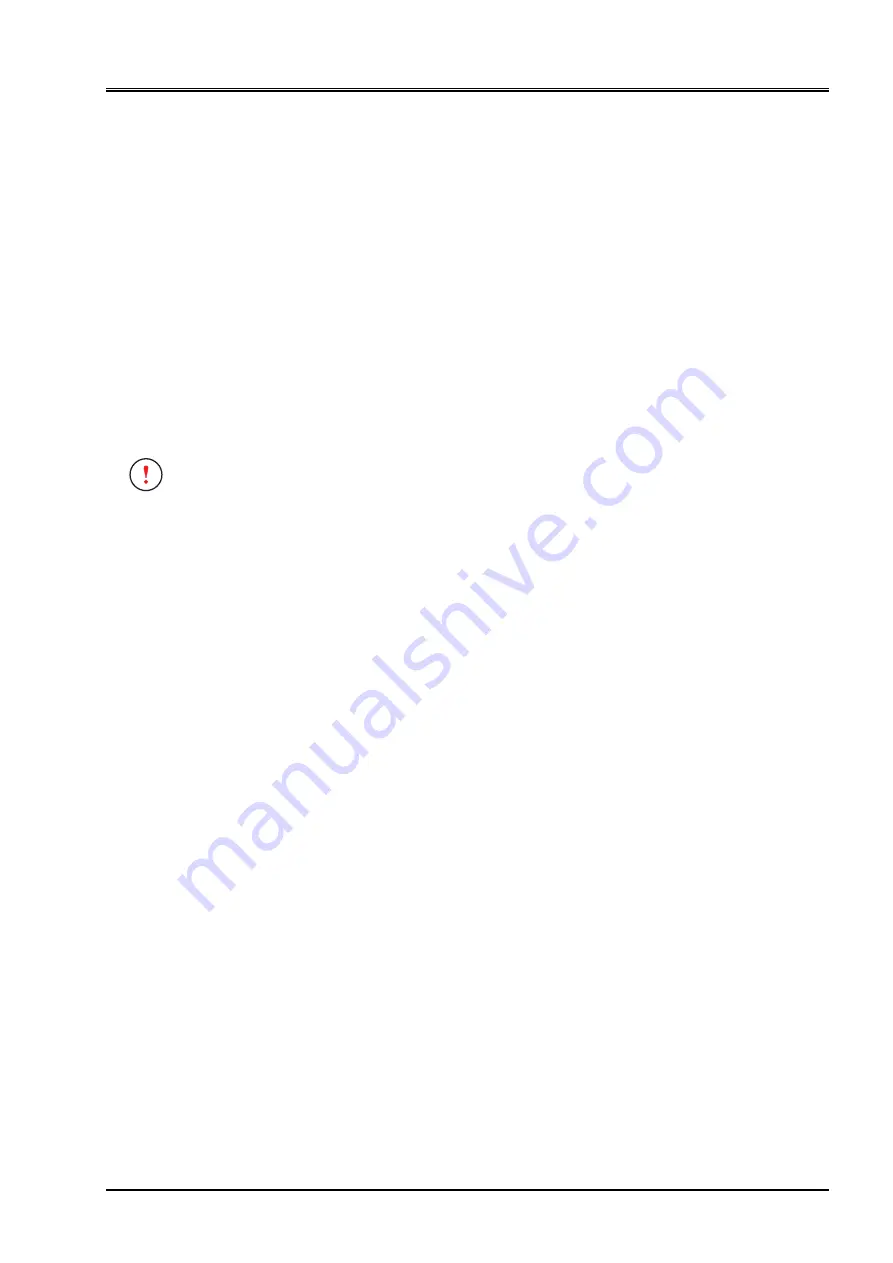
11 Service
Removing the valves
© Moog GmbH User Manual "D633-A Series" (CA80942-001; Version 1.0, 12/08) 57
11.1 Removing the valves
11.1.1 Tools and materials required
Tools and materials
required for removing
The following tools and materials are required for removing the valves:
• Torque wrench for hexagon socket head cap screws WAF 4
(for removing and mounting the valve)
• If necessary, replacement for port O-rings to be replaced
Chapter "13.2 Spare parts", page 66
• Shipping plate and associated fastening elements
• Flat-bladed screwdriver 8x1.6 [mm] and if necessary open-end
wrench WAF 8
(for mounting the shipping plate)
11.1.2 Procedure
Safety instructions:
Removing the valves
Procedure for removing
the valve
Procedure:
1.
Shut down and switch off the machine and place in a de-energized and
depressurized state.
2.
Release the valve’s installation screws.
3.
Remove the valve from the mounting surface.
4.
Check for presence, elasticity, integrity and correct seating of the O-rings
in the valve ports (A, B, P, T, etc.).
5.
Replace hardened and damaged O-rings with new O-rings.
6.
Mount the shipping plate to the valve’s hydraulic ports.
Tightening torque of the attachment screws:
approx. 5 Nm (3.7 lbf ft) (hand-tight)
7.
If the valve is not to be immediately reused or is to be serviced: Store the
valve in its original packaging.
Chapter "6 Transportation and Storage", page 33
8.
If necessary, block the ports of the hydraulic system to prevent the hy-
draulic fluid from being contaminated.
CAUTION
The valve shipping plate may only be removed from the valve
hydraulic ports directly prior to mounting and must be re-
mounted directly after the valve has been removed. This is the
only way of adequately protecting the valves against the in-
gress of dirt and moisture and protecting the seals against the
effects of ozone and UV.
The shipping plate and the associated fastening elements
(screws and nuts) must be kept for later use, e.g., during trans-
portation.