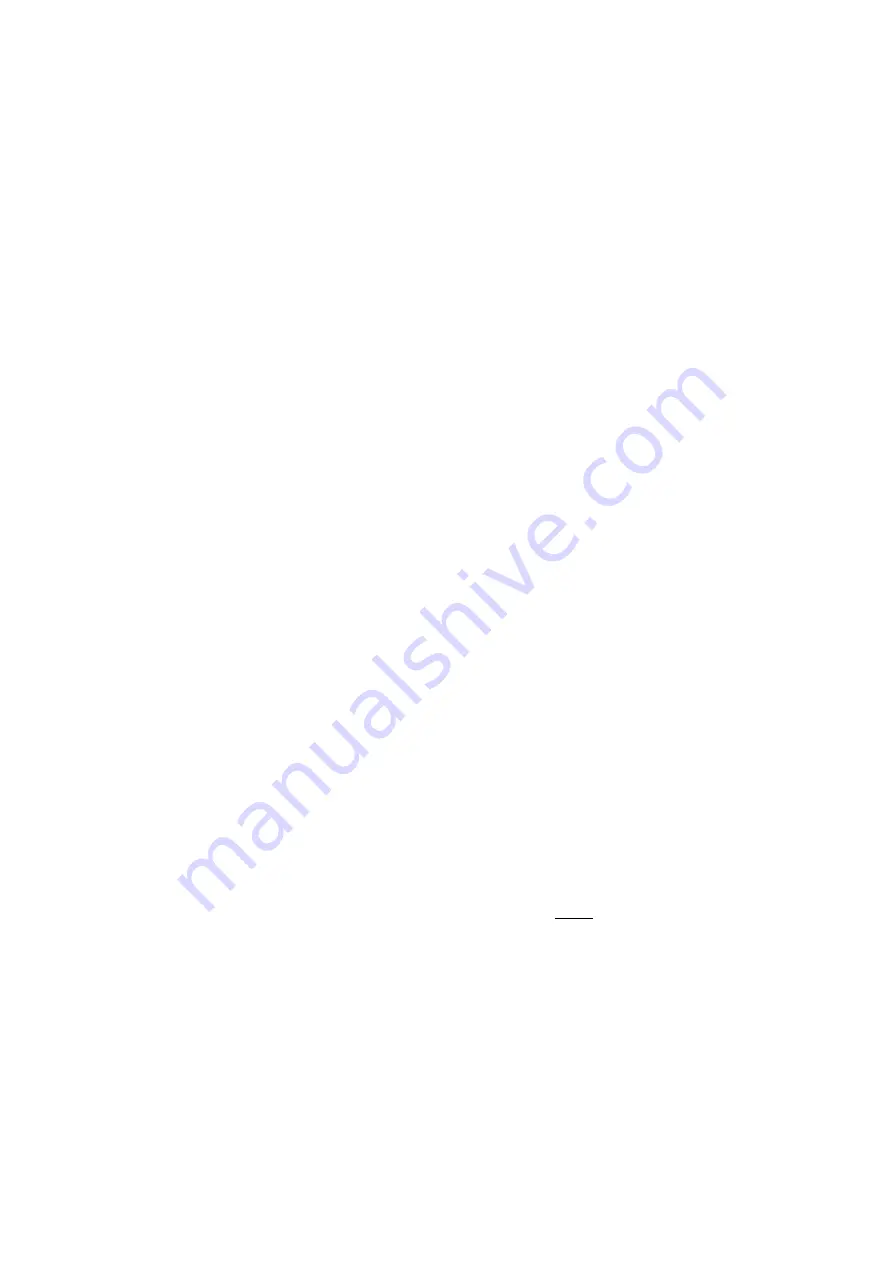
Adjust the feedback amp zero trimpot until the DMM reads
0.00V.
Set the variable supply to 4.80V.
Adjust the feedback gain trimpot until the DMM reads
-10.00V.
Set the variable supply to 0.96V again and check the
feedback test point is still 0.00V. Trim if necessary and check
the 4.80V setting again.
6.2 Input 1
An input to the error amplifier: This input is ±10V
non-inverting and has two important features:
It has a scale pot on its input that enables large inputs to be
scaled down to match smaller signals on other inputs. Scale
range is 10 to 100%. Set fully clockwise (FCW), an input of
100V can match a 10V signal on the other inputs. Note that
the maximum permissable input voltage is ±95V.
It has a switch selectable (SW4-2) lag of 55mS that can be
used to remove transients from the input signal that could
cause unwanted rapid movement in the output.
