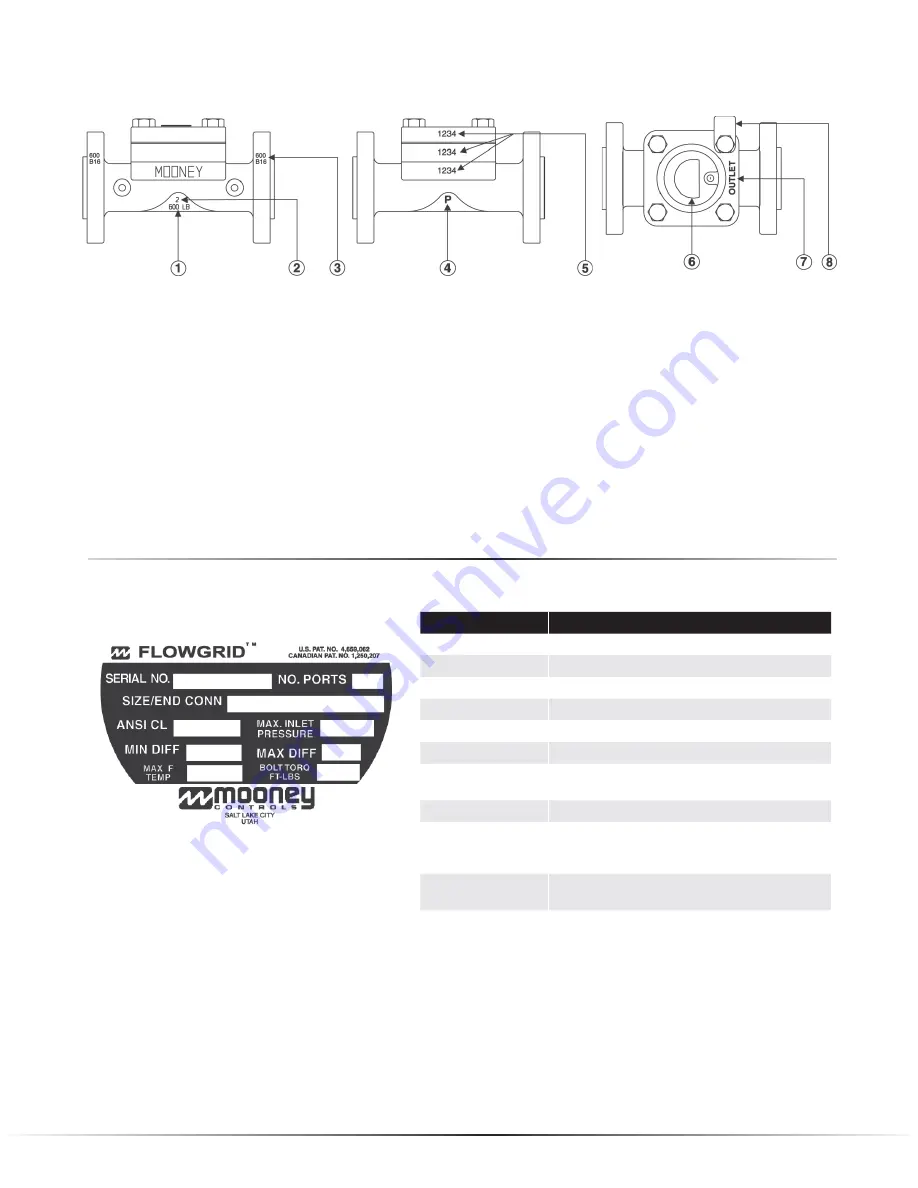
Front View
Back View
Top View
Flowgrid Regulator | 3
Valve Markings
Nameplate Information
1. American National Standards Institute (ANSI) pressure class rating of the valve.
2. Line size of body.
3. ANSI pressure class rating of the flange.
4. Indication that the valve has been hydrostatically tested according to code requirements.
5. The serial number is stamped on the spring case, spacer*, and Body.
6. The Nameplate location.
7. The flow direction is marked on the spring case (“INLET” or “OUTLET”). Proper alignment assures that the diaphragm
guide on the Spring Case is aligned toward outlet side of the valve.
8. The % Capacity tag indicates the capacity of the throttle plate (100%, 75%, 50%, & 35%) in the valve.
NOTE: On all 1” valves and 2” standard valves the throttle plate itself is stamped.
Item
Definition
Flowgrid
®
Registered name of valve
BLANK
CE Marking
SN
Serial number assigned to valve
FG
Flowgrid
®
Model description
SIZE/END CONN
Line size of bogy an type of end connection
ANSI CL
American National Standards Institute pressure class
MAX INLET
PRESSURE
Maximum inlet pressure (psig)
YR
Year manufactured
DIFF/MIN/MAX
Minimum differential required to fully open valve
Maximum allowable operating pressure differential
(psig)
MAX F
TEMPERATURE
Maximum Operating Temperature in degrees
Fahrenheit
BOLT TORQ FT-LBS
Recommended bolt torque for spring case in foot
pounds