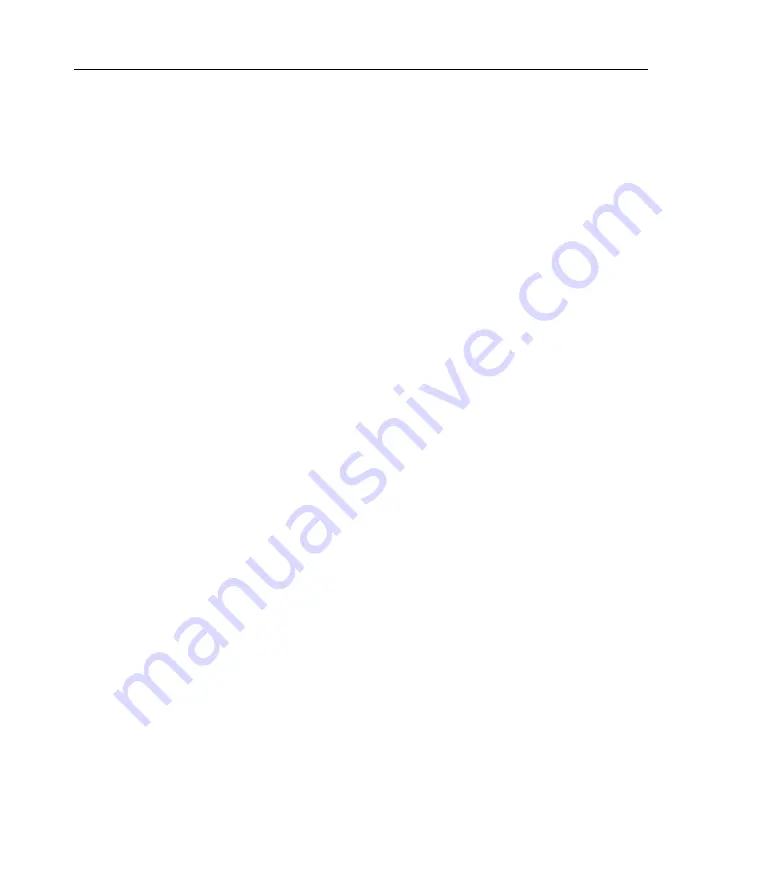
8
Chapter 3. First light
indicated on the controllers and specified by in the system test re-
port. Temperature stabilisation usually takes 5 to 10 minutes. De-
tailed
LDD
and
DLC
controller operation instructions are provided
separately in their associated user manuals.
5. The
TA
injection current should be chosen to provide between 10 mW
and 100 mW of output power, but no more than approximately 90%
of the
Maximum current, unseeded
(refer to customer test report).
Light emission should occur from the
TA
block output aperture.
NOTE:
TA
diode operation above
Maximum current, unseeded
with-
out an appropriately coupled seed laser will damage the diode.
6. For future reference, record a power
vs.
current (PI) curve for the
main output beam of the unseeded
TA
diode.
NOTE: Some power sensors (e.g. Si photodiode) have a highly
reflective surface. To avoid damage to the
TA
diode, ensure the
sensor is not close to normal incidence relative to the
TA
emission.
7. For
MSA
systems, power on the seed laser to a suitable current
according to the system test report and wait a minute for thermal-
isation. Record a PI curve for the free space output beam from the
MSA
seed. It should be similar to the PI curve in the system test
report (see test report figure
Seed power at TA input, pick off
). In-
structions for the seed laser operation are provided separately in the
CEL
or
LDL
user manual.
8. For further operation of
MSA
systems, proceed to chapter 4.
For further operation of
MOA
systems, proceed to chapter 5.
Summary of Contents for MOA
Page 4: ...ii ...
Page 14: ...4 Chapter 1 Introduction ...
Page 28: ...18 Chapter 4 MSA internal seed alignment ...
Page 36: ...26 Chapter 5 MOA external seed alignment ...
Page 40: ...30 Chapter 6 Output beam optimisation ...
Page 50: ...40 Chapter 7 Fibre coupling ...
Page 60: ...50 Appendix A Electrical connections ...
Page 63: ...53 MOA C compact amplifier 92 6 95 0 160 50 8 50 0 75 0 76 2 58 ...
Page 64: ......
Page 66: ......