Input 1 is well suited to be a command because of these two
features. If input 1 is used for feedback, be sure the lag is
switched off. Input resistance after the scale pot is 94k Ohms.
6.3 Input 2
An input to the error amplifier: This input is non-inverting. It is
switch selectable (SW5) between 4-20mA and ±10V. The
4-20mA converter produces 0 to +10V for 4 to 20mA input.
R34 connects from the output of the converter to the input of
the servo amp when 4-20mA is selected. Plug-in input resistor
R34, of 100k Ohms, gives a nominal 0 to 10V input signal
range when V rather than 4-20mA is selected. Input 2 is
suitable for command or feedback. R34 can be increased to
give a larger input range.
6.4 Input 3
An input to the output summing and limiting amplifier via a
plug-in resistor, R33. A typical use for this input is command
feed forward. With R33 at 10k Ohm, a ±10V input will produce
±100% valve drive. Increasing R33 reduces the valve drive.
7 Output configuration
Select the output to match the input requirements of the valve
(SW2). When voltage (V) is selected, ±10V is available into a
minimum load of 200 Ohm. When current (I) is selected, the
current level switches (SW1-X) enable ±5 to ±100mA to be
selected. The switch selections sum, so, if for instance 45mA is
required, select 30,10 and 5. The output can drive all known
Moog valves up to ±100mA. The maximum load at
I
(Amp)
output is:
RL max =
11V – 39 Ohm
I
(Amp)
eg. at 50mA RL max is 181 Ohm
The output amplifier is limited to approximately 105% of the
selected full scale output. If both the proportional and
integrator stages are saturated, the output will not be twice
the selected full scale but still only 105% of full scale.
8 Step push button
The step push button (SW3) injects -50% valve drive
disturbance into the output. When released, the valve drive
reverts to its original level. This feature is useful for closed loop
gain optimisation.
Page 3 of 6: C70861 Rev A – 01.09
Feedback gain and zero pots: configured for 4-20mA input
Dither level pot: fully counter clockwise (FCCW)
Scale pot: FCCW
P gain pot: FCCW
I
gain pot: FCCW
Bias pot: 0V
Caution
If you intend to use the feedback amplifier adjusted for
4-20mA, don’t change the feedback gain or zero.
They are already adjusted for 4-20mA
To re-adjust for 4-20mA takes a little time, needs test
equipment and is tedious to do in the field.
6 Input configuration
Inputs 1, 2 and feedback go to the error amplifier and can be
used for feedback or command. Care needs to be taken in
selecting signal polarity to achieve negative feedback for
the overall closed loop. Since the input error amplifier sums
the signals, the transducer feedback signal needs to be the
opposite polarity of the command. This can be achieved in
two ways:
Arrange for an opposite polarity feedback transducer signal
and connect it to input 1, input 2 or the positive feedback
amplifier input.
If the feedback transducer signal is the same polarity as the
command, you only have one option: Connect it to the
negative input of the feedback amplifier.
6.1 Feedback input
An input to the error amplifier: The feedback amplifier is the
best choice for the feedback signal, for six reasons:
It leaves input 1 available for command. See 6.2 below.
It has inverting (negative) and non-inverting (positive) inputs.
It has zero and gain adjustment pots. This enables a signal
that does not go to zero volts and has less span than the
command, to be scaled up to the command. While this is
not essential, it helps when setting up and trouble-shooting.
There is a front panel test point for the zeroed and amplified
signal. This is very convenient (essential) for setting up and
trouble-shooting.
There is the option of a plug-in resistor, R16, to give a
feedback derivative (lead or D) in the output of the feedback
amplifier.
It can be set up for a current input by connecting a 240 Ohm
resistor between terminals 17 and 18 with the 4-20mA
switch ([SW1-4]).
Default
The feedback amplifier default set-up is 4-20mA flowing into
terminal 18 and out of terminal 17, producing an output of
0 to -10V. Reversing the terminals, and hence the current flow,
will not result in a 0 to +10V output. The feedback zero must
be adjusted for this arrangement.
Adjusting feedback amp for 4-20mA input and
0 to -10V output
Set the feedback gain to minimum (fully counter clockwise).
The trimpot has 15 turns and will click when minimum is
reached.
Connect terminal 17 to terminal 26 (ground).
Connect the positive of a variable DC power supply to
terminal 18 and the negative to terminal 26.
Connect a digital multimeter (DMM), on DC Volts, between
the front panel feedback amp and ground test points.
Set the variable supply to 0.96V.
(
)