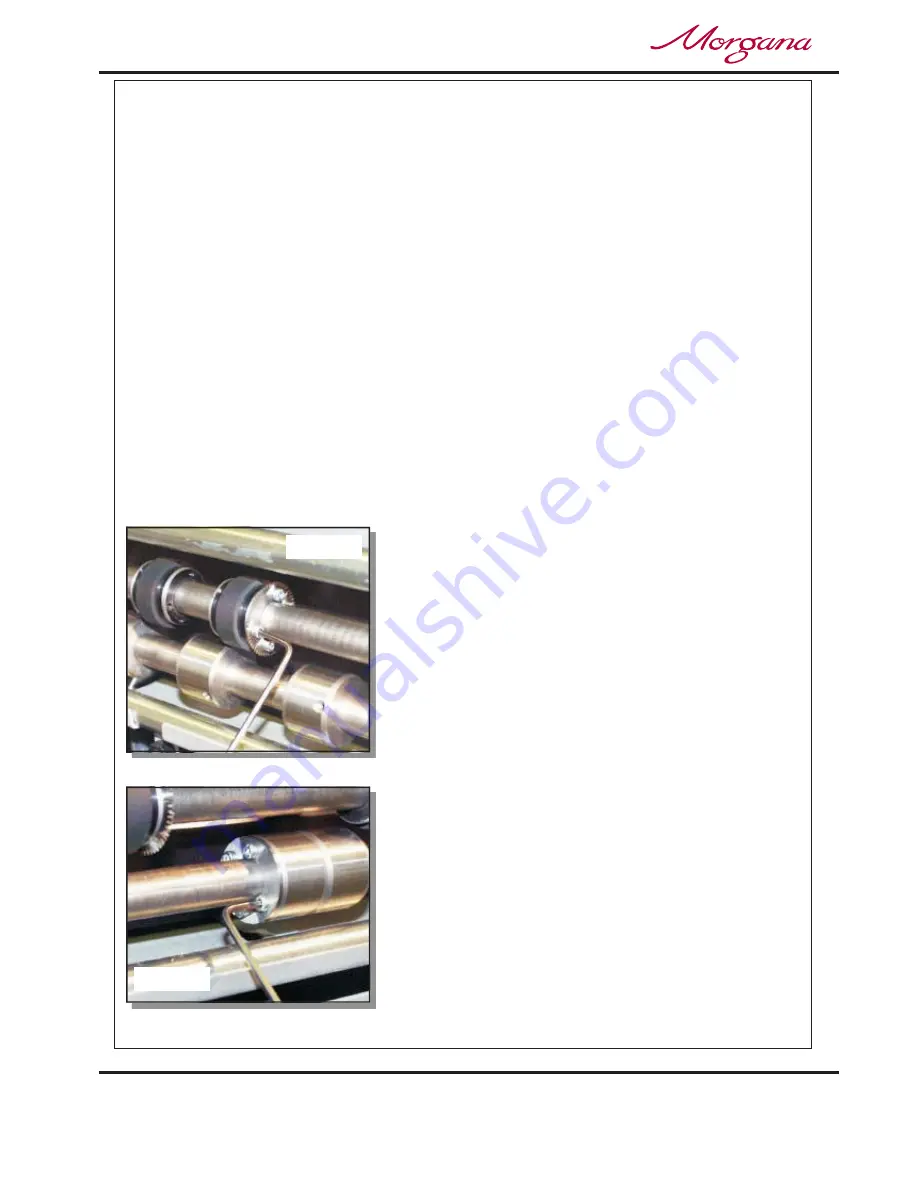
Page 40
Perforating
CREASING / BOOKLET MAKING
FIG 16.2
FIG 16.1
*Perforator stripper
78-013
All of the blades and anvils are supplied with fixings.
Standard Part Number
*It is recommended that for multiple perforations, a separate perforator stripper is used for
every perforating blade set fitted in the creasing unit.
1. Turn the mains supply to the machine ‘off’.
2. Remove the stacker unit and open the exit guard.
3. Locate and remove the blades / anvils from the despatch kit supplied with the
machine.
4. Using the 2mm allen key (supplied), loosen the drive wheel that is to accommodate
the blades.
5. Slide the drive wheel away from any obstructing drive wheels or hubs in order to
mount the blades.
6. Using the 2.5mm allen key (supplied), take one
half of the matching pair of blades and mount on
to the drive wheel. Do not secure the blade.
7. Mount the other half of the blade to the drive
wheel as shown (fig 35.1). Secure the blades to
the wheel ensuring not to over tighten grub screw.
8. Mark on a single sheet the desired perforating
position. Feed the sheet through the machine
manually until the mark can be seen. Use this
mark to assist in fixing the position of the
perforating drive wheel to the roller drive shaft.
9. Using the 2mm allen key, loosen the drive hub
nearest the perforating drive. Slide the drive hub
away from any obstructing drive wheels or hubs
in order to mount the anvils.
10. Using the 2,5mm allen key, take one half of the
matching pair of anvils and mount to the drive
hub. Do not secure the anvil.
Setting the machine