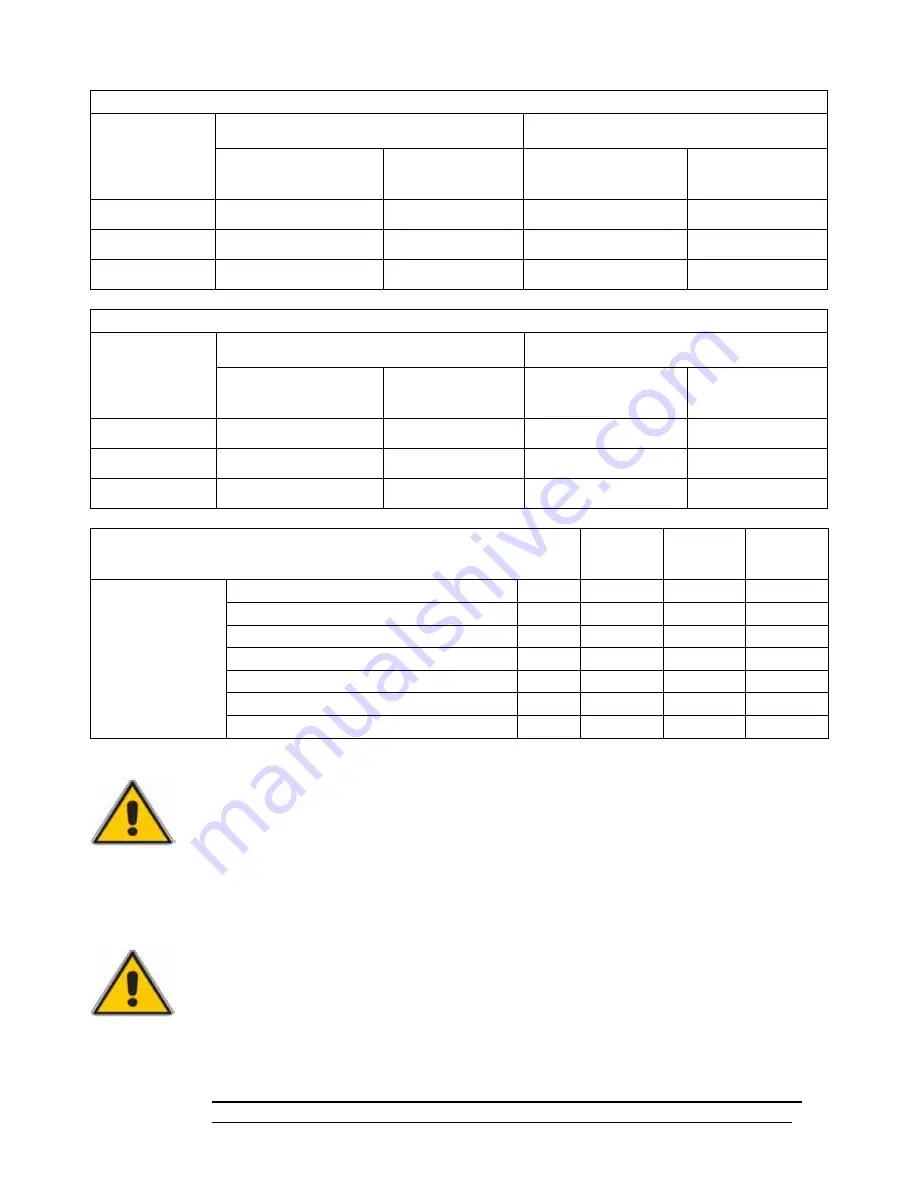
RANGE FGRi
MORELLO FORNI S. A. S.
11
3.5
TECHNICAL DATA
3.6 PREPARATION OF THE OVEN
The oven is a combustion model and must therefore be installed in adequately ventila-
ted areas or following the requirements specified in the current standards of competent
bodies.
3.7 OPERATING CHARACTERISTICS
The ovens manufactured by Morello Forni are preset to work with the type of gas spe-
cified in the order. To be able to use them with gases that are not specified on the table
supplied with the oven, it is first necessary to adapt them.
3.8 ADAPTING THE OVEN FOR ANOTHER TYPE OF GAS
This operation, which implies replacing the nozzles of the burner, must be performed
by a qualified and trained technician who will also have to annotate the new operating
characteristics of the oven after the applied changes. To request this kind of operation,
always refer to a qualified servicing technician of the manufacturer or an authorized dea-
ler.
AVOID TURNING THE OVEN ON IF THE OPERATING CHARACTERISTICS
DIFFER FROM THOSE STATED IN THE TEST TABLE SUPPLIED WITH IT!
BURNER ON THE BEDPLATE
Ref. / Mod.
DIAMETER OF BURNER
NOZZLE: 1/100 mm
POSITION OF MAIN AIR NOZZLE ON
MAIN BURNER: “X” mm
LIQUID GASG30/G31/
30/37 mbar
NATURAL GAS
G20 (20 mbar)
G25 (25 mbar)
LIQUID GASG30/G31/
30/37 mbar
NATURAL GAS
G20 (20 mbar)
G25 (25 mbar)
FGRi 100
1 X 200
1 X 280
6
8
FGRi 110
1 x 250
1 x 300
6
8
FGRi 130
2 X 160
2 X 260
2 X 10
2 X 10
BURNER ON THE DOME
Ref. / Mod.
DIAMETER OF BURNER
NOZZLE: 1/100 mm
POSITION OF MAIN AIR NOZZLE ON
MAIN BURNER: “X” mm
LIQUID GASG30/G31/
30/37 mbar
NATURAL GAS
G20 (20 mbar)
G25 (25 mbar)
LIQUID GASG30/G31/
30/37 mbar
NATURAL GAS
G20 (20 mbar)
G25 (25 mbar)
FGRi 100
3 x 150
3 x 250
3 x 8
3 x 10
FGRi 110
3 x 160
3 x 260
3 x 8
3 x 10
FGRi 130
4 x 150
4 x 250
4 x 10
4 x 10
Ref./ Mod.
FGRi 110 FGRi 130 FGRi 150
Nominal Heat
Mass of testing of fuel per hour
Kg/h
2,846
3,588
4,273
Average temperature exhaust gas
°C
151,35
153,75
157,62
exhaust flux
m
3
/h
314,60
396,824
472,39
Average satisfied CO at 13%O
2
%
0,188
0,2377
0,282
Absorbed heat
Kw
12,78
16,12
19,19
Nominal Heat delivered
Kw
3,91
4,94
5,88
Efficiency at nominal heat delivered
%
24,30
30,66
36,49