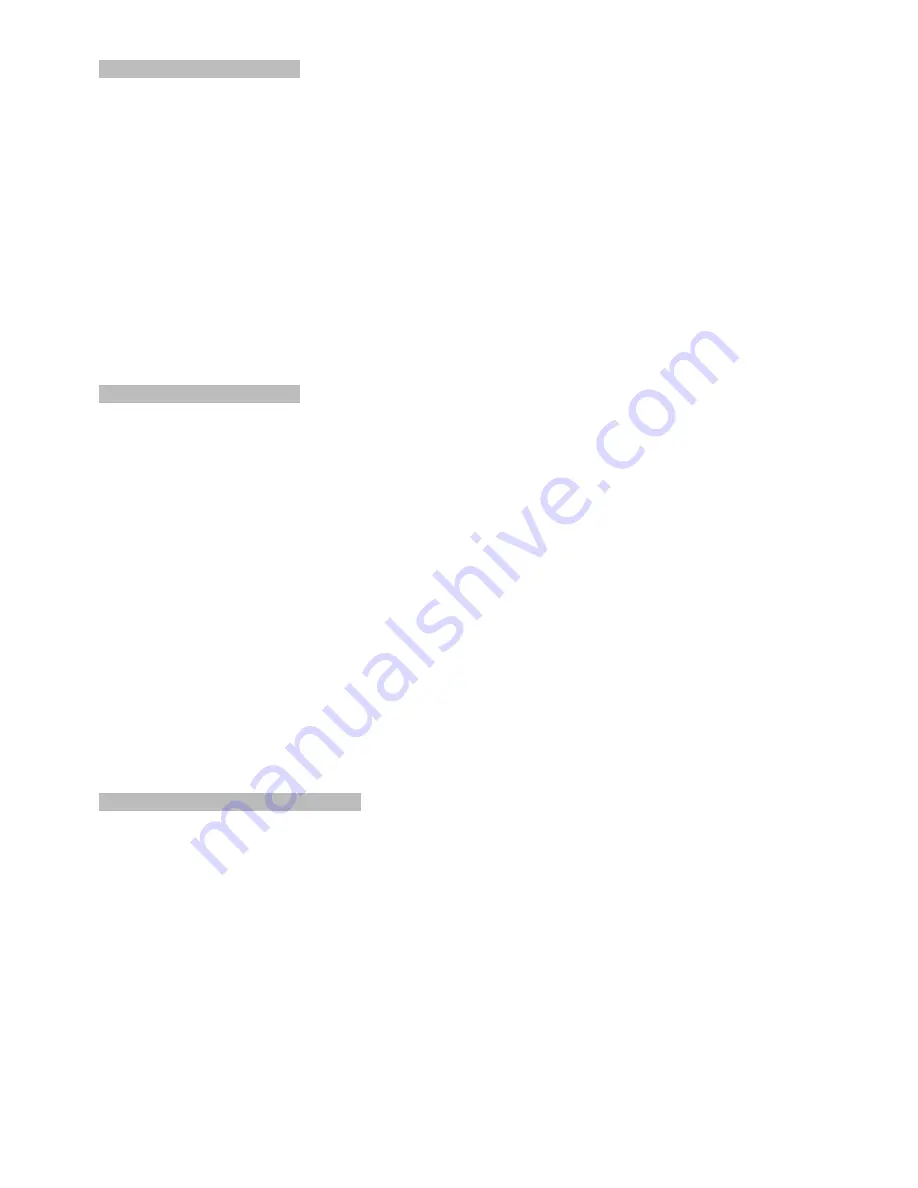
F. Leak detection method
For systems containing flammable refrigerants, the following methods for detecting leaks are
acceptable:
Electronic leak detectors can be used for the detection of flammable refrigerants, but the
sensitivity may not be sufficient or may require recalibration (the instrument calibration should
be performed in a refrigerant-free environment) to ensure that the leak detector does not
become a potential The ignition source, and applies to the measured refrigerant, the leak
detector should be set to the lowest flammable concentration of the refrigerant (in percent),
calibrated with the used refrigerant and adjusted to the appropriate gas concentration test
range (max. 25%)
The leak detection fluid is suitable for most refrigerants, but do not use oxygenated solvents to
prevent oxygen and refrigerant from reacting and corroding the copper pipeline
If leakage is suspected, all open flames should be removed from the site or extinguished
If a leak occurs where welding is required, all refrigerant should be recovered, or the refrigerant
should be completely isolated away from the leak (using shut-off valves). Before welding and
during welding, use oxygen-free. Nitrogen (OFN) purifies the entire system
G. Remove and vacuum
When performing maintenance or other operations on the refrigeration circuit, routine
procedures should be followed, but the flammability of the refrigerant should also be
considered. Follow these procedures:
- Clear refrigerant
- Purge the line with inert gas
- Vacuum
- purge the pipe again with inert gas
- cutting pipelines or welding
Refrigerant should be recycled to a suitable storage tank. The system should be purged with
oxygen-free nitrogen to ensure safety. This process may need to be repeated several times.
This operation must not be performed with compressed air or oxygen.
In the purging process, the system is filled with oxygen-free nitrogen to reach the working
pressure under the vacuum state, and then the oxygen-free nitrogen is discharged to the
atmosphere. Finally, the system is evacuated to a vacuum, and the process is repeated until
the refrigerant in the system is completely removed. After the last charge of anaerobic nitrogen,
the gas is released to atmospheric pressure and the system can then be welded. Such as pipe
welding operations, the above operation is very necessary
Make sure there are no ignition sources near the outlet of the vacuum pump and that it is well
ventilated.
H. Charge the refrigerant program
As a supplement to regular procedures, add the following requirements:
-Ensure that when using the refrigerant charging equipment, no inter-contamination between
different refrigerants will occur, and the piping for charging the refrigerant should be as short as
possible to reduce the residual amount of refrigerant therein
- Tanks should be kept vertically upward
- Ensure that the cooling system has been grounded before filling the refrigerant
- Label the system after filling (or when it has not been completed)
- Must pay attention not to overcharge
The pressure test was performed with oxygen-free nitrogen before recharging the system.
After the filling was completed, a leak test was performed before the test operation. A leak test
should be conducted when leaving the area
16