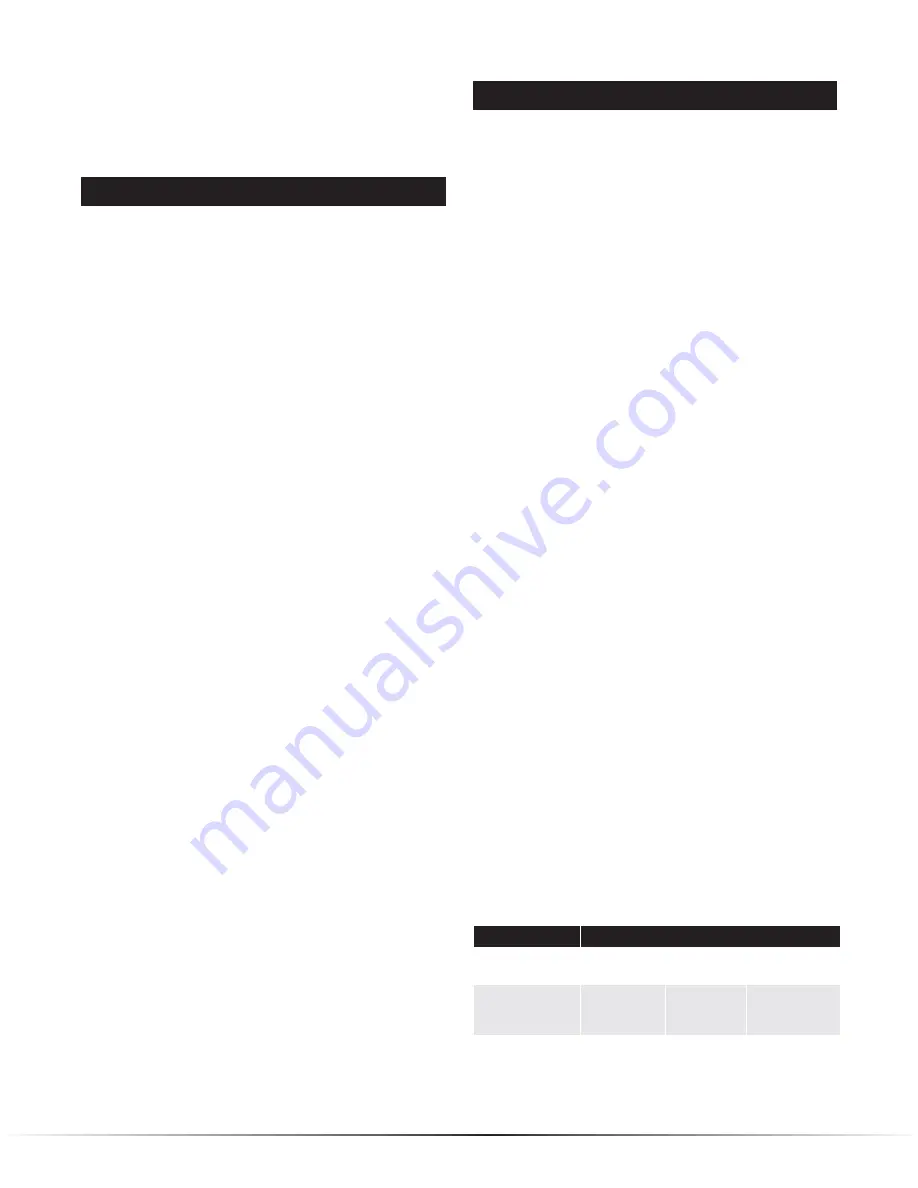
6
|
Dresser
Installation
WARNING
1. PERSONNEL:
Installation of the Flowgrid
®
valve/
regulator should be made by qualified personnel familiar
with high pressure piping and pilot operated regulators.
2. PRIOR INSPECTION:
Inspect the main valve, pilot,
and tubing for any damage that might have occurred in
shipping. Make sure the body, pilot lines, and inlet piping
are clear and free from foreign material.
3. ORIENTATION:
The Flowgrid
®
valve may be installed
in any position - the best position being one that
provides easiest access for pilot adjustment and valve
maintenance.
4. SCREWED END VALVES:
Apply pipe compound to the
male threads starting one or two threads back from the
end prior to assembling the joint.
