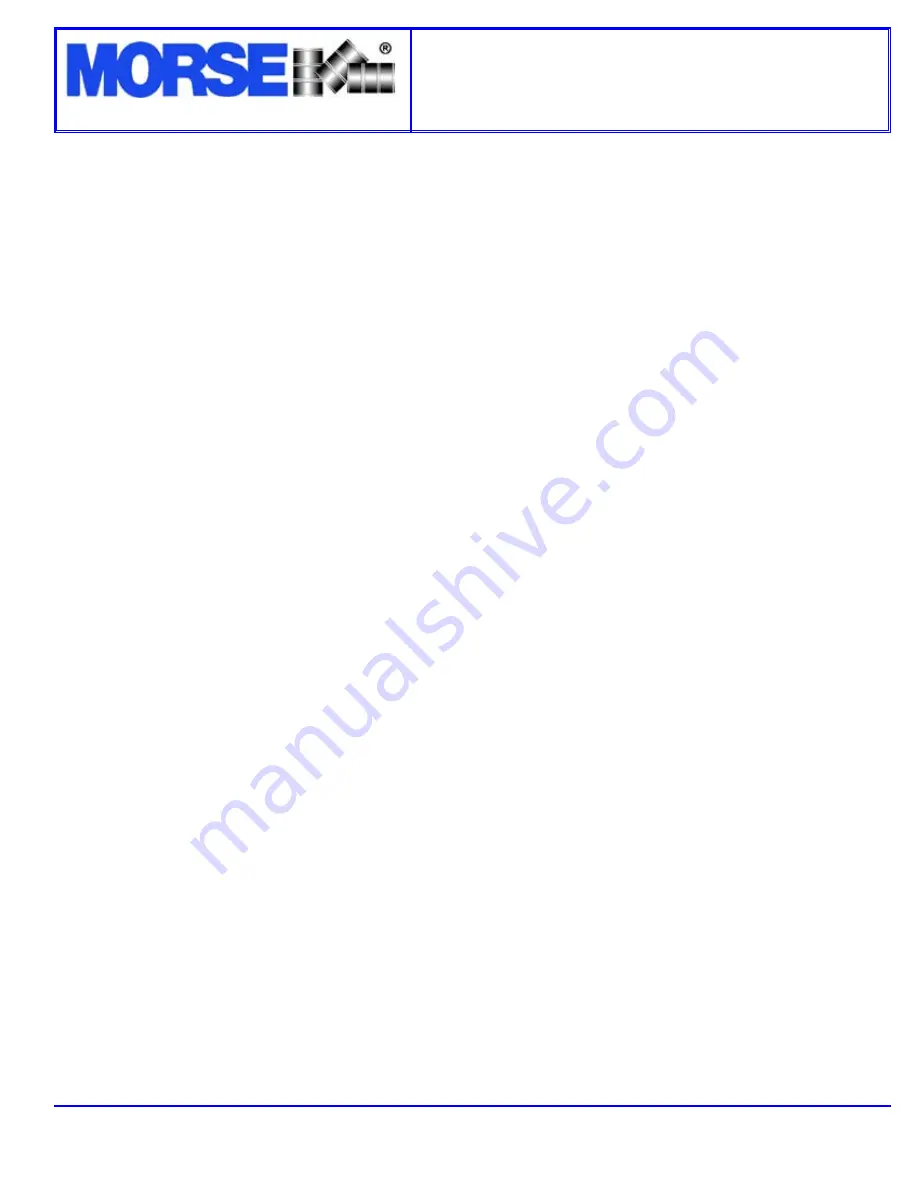
Copyright 2010 - Morse Mfg. Co., Inc.
Form PL400Z-60 (0604-0110) (Updated 04/2010)
Page 7
Maintenance
Periodic inspection for the general condition of structural and mechanical components is imperative for safe and efficient
operation.
Periodically inspect all moving parts, framework, and contact areas for signs of wear, fatigue, or loosening. Tighten, adjust, or
replace parts as necessary to prevent failure and maintain proper function.
Inspect the hydraulic system for oil drips, hose damage, or other signs of wear. Inspect the level and condition of the hydraulic
fluid. Replace any parts that show signs of wear.
Grease wheel bearings periodically. Oil or grease all moving parts including: the three clevis pins and the surfaces of the boom
which contact the inside of the mast cap, the hinge pin, the gears and sprockets in the tilt drive, and the ratchet and pawl.
Worn or damaged parts must be properly replaced with the correct, genuine Morse parts.
Operator’s Manual for Morse Hydra-Lift Drum Karrier Model 400Z-60
Serial Number 0604 to 0110 (MMYY)
The Specialist In Drum Handling Equipment
MODEL 400Z-60
Hydra-Lift, 60”, Manual Lift, Manual Tilt