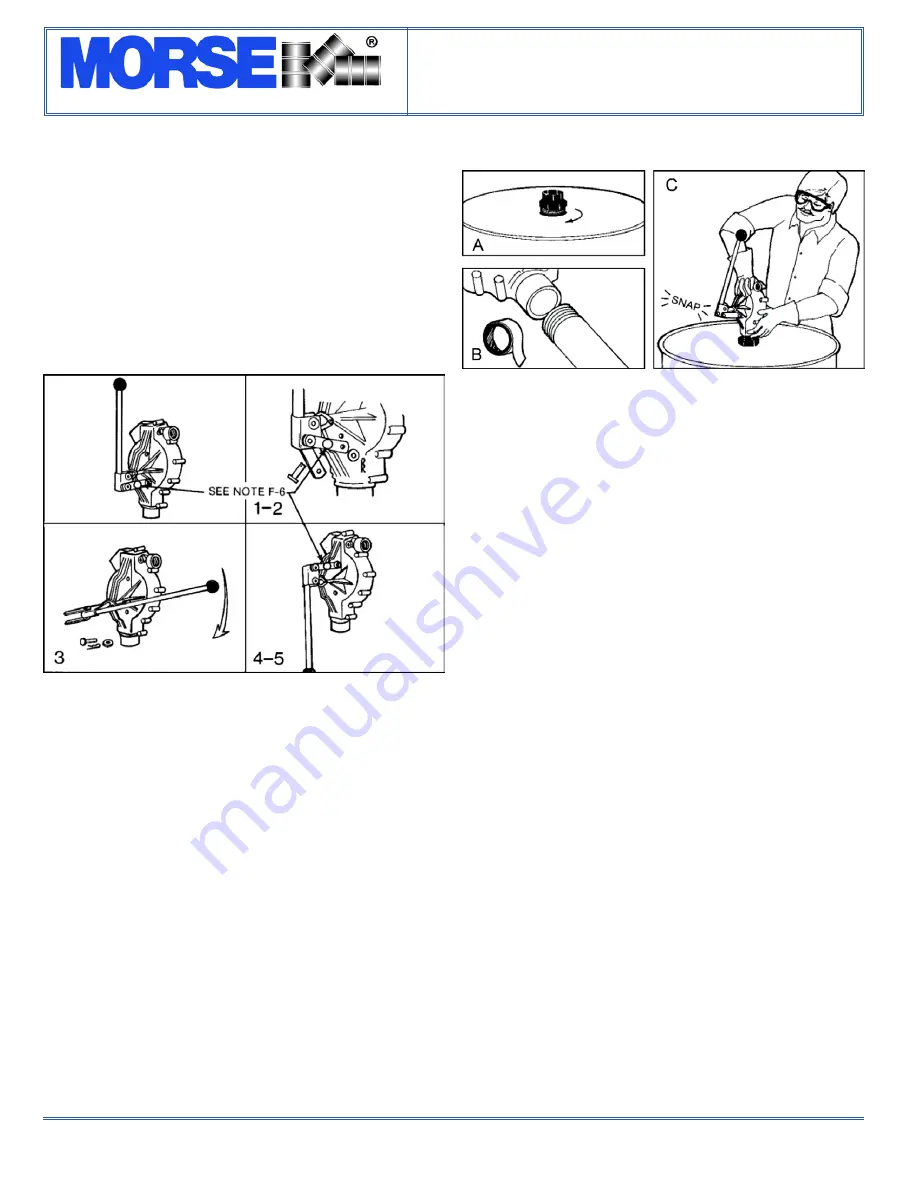
The Specialist In Drum Handling Equipment
Drum Pumps
morsedrum.com
Copyright 2019 - Morse Mfg. Co., Inc.
Form PL26
(Updated 11 Jun, 2019)
4
Pump operating Instructions
FoR eAsY InstALLAtIon FoLLoW tHese stePs In tHe
oRDeR sHoWn.
Screw the bung adaptor into the drum or barrel. Be sure not to
A.
overtighten (Refer to Safety Precautions step H on page 3).
Install supplied clamp loosely around bung adaptor.
B.
Thread appropriate length of suction tube and extension
C.
tube(s) into pump section. Use teflon tape provided (Refer to
Safety Precautions step H on page 3).
Install pump and tubing into bung adaptor by pushing straight
D.
down firmly. Housing will snap in place. Tighten the clamp
(item 31). Screw hose and adaptor or discharge spout into
pump body.
Caution: When pumping from a lined drum, order part item
E.
58-0069. This is a flexible suction tube to prevent damage to
the liner.
The handle position can be changed with the following steps.
F.
Remove hairpin clip (item 6) from clevis pin (item 7).
1.
Remove clevis pin from housing to free links (item 8).
2.
With links clear of housing, rotate handle 1/2 turn to new
3.
position.
Install clevis pin through the links and the opposite hole in
4.
housing.
Install hairpin clip through the hole in the clevis pin.
5.
Ensure the flat washer (item 4) is installed between the
hairpin clip and the link.
CAUTION: This hole is used for security lock only.
6.
Remove hose from hanger and place nozzle in container.
G.
Operate handle to prime the pump. 3-6 strokes are required under
most conditions. After the pump is primed it will deliver about one
gallon for every four full strokes (backward and forward).
Two Position Pump Handle
trouble shooting Guide
A. pump will not prime
Clogged suction. Check that the suction tubes are clear and
1.
that the screen filter is not dirty or clogged. Use a pair of
needle nose pliers or a stiff piece of wire to pull the suction
screen from housing. Clean it, if necessary, and push it gently
back into the housing or with a fi nger or blunt rod.
Air leakage. Check that the connection to housing, extension
2.
tube and suction tube are threaded tightly and sealed with
teflon tape (Refer to Safety Precautions step H on page 3).
Piston leakage. Verify that the teflon ring fits snugly in bore
3.
and is not cut or excessively worn.
Valve leakage. Inspect poppet valves for weak springs
4.
or clogging. If pump was recently disassembled VERIFY
PROPER POSITION OF VALVE SEATS (Refer to
Maintenance step B.1. on page 5).
Gasket leaks. Inspect for torn gasket (item 18), poor fit or
5.
loose coverplate bolts (item 20).
B. not enough Flow
Check items A. 1-5.
1.
Check discharge hose for clogging or pinching. Verify that the
2.
nozzle is not clogged.
Check that piston is travelling its full stroke and the linkage
3.
has not bound or jammed.