5. FLANGED END VALVES:
Use suitable line gaskets and
good bolting practices with flanged bodies. A crisscross
pattern of incrementally tightening the line bolts is
recommended.
6. WELD END BODIES:
Remove the Spring Case and
all trim parts including diaphragm and O-rings before
welding a buttweld and/or a socket weld end Flowgrid
®
valve. Electric arc welding is recommended to minimize
heat build-up on the body assembly. Reassemble valve
(refer to the MAINTENANCE section of this manual for
Disassembly and Assembly procedures) and pressurize
with air to check for leaks prior to putting the valve in
service.
Personal injury, equipment damage, or leakage due to
explosion of accumulated gas or bursting of pressure
containing parts may result if this valve/ regulator is
overpressured or is installed where service conditions
could exceed the limits given in the specification of
this manual or on the nameplate, or where conditions
exceed any ratings of the adjacent piping or piping
connections. Verify the limitations of both valve and pilot
to ensure neither device is overpressured. To avoid such
injury or damage, provide pressure relieving or pressure
limiting devices (as required by Title 49, Part 192, of the
U.S. code of Federal Regulations, by the National Fire
Codes of the National Fire Protection Association, or
applicable codes) to prevent service conditions from
exceeding those limits. Additionally, physical damage
to the valve/regulator could break the pilot off the
main valve, causing personal injury and/or property
damage due to explosion of accumulated gas. To avoid
such injury and damage, install the regulator in a safe
location.
WARNING
Gas Regulators installed in confined or enclosed spaces
should be provided with adequate ventilation to prevent
the possibility of gas buildup or accumulation from
leaks and venting. Leaks or vented gas may accumulate
causing personal injury, death, or property damage.
Pilot spring cases and the regulator enclosure should
be vented to a safe area away from air intakes, or any
hazardous location. The vent lines and stacks must be
protected against condensation and clogging.
7. PILOT SUPPLY LINES:
Run a 3/8-inch or 1/2-inch pilot
supply line from the valve body connection on the inlet
side of the Flowgrid
®
valve to the pilot supply Filter or
directly to the pilot Restrictor.
NOTE: A shutoff valve is not required in the supply to the
pilot, but if one is installed it should be a full opening ball
valve type.
8. A TYPE 30 FILTER
in the pilot supply line is recom-
mended to clean dirt and other particulates that could
affect the restrictor or variable orifice in the pilot. Use
a 1/4” nipple to mount the filter to the body tap on the
Flowgrid
®
valve.
9. FILTER OUTLET:
Run 3/8 inch tubing or 1/4- inch
pipe from the filter OUTLET port to the INLET side of the
restrictor in the pilot system of the regulator. The TYPE
30/30A/30S FILTER has two OUTLET ports for ease of
tubing. Block the other port with the plug provided or
mount a gage to monitor inlet pressure if desired.
NOTE: To avoid galling when stainless steel to stainless
steel connections are made use a lubricant (such as
NEVER SEEZ by Bostik). For best results Lightly lubri-
cate the female threads. Mixing the lubricant with pipe
dope is also acceptable. Do not exceed more than 1/4
turn past the point the threads start to bind.
10. PILOT GAS HEATERS (OPTIONAL):
Pilot supply gas
can be heated to prevent the formation of ice or hydrates
in the pilot system. Pilot supply gas heaters should be
connected after the pilot filter (if one is used). Do not
directly heat to entire Flowgrid
®
valve to prevent freezing;
internal rubber components can be heated beyond their
max temperature rating causing potential damage.
11. CONTROL LINES:
Control lines should be run from
the pilot mounted on the Flowgrid
®
valve to a point 8 to
10 pipe diameters away from the valve (Refer to Piping
Schematics). Use Table 4 as a guide for the ideal tubing
to use. Reduce as necessary to connect to the pilot.
Outlet Pressure
Pilot Regulator
with:
Inches W.C. to
2 psi
2 psi to 5 psi
5 psi & above
Static Sense
Line (No
Flow)*
1/2” Pipe
minimum
1/2” Tubing
3/8” Tubing
Sense Line
with Flow*
3/4” to 1”
Pipe
1/2” Pipe
1/2” Tubing
*The Flowgrid
®
Series 20 Pilot has a static sense line.